Different Types of Sand Casting
Sand casting is a versatile and widely used metal casting process that involves pouring molten metal into a mold created from sand. This method is favored for its capability to produce complex shapes and sizes, making it applicable across various industries, including automotive, aerospace, and consumer goods. Within the realm of sand casting, several types allow for customization depending on the specific needs of production. In this article, we'll explore the five main types of sand casting green sand casting, resin sand casting, plaster sand casting, investment sand casting, and lost foam casting.
1. Green Sand Casting
Green sand casting is the most traditional and commonly used method. It involves a mixture of sand, clay, and water to create molds. The term green refers to the fact that the mold is not baked or hardened; instead, it retains moisture. This method is cost-effective and ideal for high-volume production. Green sand molds are reusable and easy to shape, making them suitable for simple and moderate complexity designs. The process allows for fast cooling and good dimensional accuracy, making it perfect for automotive parts and machine components.
Resin sand casting utilizes a mixture of sand and resin, which is cured using heat or a chemical reaction. This method results in a stronger and more durable mold compared to green sand casting. Resin sand molds can achieve finer details and a smoother finish, which minimizes the need for extensive post-casting machining. This method is ideal for producing complex shapes and is increasingly utilized in industries that demand high precision, such as aerospace and medical equipment manufacturing.
3. Plaster Sand Casting
different types of sand casting
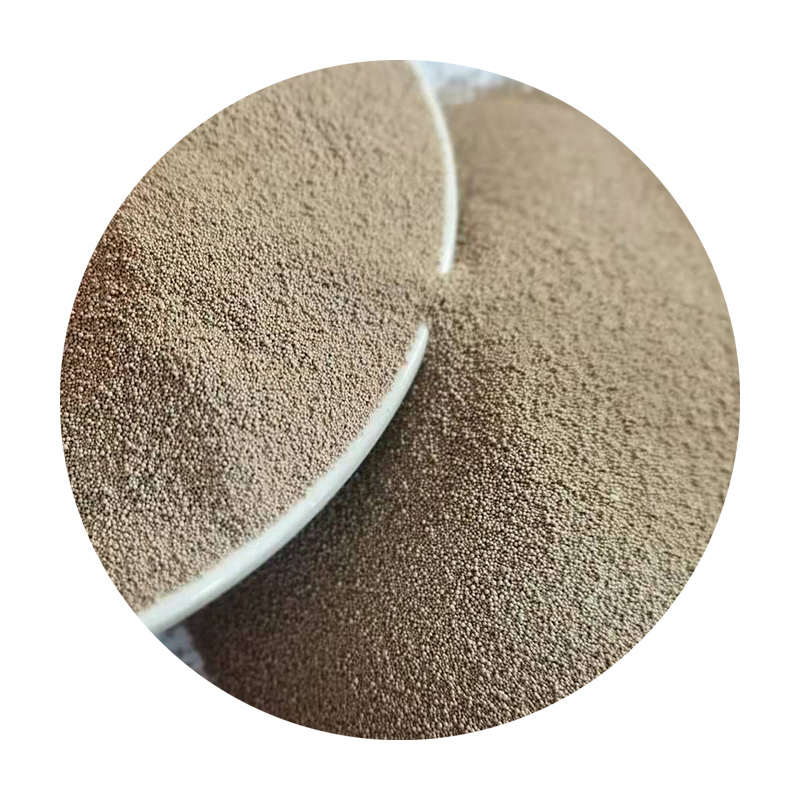
Plaster sand casting is a unique variation that utilizes plaster of Paris as the binding agent instead of clay. This method is particularly suitable for producing intricate components that require a high level of detail and a fine surface finish. The plaster molds are created by mixing sand with gypsum plaster, which is then allowed to set. Once cured, these molds can endure the heat of molten metal, making them applicable for casting aluminum and other non-ferrous metals. Plaster sand casting is prevalent in artistic applications and for prototyping.
4. Investment Sand Casting
Investment sand casting, often referred to as investment casting or lost wax casting, involves creating a wax pattern that is coated with a ceramic shell. Once the shell is formed, the wax is melted out, leaving behind a cavity that is filled with molten metal. This method allows for exceptional accuracy and repeatability, making it ideal for complex geometries and fine details. While investment sand casting can be more costly due to the extensive preparation and material costs, the precision it offers justifies the investment for specialized applications, such as turbine blades and intricate machinery parts.
5. Lost Foam Casting
Lost foam casting is a relatively modern method that involves creating a mold from a foam-pattern which is coated in sand. When molten metal is poured into the mold, it vaporizes the foam, leaving an exact replica of the pattern. This method is favored for its ability to produce parts with complex shapes and minimal material waste. Its unique characteristics make it especially suitable for large castings in the automotive and heavy machinery sectors.
Conclusion
Each type of sand casting offers distinct advantages and is suited for different applications. From the economical and versatile green sand casting to the intricacies of investment casting, manufacturers can choose the method that best fits their design specifications and production requirements. As technology and materials continue to advance, sand casting methods will likely evolve, further expanding their potential uses in various industries. Understanding these different casting processes is essential for engineers and designers alike, ensuring they choose the most appropriate technique for their specific needs.
Post time:Jul . 20, 2024 11:47
Next:Exploring the Benefits and Applications of Cerabeads Sand in Various Industries