Sand Casting A Time-Honored Technique in Metal Fabrication
Sand casting is one of the oldest and most widely used metal fabrication processes, embodying a blend of artistry and engineering that dates back thousands of years. This versatile casting method offers numerous advantages, making it an essential technique in various industries, including automotive, aerospace, and art.
At its core, sand casting involves creating a mold from sand that is compacted around a pattern—typically made of metal, wood, or plastic—that represents the object to be cast. The pattern is first placed in a sand mixture that may include clay and water to help hold the shape. Once the pattern is removed, it leaves a cavity in the sand, which is then prepared to hold the molten metal.
Sand Casting A Time-Honored Technique in Metal Fabrication
The process also scales well for both small and large production runs. For instance, single items or small batches can be efficiently produced for custom applications, such as artistic sculptures or machinery components. Conversely, sand casting can also be set up for high-volume production by creating multiple molds and patterns, enabling manufacturers to meet the demands of mass production while still providing the flexibility to make design alterations.
sand cast metal
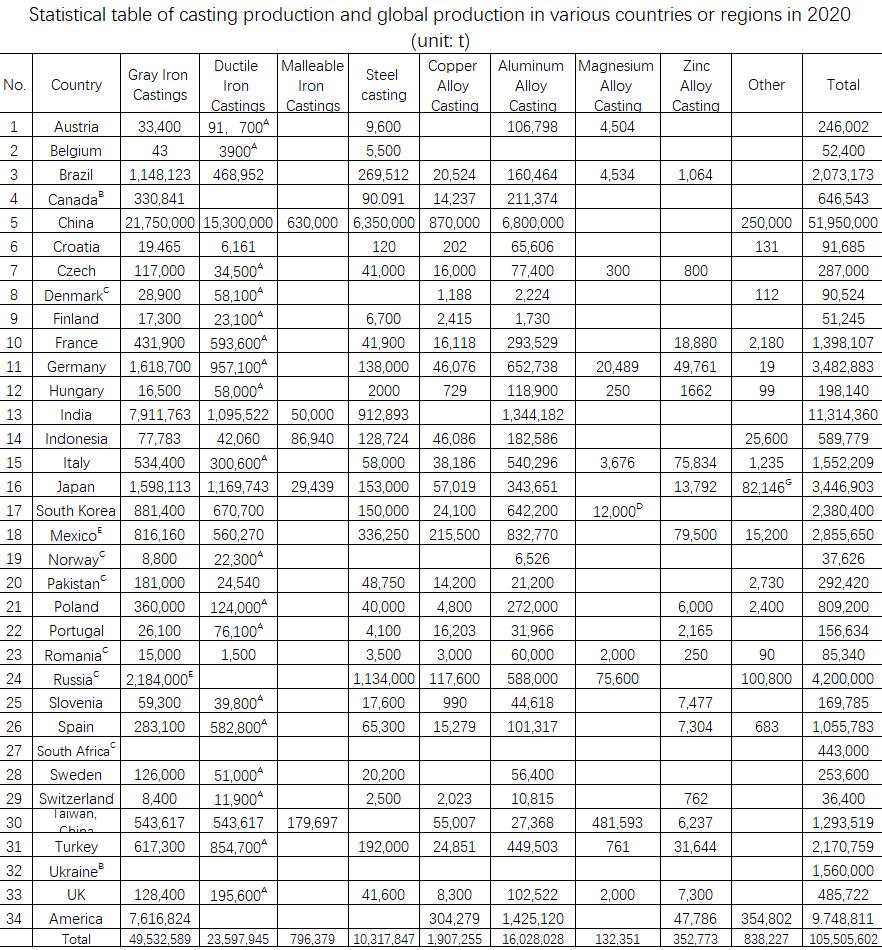
Another critical advantage of sand casting is its cost-effectiveness. The raw materials required for sand molds are relatively inexpensive, and the process itself does not necessitate elaborate equipment, making it accessible for small workshops and large foundries alike. Moreover, sand molds can be reused for multiple casting cycles, further improving the economic efficiency of the process.
However, sand casting is not without its challenges. The quality of the molded item can be influenced by several factors, such as the sand composition, the pattern design, and the pouring techniques. Besides, surface finish is a typical concern, as sand cast products may exhibit rough textures that require further machining or treatment to achieve the desired aesthetic or functional qualities.
To address these challenges, advancements in technology have been integrated into traditional sand casting processes. Innovations such as computer numerical control (CNC) machining, additive manufacturing for pattern creation, and improved sand compaction methods have enhanced both accuracy and finish quality. These improvements have expanded the capabilities of sand casting, allowing for the production of intricate designs and tighter tolerances that were once difficult to achieve.
In conclusion, sand casting is a remarkable method of metal fabrication that has stood the test of time. Its ability to accommodate various metals, combined with low production costs and adaptability for different scale operations, makes it an invaluable tool across many industries. As technology continues to advance, sand casting is poised to evolve further, allowing for innovations in design and production that will keep this ancient craft relevant in a modern context. Whether creating a complex aerospace component or a simple artistic piece, sand casting remains a vital process that connects the past with the future of manufacturing.
Post time:Jul . 28, 2024 10:47
Next:Exploring Innovative Uses and Advantages of Lost Foam Casting in Modern Manufacturing Processes