Understanding Foundry Casting Sand Essential Material for Metal Casting
Foundry casting sand plays a crucial role in the metalcasting industry, serving as the primary molding material for producing complex and precise metal products. The term foundry sand generally refers to a specific type of sand that is used in the manufacturing process of metal castings, particularly iron, steel, and non-ferrous alloys. This article aims to explore the characteristics, types, and advantages of foundry casting sand, as well as its significance in the casting process.
Characteristics of Foundry Casting Sand
The most commonly used type of foundry sand is silica sand, which is comprised mainly of silicon dioxide (SiO2). This material possesses several desirable characteristics that make it ideal for use in foundries
1. High Refractoriness Foundry sand can withstand high temperatures without degrading, making it suitable for metal casting operations that reach melting points well above 1000 degrees Celsius.
2. Good Molding Properties It easily adheres to different shapes, providing good stability for mold forms and allowing for intricate designs and details in cast products.
3. Grain Shape and Size The shape and size of sand grains greatly influence the properties of the casting mold. Round grains allow for better flow and packing, while angular grains provide mechanical strength.
4. Thermal Conductivity Effective heat transfer is essential in the casting process. Foundry sands possess adequate thermal conductivity, ensuring that molten metal solidifies uniformly.
Types of Foundry Casting Sand
While silica sand dominates the foundry market, there are various types of sands used in different applications
1. Green Sand This is a mixture of silica sand, clay, water, and additives. It is named for its moist state and is widely used for ferrous and non-ferrous castings. Green sand molds are economical and have good dimensional stability.
foundry casting sand
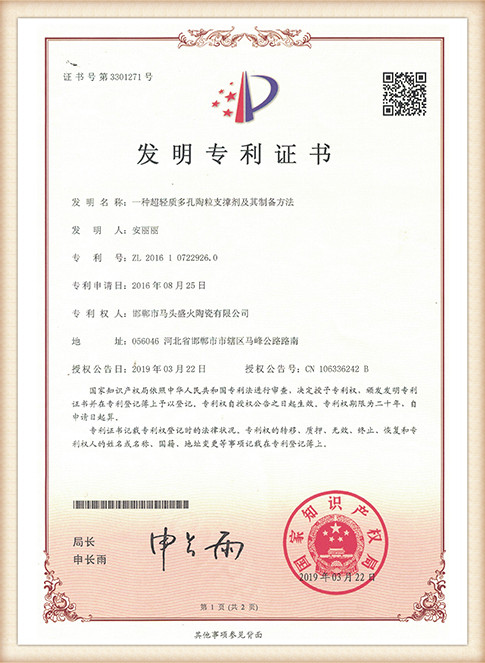
2. Synthetic Sand This type of sand is created from various natural materials, molded to possess specific properties that enhance performance during casting. It often provides better consistency and reduced impurities.
3. Resin-coated Sand This sand is coated with a resin binder that hardens when heated. Resin-coated sands are ideal for high-precision casting, as they provide improved surface finishes and dimensional accuracy.
4. Zircon Sand Known for its high melting point and low expansion, zircon sand is often used for casting molds that require superior surface finish and dimensional stability.
Advantages of Using Foundry Casting Sand
The use of foundry casting sand offers numerous advantages
- Cost-Effectiveness Foundry sand is relatively inexpensive compared to other materials used in metal casting, making it viable for mass production.
- Reusability Used sand can be reclaimed and recycled for new casting operations. This not only reduces waste but also minimizes the consumption of new raw materials.
- Versatility Foundry sand can cater to a wide range of casting processes, including sand casting, shell molding, and lost foam casting, making it an indispensable tool in the foundry sector.
Conclusion
Foundry casting sand is an essential component of the metal casting process, providing the necessary properties to manufacture high-quality cast products. Its various forms, including green sand and synthetic sand, allow for flexibility in production, catering to the specific needs of diverse industries. As technology and methodologies evolve, innovations in foundry sand formulations will continue to enhance the efficiency and quality of metal casting operations, solidifying its place as a pivotal material in manufacturing.
Post time:Jul . 29, 2024 22:31
Next:Exploring the Essential Role of Sand in the Casting Process and Its Impact on Quality