The Versatility of Cerabeads Sand A Closer Look
In modern industry, the quest for innovative materials that enhance efficiency and sustainability is ever-present. One such material that has gained attention is Cerabeads sand, a unique synthetic microsphere that offers numerous applications across various sectors. This article delves into the properties, advantages, and applications of Cerabeads sand, exploring why it has become a preferred choice in many industries.
What are Cerabeads Sand?
Cerabeads sand is a type of synthetic sand made from aluminosilicate, a compound derived from natural minerals. The production process involves meticulously controlling the heating and cooling of materials to create spherical beads that exhibit a uniform size and shape. These microspheres possess a smooth surface, high thermal stability, and remarkable resistance to chemical attack. The unique structure and properties of Cerabeads are what set it apart from conventional sand.
Outstanding Properties
One of the most notable characteristics of Cerabeads sand is its exceptional thermal stability. With a melting point exceeding 1,200 degrees Celsius, Cerabeads can withstand high temperatures without losing their structural integrity. This makes them ideal for applications in industries such as metal casting, where they can be used as a sand mold or core material. Additionally, their smooth surface decreases friction, leading to easier handling and improved flow characteristics when used in molds.
Moreover, Cerabeads sand is chemically inert, meaning it does not react with the various metals and chemicals it may encounter in industrial processes. This property ensures that Cerabeads do not contaminate products, maintaining high-quality standards in manufacturing.
Advantages of Using Cerabeads Sand
The use of Cerabeads sand offers numerous advantages. Firstly, they are environmentally friendly. Unlike natural sands, which are often mined in ways that can be detrimental to the environment, Cerabeads can be produced from recycled materials, reducing the carbon footprint associated with their production.
cerabeads sand
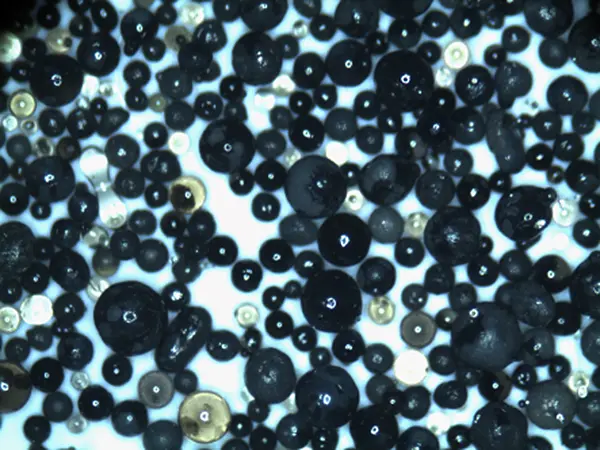
Secondly, their reusability is a significant benefit. In conventional sand casting processes, a large volume of sand is discarded after use. However, Cerabeads can be cleaned and reused multiple times, leading to cost savings for manufacturers and minimizing waste.
In addition to cost efficiency, Cerabeads sand improves the overall quality of finished products. They create smoother surfaces and more precise mold shapes, resulting in fewer defects and reduced post-processing requirements.
Applications Across Various Industries
The versatility of Cerabeads sand allows it to be utilized in a wide array of applications. In the foundry industry, they are extensively used as a mold and core material in metal casting, where their ability to endure high temperatures and minimize defects enhances product quality.
In the construction sector, Cerabeads are employed as lightweight aggregate in concrete, improving insulation properties and reducing the overall weight of structures. This usage not only aids in energy efficiency but also offers better seismic performance in buildings.
Moreover, Cerabeads sand finds applications in the field of electronics, particularly in the manufacturing of semiconductors and other precision components. Their fine, uniform granules help create stable and reliable molds essential for high-tech products.
Conclusion
Cerabeads sand represents a significant advancement in material science, combining functionality, sustainability, and efficiency. As industries continue to seek innovative solutions to address challenges in production and environmental impact, Cerabeads sand stands out as a preferred material, promising enhanced performance across various applications. With its unique properties and versatility, Cerabeads sand is poised to play a vital role in shaping the future of manufacturing and construction. As we embrace these advanced materials, the benefits they bring to the table cannot be understated, paving the way for a more sustainable industrial landscape.
Post time:Jul . 20, 2024 11:46
Next:Techniques for Smoothing and Finishing 3D Printed Resin Models to Achieve Professional Results