Understanding Foundry Sand Properties
Foundry sand is a critical component in the casting process, playing a significant role in the production of metal castings. The properties of foundry sand are paramount to achieving high-quality casts, influencing factors such as mold strength, surface finish, and overall casting integrity. This article delves into the essential properties of foundry sand and their implications for the casting industry.
1. Grain Shape and Size
The grain shape and size of foundry sand are fundamental to its performance. Generally, sand grains can be spherical, angular, or rounded. Spherical grains tend to provide better flowability and packing density, leading to improved mold strength and surface finish. On the other hand, angular grains can enhance the interlocking of particles, resulting in a more robust mold. The size of the sand grains, typically falling between 0.1 mm and 0.5 mm, influences the permeability and compactness of the mold. Finer sands can create smoother surfaces but may also lead to increased friction that can hinder metal flow.
2. Permeability
Permeability is another critical property of foundry sand, referring to its ability to allow gases to escape during the casting process. Adequate permeability is essential for preventing defects such as blowholes and gas porosity in the final casting. Foundry sands must strike a balance; while too low permeability can trap gases, too high permeability may reduce mold strength. The optimal permeability level depends on the specifics of the metal being cast and the casting procedure employed.
3. Moisture Content
foundry sand properties
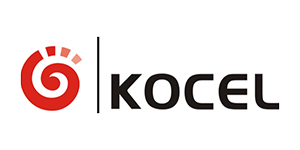
Moisture content significantly affects the behavior of foundry sand. The correct moisture level helps bind the sand grains together, enhancing mold strength. However, excessive moisture can lead to problems such as steam generation, which can cause defects in the casting. Therefore, maintaining the right moisture content is crucial for optimal performance, typically ranging from 2% to 8% for sand molds.
4. Thermal Properties
The thermal properties of foundry sand, including thermal conductivity and thermal expansion, are vital during the casting process. A sand's thermal conductivity determines how quickly it can absorb heat from the molten metal. Sand with high thermal conductivity aids in the rapid cooling of the cast. Conversely, the thermal expansion of sand can lead to dimensional changes during the heating process, potentially causing casting defects. Understanding these thermal properties is essential for selecting the right sand for specific casting applications.
5. Binding Agents
In many cases, foundry sand is used in conjunction with binding agents such as clay or resin. These binding agents enhance the sand's cohesiveness and strength. Clay-type sands, commonly known as green sands, have moisture-retaining properties that provide excellent mold strength, but they may require more careful handling to prevent defects. Resin-bonded sands, while more expensive, offer superior strength and can be used for more intricate casting designs.
Conclusion
The properties of foundry sand significantly impact the quality and efficiency of the casting process. By understanding the characteristics such as grain shape and size, permeability, moisture content, thermal properties, and the inclusion of binding agents, foundry professionals can make informed decisions in selecting the appropriate sand for their specific needs. As the casting industry continues to evolve, ongoing research and development in sand properties and applications will remain essential for achieving improved casting outcomes and meeting the demands of modern manufacturing.
Post time:Aug . 03, 2024 02:59
Next:Creating a Custom 3D Printed Sanding Block for Perfect Surface Finishing