Rapid Sand Casting Revolutionizing Metal Manufacturing
Rapid sand casting, an innovative approach to traditional metal casting, is gaining attention in the manufacturing sector for its ability to reduce production time and costs while maintaining high-quality output. As industries seek faster and more efficient methods to meet increasing demands, rapid sand casting stands out as a viable solution that combines traditional techniques with modern technology.
The Basics of Sand Casting
Sand casting is one of the oldest and most versatile metal casting processes. It involves the creation of a mold using sand, which is then filled with molten metal to form parts. The primary advantages of sand casting include the ability to produce large and complex shapes, adaptability to different metals, and relatively low production costs. Traditionally, however, the process can be time-consuming due to the manual labor involved in mold creation and preparation.
Innovations Leading to Rapid Sand Casting
Rapid sand casting introduces several advancements that streamline the process. One of the key innovations is the use of 3D printing technology to create molds. This method allows engineers to produce highly precise and complex mold designs in a fraction of the time compared to traditional techniques. By utilizing digital modeling, manufacturers can quickly iterate designs, reducing the lead time for prototyping.
Additionally, computer-aided design (CAD) software plays a crucial role in optimizing the design process. Engineers can simulate casting processes, identify potential defects, and make necessary adjustments before the physical mold is created. This digital approach not only saves time but also enhances the accuracy of the final product.
Benefits of Rapid Sand Casting
rapid sand casting
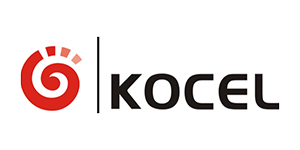
The advantages of rapid sand casting extend beyond speed. The process significantly reduces material waste, as 3D-printed molds can be designed to use only the necessary amount of sand. This efficiency leads to lower production costs and a more sustainable manufacturing process. Furthermore, the precision of 3D printing facilitates the production of components with intricate geometries that would be challenging to achieve with traditional casting methods.
Rapid sand casting also enables manufacturers to respond quickly to market changes and customer demands. In industries such as automotive, aerospace, and consumer electronics, where product life cycles are short, the ability to produce prototypes and small runs rapidly is invaluable. Manufacturers can test designs and gather feedback in real time, allowing for quicker iterations and improvements.
Challenges and Considerations
Despite its many benefits, rapid sand casting is not without challenges. The initial investment in 3D printing technology and advanced software can be significant, posing a barrier for smaller manufacturers. Additionally, while the technology has advanced considerably, there may still be limitations regarding the types of metals that can be effectively used in rapid sand casting processes.
Furthermore, the adoption of rapid sand casting requires a shift in mindset and skill sets within organizations. Employees need training to use new tools and technologies effectively. This transition can take time, but the long-term benefits usually outweigh the initial hurdles.
Conclusion
Rapid sand casting is poised to revolutionize the metal manufacturing industry by bridging the gap between traditional methods and modern technological advancements. As demand for quicker, customized, and high-quality components continues to rise, embracing rapid sand casting will be essential for manufacturers looking to remain competitive in a fast-paced market. With ongoing advancements, this innovative casting technique is set to unlock new possibilities, driving efficiency and creativity in metal production.
Post time:Jul . 31, 2024 21:35
Next:Exploring Various Methods and Techniques for Sand Casting in Modern Manufacturing Processes