Understanding Coated Sand Applications and Benefits
Coated sand is an innovative material widely utilized in various industries due to its unique properties and enhanced performance characteristics. By applying a thin layer of resin or other coatings to conventional sand, the resulting coated sand exhibits improved strength, reduced permeability, and a range of additional benefits that make it suitable for various applications, particularly in the construction and composites sectors.
What is Coated Sand?
Coated sand is primarily produced by treating natural sand with a polymeric or chemically modified coating. This process involves the careful selection of sand particles based on size, shape, and cleanliness. After the sand is washed and dried, it undergoes a coating procedure where a resin or other binding material is evenly distributed on the surface of each grain. This results in a material that retains the fundamental properties of sand while offering enhanced performance features.
Key Benefits of Coated Sand
1. Improved Strength One of the significant advantages of coated sand is its increased strength and stability. The resin coating binds the sand particles together, reducing the likelihood of separation under stress. This property is particularly valuable in applications requiring high structural integrity, such as concrete production and sand casting.
2. Reduced Permeability Coated sand exhibits lower permeability than uncoated sand, which can be crucial in certain applications. In the construction industry, this characteristic helps prevent water infiltration and enhances the durability of structures. In foundry applications, it contributes to the production of high-quality molds that do not permit unwanted gas escape.
3. Reduced Dust Generation The coating process helps to minimize the amount of dust generated during the handling and mixing of sand. This reduction in dust not only creates a cleaner working environment but also improves safety for workers, as airborne particulates can pose health risks.
4. Customizable Properties The versatility of coated sand allows for customization of its properties based on specific application requirements. Different types of resins can be used to achieve desired characteristics such as flexibility, temperature resistance, and chemical stability.
coated sand
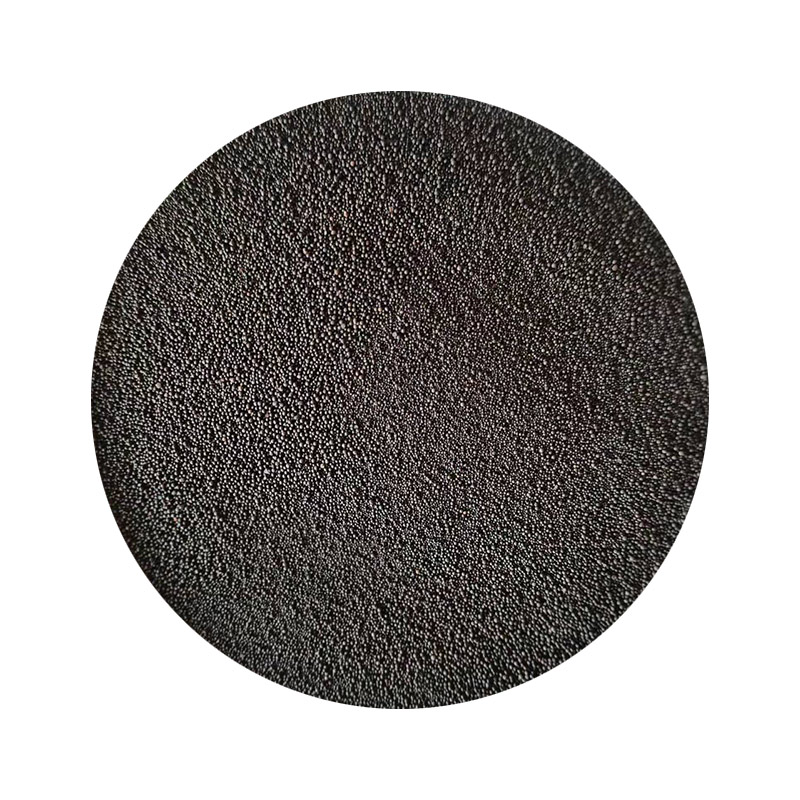
5. Environmentally Friendly Options With growing concerns around environmental sustainability, manufacturers are increasingly producing eco-friendly coated sands using bio-based resins. These alternatives provide a greener option without compromising performance, making them suitable for environmentally conscious projects.
Applications of Coated Sand
Coated sand finds utility in several industries, most notably in
- Construction In the construction sector, coated sand is often used for producing concrete and mortar due to its enhanced bonding properties and reduced water absorption rates.
- Foundries In metal casting, coated sand is employed to create molds and cores, ensuring high-quality finishes and precise dimensions in cast components.
- Oil & Gas In the oil and gas sector, coated sand is used in hydraulic fracturing processes. Its unique properties help improve fluid flow and ensure better permeability in reservoir stimulation.
- Sports and Recreation Coated sand is also used in synthetic turf systems, providing excellent drainage and improved performance characteristics for sports fields and recreational areas.
Conclusion
Coated sand represents a significant advancement in material science, offering numerous benefits that enhance performance across various applications. Its ability to improve strength, reduce permeability, and minimize dust generation makes it a valuable component in industries ranging from construction to manufacturing. As technology continues to develop, coated sand is likely to play an increasingly vital role in promoting sustainable and efficient practices across multiple sectors. Whether through improved performance or environmental considerations, coated sand is poised to remain at the forefront of material innovations for years to come.
Post time:Oct . 17, 2024 11:50
Next:zandgietijzer