Understanding Sand Casting in Foundry Operations
Sand casting, one of the most widely used metal casting processes, is integral to the foundry industry. This traditional method, which dates back thousands of years, has evolved into a highly sophisticated technique utilized by manufacturers around the globe. At its core, sand casting involves creating a mold from a mixture of sand, a bonding agent, and water. Once the mold is prepared, molten metal is poured into it to create a desired shape.
The Process of Sand Casting
The sand casting process begins with the design of the pattern, which is a replica of the final product. Patterns are typically made from materials like wood, plastic, or metal and must be slightly larger than the finished item to account for shrinkage during the cooling process. Once the pattern is prepared, it is pressed into a mold made of fine or coarse sand mixture to create the shape of the desired part.
The next step involves assembling two halves of the mold, known as the cope (top half) and the drag (bottom half), before the molten metal is poured. The mixture used in molds is crucial; the sand must possess suitable properties, such as shape, size, and cohesion, to ensure that it can withstand the pouring of molten metal without disintegrating.
After the metal has been poured and allowed to cool, the mold is broken apart to reveal the casting. It is then inspected for quality, magnitude, and structural integrity. Any imperfections such as sand inclusions or surface defects are corrected through finishing processes, including grinding, polishing, or sandblasting.
Advantages of Sand Casting
One of the primary advantages of sand casting is its versatility. It can accommodate a wide range of metals, including aluminum, brass, and iron, making it suitable for numerous applications across various industries, from automotive to aerospace. Additionally, the process allows for the production of large and complex shapes that would be challenging to achieve with other casting methods.
sand casting foundry
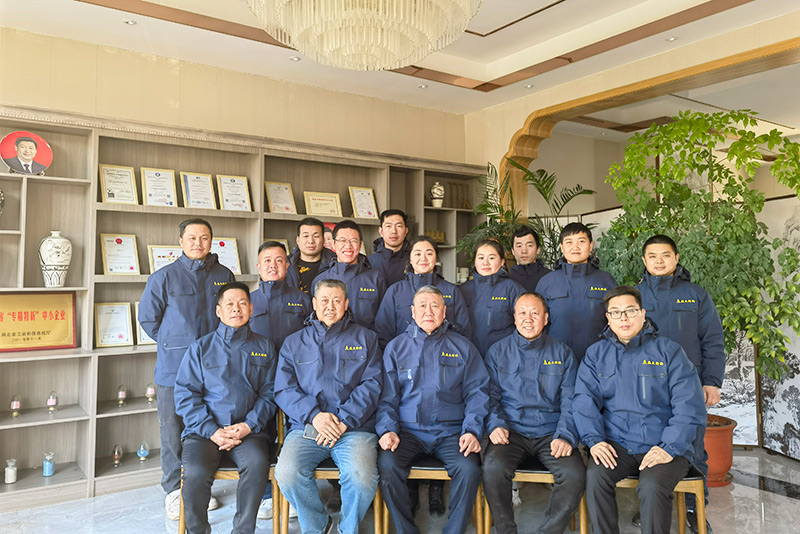
Another significant benefit is cost-effectiveness. Producing molds from sand is generally less expensive than creating permanent molds used in die casting or investment casting. This makes sand casting particularly attractive for low to medium volume production runs and prototyping, where the cost of creating a permanent mold would be prohibitive.
Moreover, sand casting has a relatively short lead time. The ability to quickly create patterns and molds allows manufacturers to meet tight production schedules and rapidly respond to market demands.
Challenges in Sand Casting
Despite its advantages, sand casting is not without its challenges. The quality of the final product highly depends on the expertise of the foundry workers and the materials used. There are instances of defects like porosity, which occurs when gas bubbles are trapped in the solidifying metal, compromising its integrity.
Furthermore, due to the manual nature of the process, sand casting may not always achieve the dimensional accuracy required for precision components. However, advancements in technology, such as computer-aided design (CAD) and numerical simulation, are helping to mitigate these challenges by improving the design and analysis of castings before production.
The Future of Sand Casting
As industries evolve, so does the sand casting process. With growing interest in sustainability and reducing the environmental impact of manufacturing, foundries are exploring new molding materials and methods to enhance efficiencies. Innovations like 3D printing are being integrated into the sand casting process to streamline production and reduce waste.
In conclusion, sand casting remains a fundamental technique within the foundry sector, offering both flexibility and cost-efficiency. As advancements in technology and techniques continue to improve its applications and mitigate its challenges, sand casting is poised to maintain a vital role in manufacturing for years to come.
Post time:Aug . 14, 2024 02:11
Next:Understanding the Properties and Applications of Resin Coated Sand in Modern Industries