Types of Sand Used in Foundry
In the world of metal casting, sand molds play a crucial role in shaping metal into desired forms. The type of sand used in foundry operations significantly influences the quality of the final product as well as the efficiency of the casting process. Understanding the various types of sands and their properties is vital for manufacturers aiming to achieve precise and durable castings.
1. Green Sand
Green sand is perhaps the most commonly used type of foundry sand. It is a mixture of silica sand, clay, and water. The term “green” refers to the fact that the sand molds are damp when formed, not dry. The clay content, usually bentonite, provides the necessary binding properties, allowing the sand to hold its shape when subjected to molten metal. Green sand molds are preferred for their excellent casting characteristics including high strength, good thermal conductivity, and the ability to withstand metal pouring. They are commonly used in the production of both ferrous and non-ferrous castings.
2. Dry Sand
Dry sand is another type commonly utilized in foundries, particularly where higher casting precision is required. It is composed of silica sand with a low moisture content, ensuring that the mold cures faster and offers a fine surface finish. While dry sand molds are less forgiving than green sand molds, they allow for better detail reproduction in intricate designs. Dry sand is often used for casting aluminum and other non-ferrous metals due to its improved finishing qualities.
types of sand used in foundry
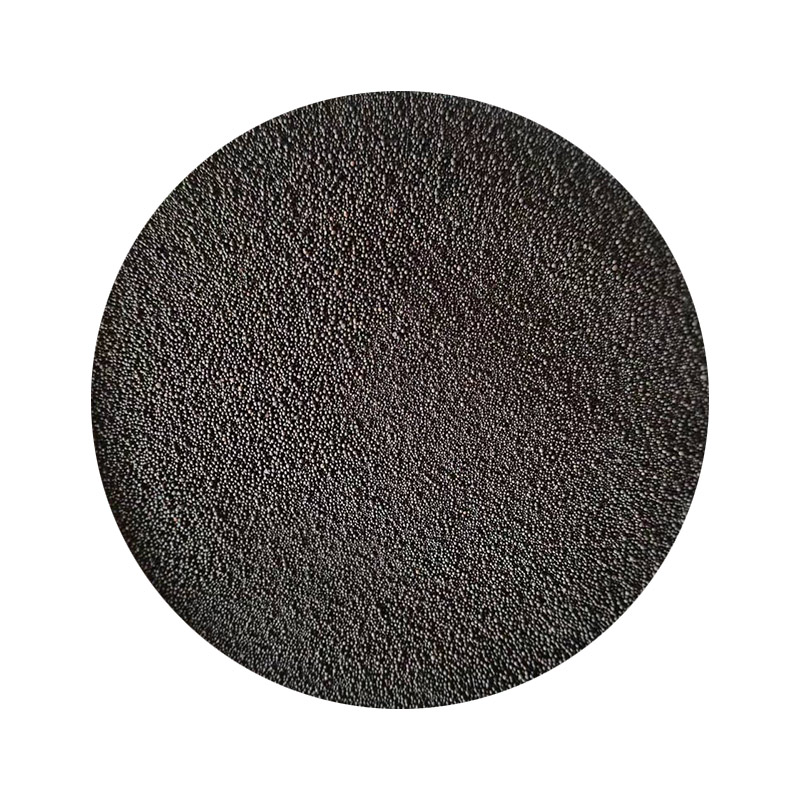
Synthetic sand, also known as resin sand, has gained popularity in modern foundry practices. This type of sand is engineered from silica and is typically coated with a resin that serves as a binder. The main advantage of synthetic sand is its ability to create molds that are remarkably strong and resilient, minimizing defects in the casting. Moreover, synthetic sand can be reused multiple times, leading to lower material costs and reduced waste. Manufacturers often prefer it when precision and surface quality are pivotal requirements.
4. No-Bake Sand
No-bake sand is a versatile type that uses a chemical binder which hardens at room temperature rather than needing to be baked. This allows for more intricate, larger, and heavier castings. The significant advantage of no-bake processes is their capability of producing high-quality molds without relying on high-temperature curing. This versatility makes it suitable for both ferrous and non-ferrous metal castings.
5. Lost Foam Sand
Lost foam casting is a process where expanded polystyrene (EPS) foam patterns are used, making it a unique component in foundry operations. The mold is made from dry sand, which is then packed around the foam pattern. As molten metal is poured, the foam evaporates, leaving an exact replica of the pattern in the sand. This technique allows for the casting of complex shapes and details with minimal additional finishing work.
Conclusion
The right type of sand is essential for efficient and effective foundry operations. Each type has its specific advantages and applications, depending on the desired outcome and the properties of the metal being cast. Whether it is the traditional green sand or the advanced synthetic sand, the choice shapes the quality, durability, and production costs of metal castings. As technology continues to evolve, the foundry industry adapts and incorporates new materials and methods, paving the way for more innovative and sustainable casting practices. Understanding the characteristics of different sands helps foundries optimize their processes and deliver superior products to their clients.
Post time:Jul . 21, 2024 01:03
Next:Understanding the Benefits and Applications of Resin Coated Sand in the Foundry Industry