The Role of Sand in Ceramic Fire Bricks
Ceramic fire bricks, commonly used in high-temperature applications such as kilns, fireplaces, and industrial furnaces, are crucial components in various sectors including construction, manufacturing, and pottery. One of the primary materials that contribute to the unique properties of these fire bricks is sand. This article explores the significance of sand in the formulation of ceramic fire bricks, focusing on its properties, types, and the overall impact on the performance of these essential refractory materials.
Understanding Ceramic Fire Bricks
Ceramic fire bricks, also known as refractory bricks, are made from specially formulated clay and other materials that can withstand high temperatures without deforming or melting. They are designed to provide insulation while also handling mechanical stresses, making them ideal for use in environments that reach temperatures exceeding 1000 degrees Celsius. The durability, thermal stability, and insulating properties of fire bricks are paramount for their functionality.
The Importance of Sand
Sand is a critical ingredient in the production of ceramic fire bricks. It contributes to the structural integrity, thermal conductivity, and overall performance of the bricks. When used in the formulation process, sand helps to enhance the brick's ability to withstand thermal shock, which is vital for applications where rapid temperature changes occur.
Additionally, the incorporation of sand helps to prevent cracking and distortion during the firing process, allowing the bricks to maintain their shape and strength even under extreme conditions. The silicon dioxide present in sand plays a key role in this respect; it forms a glassy phase during firing, which acts as a binding agent and fills the microvoids within the brick, thus improving its density and mechanical properties.
Types of Sand Used
sand ceramic fire brick
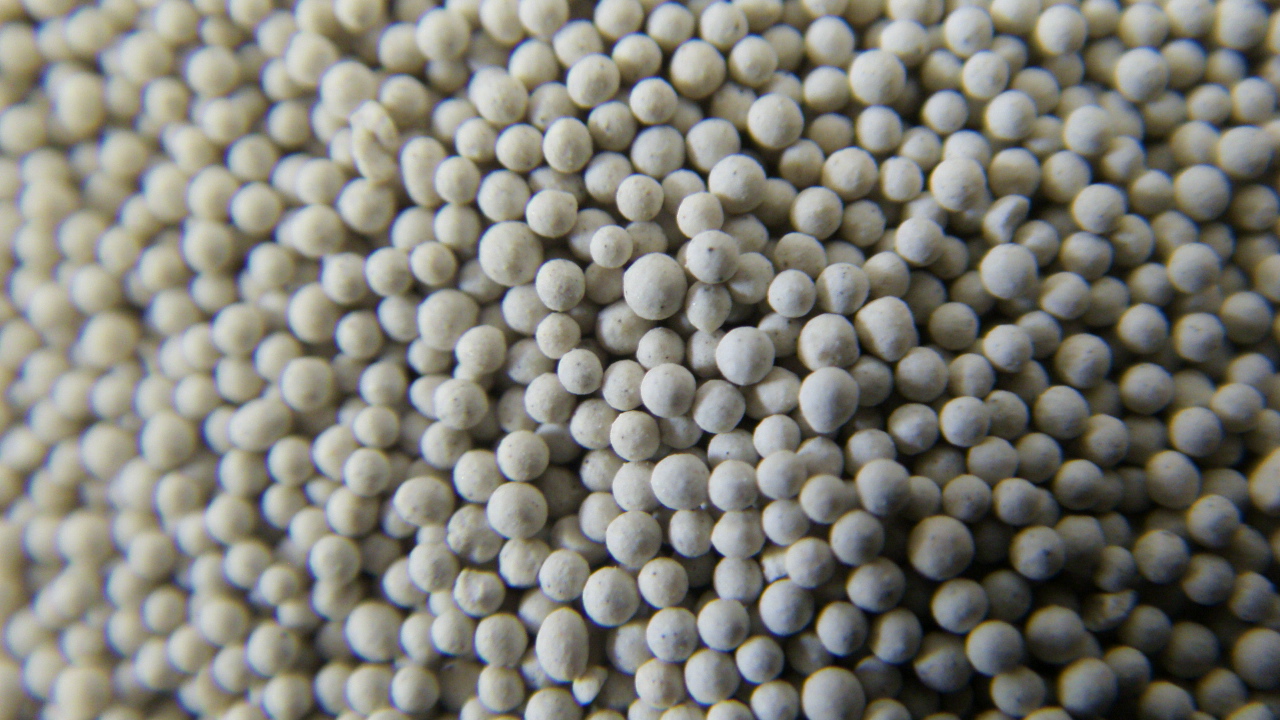
Different types of sand can be utilized in the production of ceramic fire bricks, each affecting the properties of the final product differently. The most commonly used sands include silica sand, which is known for its high purity and excellent thermal properties. It provides strength and stability to the bricks, making them more resistant to thermal cycling.
Another type of sand used is chamotte, which consists of calcined clay and boasts excellent resistance to thermal shock. Its incorporation not only improves the thermal resilience of the bricks but also enhances their ability to absorb and retain heat, which is particularly beneficial for applications like pizza ovens and wood-fired stoves.
Environmental Considerations
The use of sand in the production of ceramic fire bricks also raises environmental considerations. As the demand for construction and industrial refractories grows, so does the pressure on sand resources. Sustainable sourcing and environmentally friendly practices in the extraction and processing of sand are critical issues that need to be addressed to ensure a balance between demand and environmental impact.
Innovations in recycling and repurposing materials, such as using waste products as sand substitutes, are emerging solutions to help mitigate environmental impacts. Additionally, advancements in manufacturing techniques can lead to more efficient use of raw materials, further contributing to sustainability in the industry.
Conclusion
In summary, sand plays a fundamental role in the formulation and performance of ceramic fire bricks. Its contributions to the structural integrity, thermal management, and durability of these materials cannot be understated. As industries continue to innovate in the use and sourcing of sand for ceramic fire bricks, balancing performance with sustainability will be essential in meeting the future demands of high-temperature applications. Understanding and leveraging the properties of sand will ensure that ceramic fire bricks continue to fulfill their crucial role in various sectors for years to come.
Post time:Jul . 26, 2024 23:35
Next:Exploring the Benefits and Techniques of Producing High-Quality Sand Castings for Durable Manufacturing