What Is Resin Coated Sand?
Resin coated sand is an advanced material widely used in the foundry industry for the production of various metal castings. This specialized type of sand is created by coating sand grains with a thermosetting resin, which provides several advantages over traditional casting sands, making it a popular choice among metal casters and manufacturers.
Composition and Production Process
The primary component of resin coated sand is silica sand, which serves as the base material due to its excellent thermal properties and ability to withstand high temperatures. The production process involves mixing dry silica sand with a resin binder and often a catalyst. This mixture is then heated, causing the resin to coat the sand grains evenly. The result is a sand that has enhanced strength, thermal resistance, and improved dimensional stability.
Typically, the resins used in this process include phenolic, epoxy, and furan resins, each of which offers unique properties that cater to different casting requirements. The choice of resin impacts the final product, influencing its performance in specific applications.
Advantages of Resin Coated Sand
1. High Strength One of the most significant advantages of resin coated sand is its high compressive strength, which allows for the production of intricate shapes and details in metal castings. This strength is particularly beneficial for thin-walled castings, as it reduces the likelihood of defects during the pouring process.
2. Thermal Stability Resin coated sand can withstand higher temperatures compared to conventional sand. Its superior thermal stability helps in maintaining the integrity of the mold during the casting process, leading to better surface finishes and fewer defects.
3. Rapid Setting The curing process of resin coated sand is relatively quick. Once the resin is applied, the sand can be molded and cured within a short time frame, allowing for efficient production schedules.
what is resin coated sand
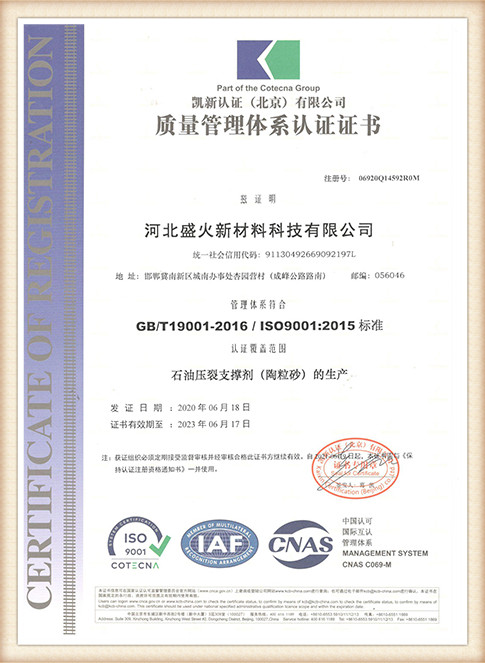
4. Excellent Surface Finish Molds made from resin coated sand provide a smoother finish on castings. This characteristic reduces or eliminates the need for additional machining, saving time and costs in post-production processes.
5. Versatility Resin coated sand can be used for various metals, including aluminum, iron, and steel. Its adaptability makes it suitable for a wide range of applications, from automotive parts to artistic sculptures.
Applications
The applications of resin coated sand are extensive. It is commonly used in the automotive industry for producing engine blocks, transmission cases, and other complex parts that require high precision. Additionally, it finds use in the manufacturing of components for aerospace, marine, and general engineering industries where performance and accuracy are critical.
Challenges and Considerations
Despite its many advantages, resin coated sand is not without its challenges. The cost of resin coated sand is typically higher than that of traditional sands, which can impact overall production budgets. Moreover, handling and disposal of used resin coated sand require adherence to environmental regulations due to the presence of resins and potential chemical hazards.
Conclusion
Resin coated sand represents a significant advancement in the field of metal casting materials. Its remarkable properties, including high strength, thermal stability, rapid setting, and excellent surface finish, make it an invaluable asset in modern manufacturing. As industries continue to seek greater precision and efficiency, the demand for resin coated sand is likely to grow, solidifying its place in the future of metal casting technology. By understanding both the benefits and challenges associated with this material, manufacturers can make informed decisions that optimize production processes and improve product quality.
Post time:Aug . 14, 2024 02:11
Next:Selecting the Right Molding Sand for Optimal Metal Casting Performance and Quality