The Role of Sand in Foundry Applications
In the realm of metal casting, the use of sand has been an age-old practice, dating back thousands of years. Foundries, which are facilities where metal casting occurs, rely heavily on sand to create molds for various metal components. The significance of sand in foundry applications cannot be overstated; it serves as the backbone of the casting process, influencing the quality, precision, and efficiency of metal production.
Types of Sand Used in Foundries
The primary sand used in foundry operations is silica sand, known for its high melting point and excellent thermal properties. This type of sand provides the necessary strength and durability required to withstand the high temperatures involved in metal casting. In addition to silica sand, other types may include olivine sand, zircon sand, and chromite sand, each offering unique properties suitable for specific casting applications. For instance, olivine sand is often chosen for its high thermal stability, making it ideal for certain ferrous alloys.
Sand Casting Process
The sand casting process begins with creating a mold, typically in two halves the cope (top half) and the drag (bottom half). A mixture of sand, clay, and water is compacted around a pattern of the desired object. This mixture is crucial; the composition affects the mold's strength, cohesiveness, and permeability. Once the mold is prepared, the pattern is removed, leaving behind a cavity into which molten metal is poured. The sand mold holds the shape of the pattern and, after the metal solidifies, is broken away to reveal the final cast product.
Advantages of Sand as a Material
sand used in foundry
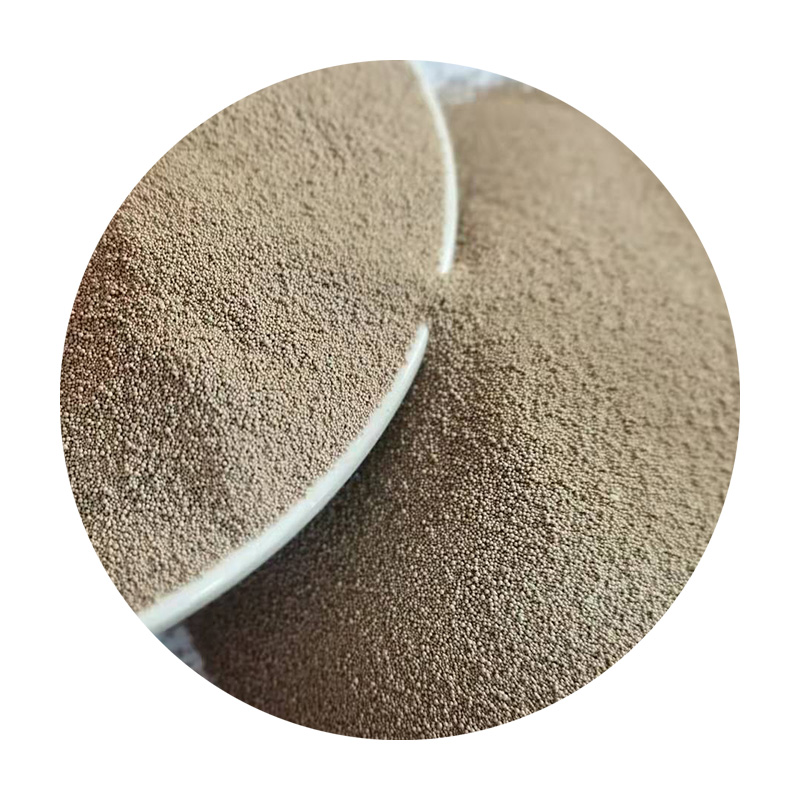
The use of sand in foundries offers several advantages. One of the most notable is its cost-effectiveness; sand is abundant and can be recycled multiple times, significantly reducing material costs. Furthermore, sand molds can be produced quickly, allowing for shorter lead times and increased production rates. Additionally, sand casting can accommodate complex shapes, making it a versatile choice for a wide range of applications, from automotive components to intricate artistic sculptures.
Moreover, the flexibility of sand molds allows for easy modifications. If a design change is necessary, adjustments can be made relatively simply without the need for expensive tooling changes. This aspect makes sand casting particularly appealing for prototype production or batch runs of varying designs.
Challenges and Innovations in Sand Casting
Despite its numerous advantages, sand casting does come with challenges. Issues such as sand erosion and contamination can affect the final casting quality. Innovations in foundry technology have led to the development of coated sands and advanced binders. These materials are designed to enhance mold strength, reduce emissions, and improve the surface finish of the cast products.
Furthermore, the push for sustainability has prompted foundries to explore green sand casting techniques. Utilizing organic binding agents instead of traditional clay and adopting sand recycling processes not only mitigate environmental impact but also improve the overall efficiency of foundry operations.
Conclusion
In conclusion, sand plays a pivotal role in the foundry industry, serving as a crucial material for the metal casting process. Its unique properties, coupled with cost-effectiveness and versatility, make it a favored choice among manufacturers. As the industry evolves, staying ahead of potential challenges through innovation and sustainable practices will be key to harnessing the full potential of sand in foundry applications. As we move toward a more efficient and environmentally conscious future, the significance of sand in foundry processes will undoubtedly continue to grow, highlighting its enduring legacy in metal casting.
Post time:Aug . 22, 2024 04:17
Next:Understanding the Lost Foam Process in Sand Casting Techniques and Applications