The Resin Coated Sand Process Enhancing Foundry Operations
The resin coated sand process has revolutionized the foundry industry by providing a superior method for producing high-quality castings. This innovative technique addresses many of the traditional challenges faced by foundries, offering improved strength, durability, and surface finish to cast products. In this article, we will explore the resin coated sand process, its advantages, applications, and its impact on the foundry industry.
Understanding the Resin Coated Sand Process
At its core, the resin coated sand process involves the coating of sand grains with a thermosetting resin binder. The key steps in this process include the preparation of sand, mixing it with resin, curing, and forming. Initially, high-quality silica sand is washed and dried to remove impurities and ensure optimal performance. Once prepared, the sand is mixed with a specific type of resin, usually phenolic or furan, in a controlled environment to achieve uniform coating.
Following this mixing phase, the resin coated sand is cured at elevated temperatures. This curing process initiates a chemical reaction that hardens the resin, creating a strong bond between the sand grains. The result is a composite material that exhibits excellent strength and resilience, making it suitable for various casting applications. The coated sand can then be utilized in the mold-making process, allowing foundries to produce intricate designs with high levels of precision.
Advantages of Resin Coated Sand
The primary advantage of using resin coated sand is its ability to produce high-quality castings with finer surface finishes. The smoothness of the resin-coated grains creates molds that capture intricate details, reducing the need for excessive post-processing. This benefit translates to lower labor and finishing costs, boosting efficiency in the foundry.
resin coated sand process
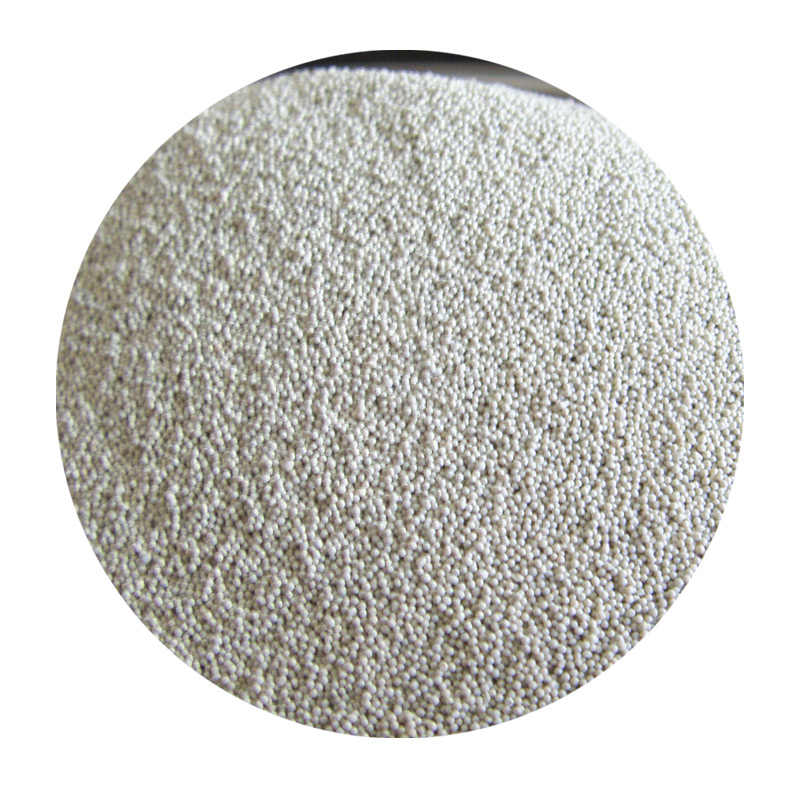
Another significant advantage lies in the mechanical properties of resin coated sand. The strong bond formed between the grains enhances the overall strength of the molds, allowing them to withstand the pressures of molten metal. This durability reduces instances of mold failure and defects in castings, leading to increased production yield and reduced scrap rates.
Additionally, resin coated sand exhibits excellent thermal stability, allowing it to endure high temperatures without compromising its structural integrity. This characteristic is particularly beneficial in the casting of various metals, including aluminum, iron, and steel, enabling foundries to expand their capabilities.
Applications in the Foundry Industry
Resin coated sand is utilized in a wide range of applications within the foundry industry. Its versatility makes it suitable for both ferrous and non-ferrous metal casting, with significant usage in automotive, aerospace, and heavy machinery production. The precise nature of the molds created using this process allows for complex geometries that would be challenging to achieve with traditional sand casting methods.
Moreover, its efficiency in producing high-quality molds has led to its adoption in prototype development and low-volume production runs, where quick turnaround times are essential. The ability to create consistent and repeatable results positions resin coated sand as a preferred choice for foundries aiming to meet the demands of a competitive market.
Conclusion
The resin coated sand process represents a significant advancement in casting technology, providing foundries with an effective solution to enhance the quality and efficiency of their operations. By offering improved surface finishes, mechanical properties, and thermal stability, it addresses many of the limitations associated with traditional sand casting techniques. As the foundry industry continues to evolve, the resin coated sand process is likely to play an integral role in shaping the future of casting, enabling manufacturers to produce complex, high-quality components to meet the growing demands of various industries.
Post time:Jul . 25, 2024 14:13
Next:The Time Required for Sand Casting Process and Factors That Influence It