The Role of Sand in Casting A Comprehensive Overview
Casting is a fundamental manufacturing process used to create complex shapes and components in various industries, including automotive, aerospace, and metalworking. Among the various materials employed in this process, sand has emerged as a dominant medium, particularly in sand casting. This method is notable for its versatility, cost-effectiveness, and ability to produce intricate geometries, making it a vital technique in modern foundries.
Sand casting involves the creation of a mold from a mixture of sand, clay, and water. The sand used in this process is typically silica sand, which is known for its durability and thermal stability. The primary purpose of sand in casting is to form the mold cavity where the molten metal will be poured. The mixture's properties can be tailored to ensure optimal performance, as factors such as grain size and shape significantly influence the mold's strength and permeability.
The Role of Sand in Casting A Comprehensive Overview
The preparation of sand for casting involves several steps to ensure the right consistency and characteristics. First, the sand grains must be uniformly sized to achieve a smooth finish. Inadequate screening can lead to defects in the final product, such as rough surfaces and dimensional inaccuracies. Moreover, the addition of clay and water helps to bind the grains together, providing the mold with strength while retaining the necessary porosity to allow gases to escape during the casting process.
sand in cast
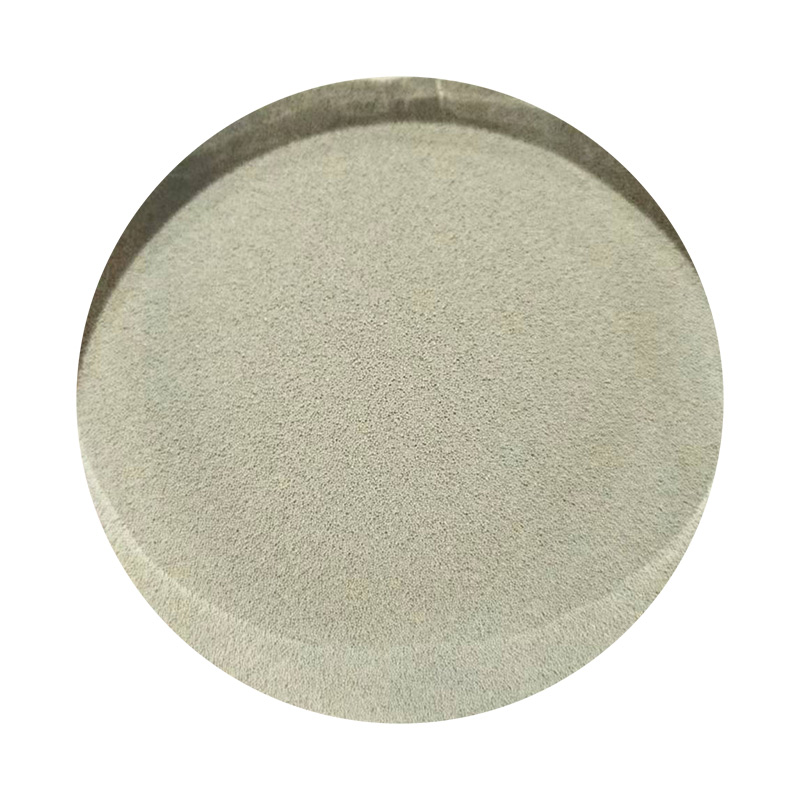
Once the mold is prepared, the molten metal is poured into the cavity. The sand mold absorbs heat from the liquid metal, facilitating solidification. The thermal conductivity of sand is crucial at this stage, as it helps to control the cooling rate of the casting, which can affect the mechanical properties of the final product. For instance, rapid cooling can lead to higher hardness but may also cause brittleness, whereas slower cooling can enhance ductility.
Despite the numerous benefits of sand casting, the process is not without challenges. The presence of moisture in the sand mixture can lead to defects known as sand inclusions or blowholes, which occur when trapped air or steam escapes during solidification. Such defects compromise the integrity of the casting and must be meticulously monitored during production.
Furthermore, surface finish and dimensional accuracy are often less precise than those achieved with other casting methods, such as investment casting or die casting. As a result, secondary machining processes may be necessary to meet stringent specifications required in various industries.
In conclusion, sand plays a crucial role in the casting process, serving as the primary material for mold creation. Its properties, such as durability, heat retention, and adaptability, make it an ideal choice for producing a wide range of components. While there are challenges associated with sand casting, the benefits it offers, particularly its cost-effectiveness and ability to create large, complex parts, continue to make it a prominent method in manufacturing. As technology advances, improvements in sand casting techniques promise to enhance its quality and efficiency, ensuring its relevance in an increasingly competitive industrial landscape.
Post time:Jul . 29, 2024 22:11
Next:Current Trends and Predictions for Gold and Sand Prices in the Global Market Today