The Cost of Sand Casting A Comprehensive Overview
Sand casting, one of the oldest manufacturing processes, remains a dominant method for producing metal parts and components across various industries. While this technique offers numerous benefits, including design flexibility and cost-effectiveness for small production runs, many potential users often ask, “How much does sand casting cost?” This article breaks down the factors influencing the overall cost and provides insights into budgeting for a sand casting project.
Understanding Sand Casting
Before delving into costs, let’s briefly understand what sand casting entails. This process involves creating a mold from sand, then pouring molten metal into that mold to produce the desired shape once it cools and solidifies. Sand casting is suitable for various metals, including aluminum, iron, and bronze, making it a versatile choice for many applications.
Factors Influencing Sand Casting Costs
1. Material Costs The type of metal used significantly impacts the overall cost of sand casting. Common metals like aluminum might be less expensive than specialized alloys or cast iron. Additionally, fluctuations in raw material prices can affect the estimated costs.
2. Mold Design and Complexity The complexity of the mold directly influences the cost. Simple designs require less time and fewer resources, resulting in lower costs. However, intricate designs may necessitate more advanced techniques and additional handling, leading to higher expenses. Furthermore, the need for cores, which are inserts used to create internal features, can add to the cost.
3. Production Volume The number of parts you plan to produce can also affect the cost per unit. Sand casting is generally more economical for low to medium production runs. Higher volumes may justify the initial setup costs, allowing for a decrease in the per-unit price as the fixed costs are spread over more units.
4. Labor Costs Skilled labor is essential for effectively executing sand casting operations. Labor costs can vary based on regional wage differences and the complexity of the project. Additionally, the required level of expertise in handling and finishing castings can influence the overall labor costs.
5. Post-Processing Most sand-cast parts require some level of post-processing, such as machining, polishing, or surface treatments. These additional processes can significantly affect the overall cost, especially if precision and surface finish are crucial for the final application.
how much does sand casting cost
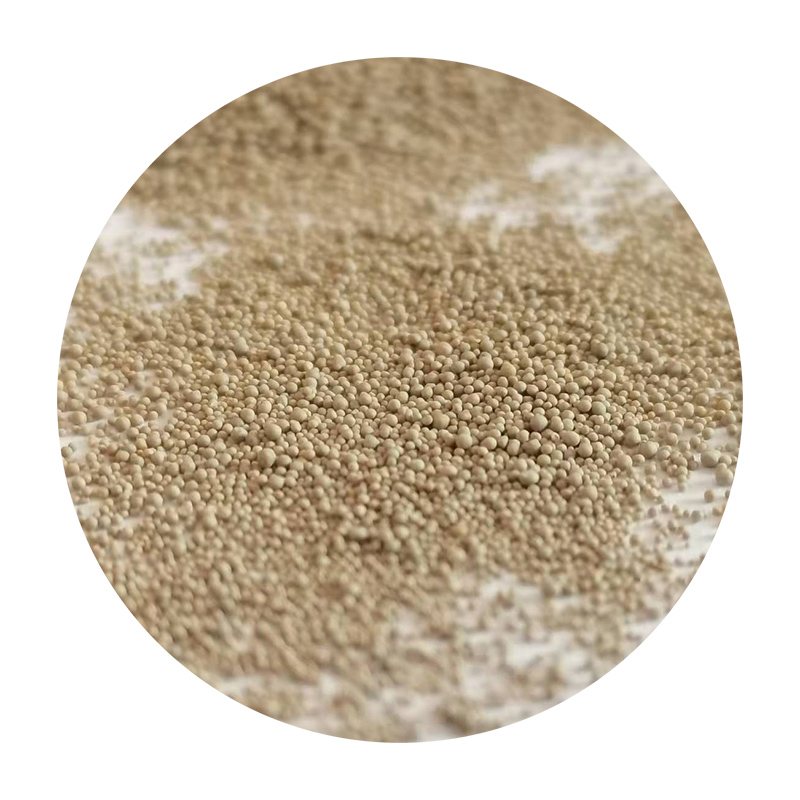
6. Setup Costs There are one-time setup costs associated with creating the mold, especially for custom designs. These costs include the creation of patterns, which can range from simple wooden patterns to complex CNC-machined patterns, depending on the precision needed.
Typical Cost Estimates
While costs can vary widely based on the factors mentioned, here are some general estimates to provide a basic understanding
- Setup Costs For a simple mold, setup costs can range from $1,000 to $5,000. More complex molds may cost anywhere from $5,000 to $20,000 or more. - Material Costs The cost of raw materials can range from $1 to $5 per pound, depending on the metal used and market conditions.
- Per-Unit Costs For a small run, expect to pay anywhere from $10 to $100 per unit, depending on the complexity and size of the casting.
- Post-Processing Costs These can add anywhere from $5 to $50 per unit, again depending on the level of finishing required.
Budgeting for Sand Casting
When budgeting for a sand casting project, it’s important to gather quotes from multiple foundries and to clearly define your project requirements. Consider not only the price but also the capabilities of the foundry in terms of quality control, material availability, and turnaround times. Developing a strong relationship with your supplier can lead to better pricing and service as you continue to produce parts.
Conclusion
In summary, the cost of sand casting can vary significantly based on various factors, including materials, design complexity, production volume, and required finishing processes. A thorough understanding of these elements will allow manufacturers to better estimate costs and optimize their budgets. By carefully selecting materials and working with experienced foundries, the benefits of sand casting can be effectively harnessed while managing expenses. Ultimately, investing time in planning and communication is key to a successful sand casting project, ensuring that the end product meets both expectations and budgetary constraints.
Post time:Oct . 17, 2024 12:13
Next:Coated Sand Applications and Benefits in Modern Industries and Construction Techniques