The Art of High-Quality Sand Casting
Sand casting is one of the oldest and most versatile methods of metal casting, renowned for its simplicity and effectiveness. In recent years, the emphasis on high-quality sand casting has grown significantly, as industries strive for precision, durability, and efficiency in their metal products. This article will explore the essential aspects of high-quality sand casting, including the process, materials, applications, and advantages.
At its core, sand casting involves creating a mold from a sand mixture, which is then filled with molten metal to form the desired shape. The process begins with the design of the mold, where a pattern made from wood, metal, or plastic is placed in a sand mixture, typically composed of silica sand, clay, and water. It is essential to achieve the right balance of these materials to ensure optimal mold strength, permeability, and collapsibility. High-quality sand casting relies on carefully controlling these parameters to produce molds that can withstand high temperatures without deforming.
The Art of High-Quality Sand Casting
The preparation of the mold is crucial in achieving high-quality results. This process involves not just mixing the sand and binder but also ensuring the pattern is properly coated and that the mold halves fit together tightly. Poor mold preparation can lead to misalignments and defects, such as flash or surface imperfections, which compromise the integrity of the final product. Therefore, attention to detail during mold preparation is paramount.
high quality sand casting
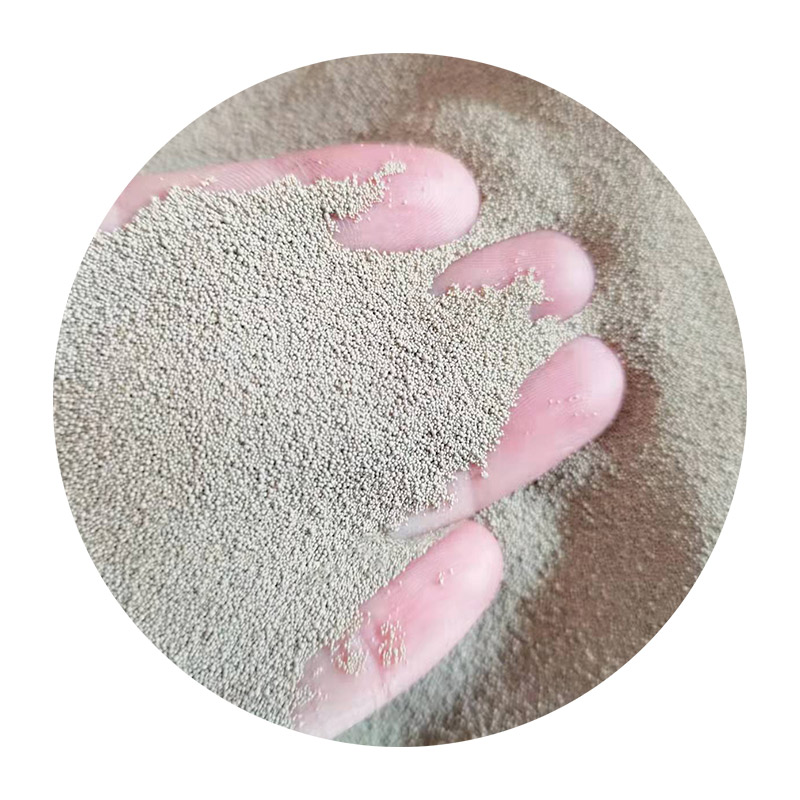
Once the mold is prepared, molten metal is poured into it. Maintaining the correct pouring temperature and speed is essential to avoid issues such as shrinkage cavities and cold shuts — defects commonly seen in lower-quality castings. Furthermore, advanced techniques, such as vacuum pouring or inert gas pouring, can be employed to enhance the quality of the casting, reducing oxidation and contamination during the pouring process.
High-quality sand casting produces parts that exhibit excellent mechanical properties and surface finishes. This method is widely used across various industries, including automotive, aerospace, and machinery. Components ranging from engine blocks and transmission housings to intricate machine parts can be effectively produced using sand casting. Its versatility allows for the casting of complex shapes that would be challenging to fabricate using other methods.
The benefits of high-quality sand casting are manifold. Not only does it provide exceptional dimensional accuracy and surface finish, but it is also cost-effective for both small and large production runs. Moreover, the ability to easily modify molds for different designs without substantial expenses makes sand casting an attractive option for many manufacturers.
In conclusion, high-quality sand casting is a vital component of modern manufacturing. By focusing on material selection, meticulous mold preparation, and precise pouring techniques, manufacturers can create durable and efficient products that meet the increasingly demanding standards of today’s industries. As technology continues to advance, the future of sand casting looks bright, with ongoing innovations aimed at perfecting this traditional yet indispensable manufacturing process.
Post time:Jul . 26, 2024 23:34
Next:Exploring the Future of Sand 3D Printing Technology and Its Numerous Applications in Various Industries