The Significance of Sand Cast Foundries in Modern Manufacturing
Sand casting, also known as sand molded casting, is a widely used metal casting process that has foundry roots dating back thousands of years. Despite the advent of advanced technologies in manufacturing, sand cast foundries remain pivotal in various industries, including automotive, aerospace, and art. This article delves into the significance of sand cast foundries, highlighting their process, advantages, and applications in contemporary manufacturing.
The Sand Casting Process
The sand casting process involves several key steps. Initially, a pattern, which is a replica of the final product, is created using materials like metal or plastic. This pattern is then coated with a thin layer of a release agent to facilitate its removal from the mold. The next step involves compacting sand around the pattern to form a mold. The sand used is typically a mixture of silica sand, clay, and water, which allows it to retain its shape when compacted while also being easily removable once the casting has cooled.
After the mold is prepared, molten metal is poured into the cavity created by the pattern. Once the metal solidifies, the mold is broken, and the casting is removed. The final steps involve cleaning, finishing, and inspecting the cast product for quality assurance. This straightforward yet effective process proves to be versatile, allowing for a wide range of shapes and sizes.
Advantages of Sand Cast Foundries
One of the primary advantages of sand casting is its cost-effectiveness, especially for low to medium production volumes. The materials used in sand casting are relatively inexpensive compared to other casting methods, making it an attractive option for businesses looking to minimize costs. Additionally, the sand used is reusable; it can be reclaimed and used for future molds, further reducing material costs and waste.
sand cast foundry
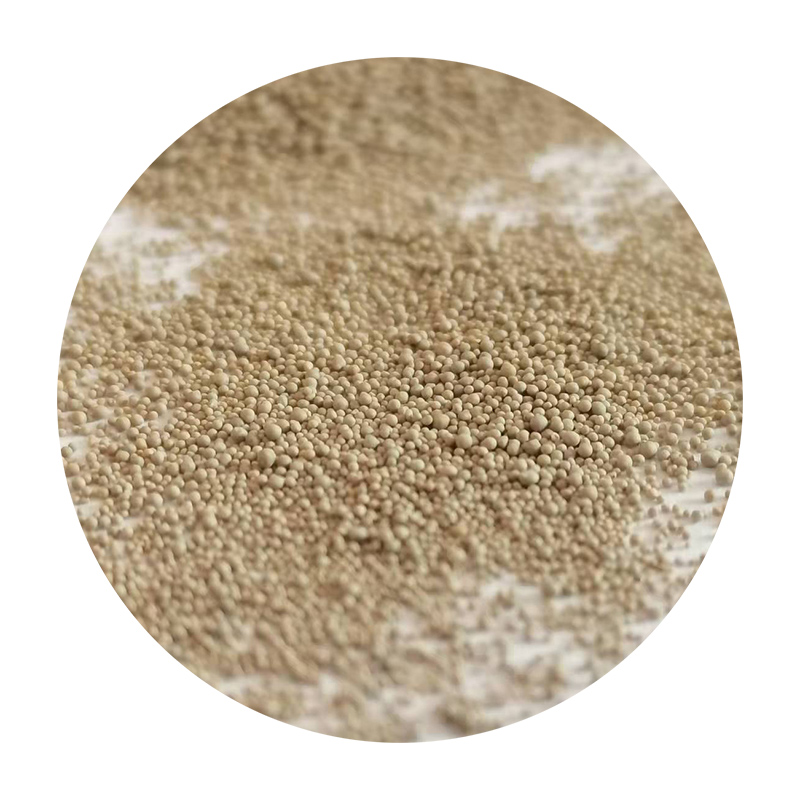
Furthermore, sand casting provides exceptional design flexibility. Complex geometries and intricate details can be achieved, catering to the diverse requirements of different industries. The process also accommodates various metals, including iron, aluminum, brass, and bronze, making it versatile for numerous applications.
Another significant advantage is the ability to produce large castings. Sand cast foundries can manufacture components weighing several tons, which is a feat that other casting techniques may struggle to achieve. Moreover, the rapid setup time associated with sand molds allows for quicker turnarounds compared to other methods, making it feasible for prototyping and small production runs.
Applications in Modern Industries
The applications of sand cast foundries stretch across multiple sectors. In the automotive industry, sand casting is used to produce engine blocks, cylinder heads, and transmission housings. The aerospace sector relies on sand cast components for their lightweight yet durable parts, such as landing gear and structural components. Additionally, sand casting is instrumental in creating artistic sculptures and intricate metalwork, showcasing its versatility beyond industrial applications.
Moreover, as sustainability practices gain traction, many foundries are adopting eco-friendly approaches to sand casting. This includes using recyclable materials and reducing energy consumption during the casting process. By integrating sustainable practices, sand cast foundries not only contribute to environmental conservation but also appeal to the growing market demand for green manufacturing solutions.
Conclusion
In conclusion, sand cast foundries play an essential role in modern manufacturing, providing an efficient and cost-effective method for producing a range of metal components. With their ability to accommodate complex designs, produce large castings, and adapt to various materials, sand casting remains a vital process in different industries. As technology advances, the integration of sustainable practices in sand casting will likely enhance its importance, ensuring that this age-old technique remains relevant in the contemporary manufacturing landscape.
Post time:Aug . 13, 2024 10:38
Next:A Comprehensive Guide to Sanding and Finishing Resin 3D Printed Objects for a Smooth Surface