An Overview of Sand Casting Manufacturers
Sand casting is one of the oldest and most widely used manufacturing processes for metal workpieces. This technique involves creating a mold from a sand mixture, which is then filled with molten metal to form a desired shape. The simplicity and versatility of sand casting make it an essential process in various industries, from automotive to aerospace. This article provides an overview of sand casting manufacturers, their processes, and the benefits they offer.
The Sand Casting Process
The sand casting process typically begins with the creation of a pattern, which is a replica of the final product made from materials such as wood, metal, or plastic. This pattern is then placed in a molding box and surrounded by a sand mixture, often composed of silica sand, clay, and water. The sand is compacted around the pattern to create a mold cavity. Once the mold is prepared, the pattern is removed, leaving an impression in the sand.
Molten metal is then poured into the mold through a system of gates and runners, filling the cavity. After the metal cools and solidifies, the sand mold is broken away, revealing the cast part. The final step involves finishing processes such as trimming, grinding, or machining to achieve the desired specifications.
Key Characteristics of Sand Casting Manufacturers
1. Expertise and Experience Leading sand casting manufacturers bring extensive knowledge and experience to the table. They understand the intricacies of the casting process, including the properties of different metals and the optimal conditions for pouring and cooling.
2. State-of-the-art Equipment Modern sand casting manufacturers invest in advanced machinery and technology to enhance their production capabilities. Automated systems for mold making and pouring can significantly improve efficiency and precision.
sand casting manufacturers
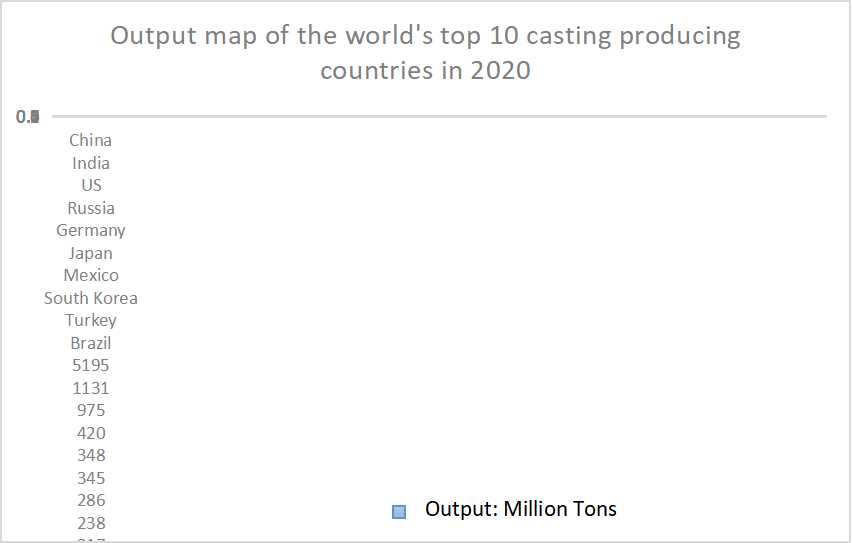
3. Quality Assurance A significant characteristic of reputable sand casting manufacturers is their commitment to quality control. They often implement rigorous testing protocols to ensure that each cast part meets industry standards and customer specifications. This includes non-destructive testing (NDT) methods to detect potential defects in the metal structure.
4. Customization Many manufacturers offer customized solutions tailored to their clients' specific needs. This could involve making unique mold designs, using specific metal alloys, or producing components in various sizes and complexities.
5. Sustainability Practices In recent years, there has been a growing emphasis on sustainable manufacturing practices. Top-tier sand casting manufacturers often employ environmentally friendly methods, such as recycling sand and metal scrap, to minimize their ecological footprint.
Industries Served by Sand Casting Manufacturers
Sand casting manufacturers cater to a wide range of industries, including
- Automotive Producing engine blocks, transmission cases, and various components essential to automobile assembly. - Aerospace Creating lightweight yet strong parts that withstand high-stress conditions, such as turbine blades and structural components. - Construction Manufacturing heavy machinery parts, such as gears and housings utilized in construction equipment. - Marine Supplying components such as propellers and engine blocks for marine vessels. Conclusion
In summary, sand casting manufacturers play a crucial role in the manufacturing ecosystem, providing valuable services across multiple industries. Their expertise, advanced technology, quality assurance practices, and commitment to sustainability ensure that they produce high-quality metal components that meet the demands of modern engineering. As industries continue to evolve, the importance of reliable sand casting manufacturers will undoubtedly remain significant, driving innovation and efficiency in metal production.
Post time:Aug . 13, 2024 05:22
Next:Summary and Insights on the Effectiveness and Applications of Sand Casting Techniques in Manufacturing