3D Printing a Sanding Block Revolutionizing Your DIY Projects
In recent years, 3D printing has transformed the way we approach DIY projects, offering a level of customization and convenience that traditional manufacturing methods simply cannot match. One fascinating application of this technology is the creation of a sanding block, a tool essential for any woodworking or crafting enthusiast. By leveraging 3D printing, we can design and produce sanding blocks that perfectly fit our needs, improving both efficiency and effectiveness in various projects.
The Importance of Sanding Blocks
Sanding blocks are commonly used in woodworking to ensure a smooth surface on finished pieces. They provide a flat and stable base on which sandpaper can be adhered, allowing for uniform pressure application across the surface being sanded. Traditional sanding blocks are often made from wood or plastic, offering limited shapes and sizes. However, with 3D printing, we can create sanding blocks with unique geometries that cater to specific requirements, including ergonomic designs for better grip, varying shapes for different surfaces, and customizable dimensions.
Designing Your 3D Printed Sanding Block
Creating a sanding block using 3D printing starts with the design phase. Utilizing software like Tinkercad, Fusion 360, or Blender, enthusiasts can sketch out their ideas, taking into account the block’s intended use. For example, if a sanding block is needed for detailed work on intricate contours, designers can create a block that mimics the desired shape. Also, varying the internal structure can optimize material use while maintaining strength and durability.
Additionally, one can incorporate features such as finger grips, a central recess for the sandpaper, or even holes for dust extraction to improve performance. The possibilities are nearly endless, providing makers with a chance to experiment and innovate.
sanding block 3d print
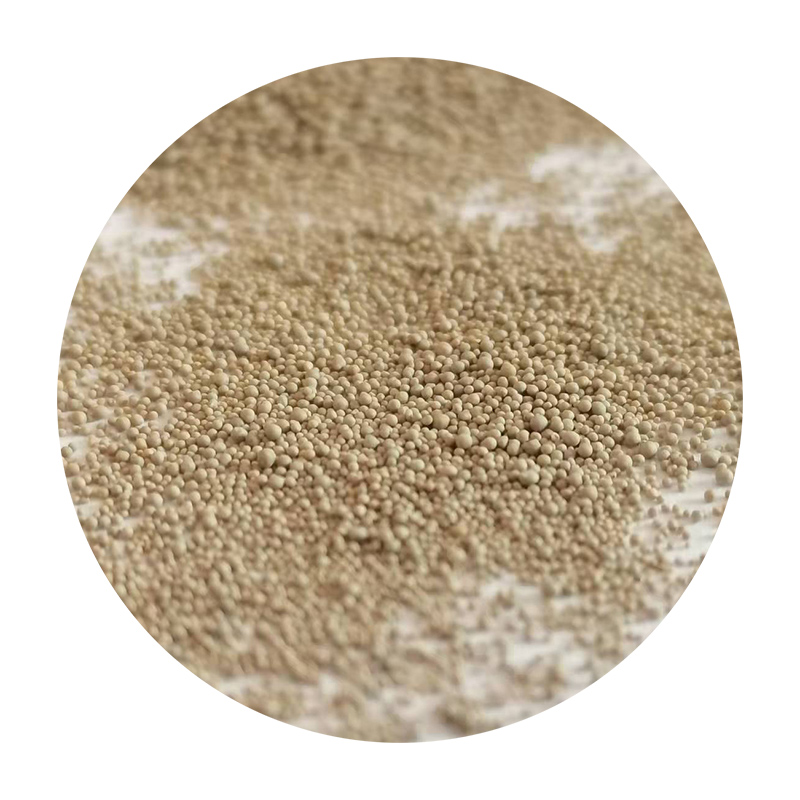
Selecting Materials for 3D Printing
Material choice is critical in 3D printing, especially for functional items like sanding blocks. Common materials include PLA (Polylactic Acid), ABS (Acrylonitrile Butadiene Styrene), and PETG (Polyethylene Terephthalate Glycol). Each material offers distinct characteristics PLA is easy to print and biodegradable, ABS is durable and heat-resistant, while PETG combines ease of printing with strength and flexibility. Selecting a material that can withstand the friction and pressure involved in sanding operations is vital for longevity and effectiveness.
Printing and Post-Processing
Once the design is finalized and the material chosen, it’s time to print the sanding block. Using a 3D printer, the design is translated into a tangible product layer by layer. Depending on the printer’s resolution and settings, the quality and finish of the block may vary. Post-processing steps, such as sanding rough edges or applying a coat of sealant, can enhance the surface finish and durability, ensuring that the sanding block performs well in practice.
Conclusion
3D printing a sanding block exemplifies the vast potential of additive manufacturing in enhancing our DIY projects. By allowing for customization, increased efficiency, and innovative design, 3D printing is reshaping how we approach tool-making. Whether you are a hobbyist looking to improve your craft or a professional woodworker seeking the perfect tool, exploring the world of 3D-printed sanding blocks can open up new possibilities for creativity and customization. Embrace this technology, and take your woodworking skills to the next level with a personalized sanding block that meets all your specifications. The future of DIY is exciting, and it’s just a print away.
Post time:Aug . 03, 2024 02:31
Next:Exploring the Applications and Innovations in Ceramic Foundry Sand Materials and Their Impact on Industry