Lost Foam Casting Applications An Overview
Lost foam casting (LFC) is a sophisticated and innovative metal casting technique that offers numerous advantages in various industrial applications. Unlike traditional casting methods, lost foam casting utilizes a foam pattern that evaporates during the metal pouring process, allowing for the creation of complex shapes and precision parts. This article will delve into the diverse applications of lost foam casting, highlighting its benefits and impact on modern manufacturing.
Lost Foam Casting Applications An Overview
In addition to automotive applications, lost foam casting is widely used in the aerospace sector. Components for aircraft, such as turbine housings, brackets, and landing gear parts, require high precision and low weight to ensure optimal performance during flight. The LFC process allows aerospace engineers to achieve the tight tolerances necessary to meet regulatory standards while also producing lightweight structures that can withstand extreme conditions. The development of advanced alloys and ceramics in lost foam casting further enhances the material properties, making it an excellent choice for critical aerospace components.
lost foam casting applications
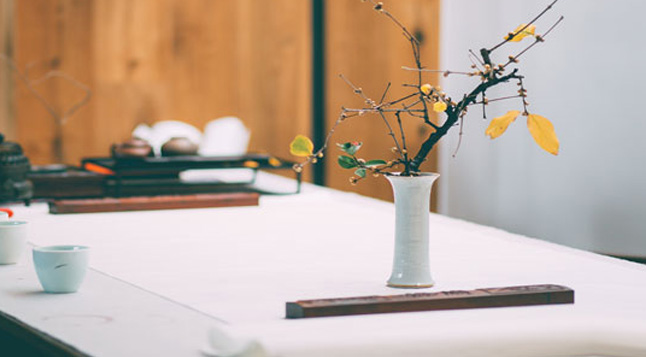
Another significant application of lost foam casting is in the manufacturing of industrial machinery and equipment. Heavy machinery often requires cast components that can bear high loads and resist wear. LFC can produce complex shapes that traditional casting methods might struggle with, allowing for optimized designs that enhance the overall performance and durability of machines. This technology supports the manufacturing of components like gear housings, pump casings, and structural parts, all while maintaining cost-effectiveness and efficiency.
The use of lost foam casting is also expanding into the field of art and sculpture. Artists and designers are increasingly utilizing LFC to create intricate metal sculptures and one-of-a-kind pieces. The ability to produce highly detailed patterns without the need for molds opens new avenues for creative expression. Artists can experiment with various materials, including aluminum, bronze, and iron, to create stunning works that reflect their vision while benefiting from the efficiency of modern casting techniques.
Additionally, lost foam casting is gaining traction in the production of renewable energy components, particularly in wind and solar energy applications. For instance, LFC is employed to manufacture wind turbine components such as housings and brackets that must be both lightweight and durable. The precision offered by this method ensures that these components can withstand environmental stressors while maintaining their structural integrity over time.
In conclusion, lost foam casting presents a versatile solution for a variety of industrial applications, including automotive, aerospace, heavy machinery, art, and renewable energy. Its unique advantages—such as the ability to create complex geometries, reduce material waste, and improve manufacturing efficiency—make it an attractive option for modern production needs. As technology advances and industries continue to push the boundaries of design and functionality, lost foam casting is poised to play an increasingly vital role in the future of manufacturing.
Post time:Jul . 28, 2024 09:51
Next:Innovative Techniques and Benefits of Iron Sand Casting for Modern Manufacturing Applications