Different Types of Sand Casting
Sand casting is one of the oldest and most versatile metal casting processes, offering a unique combination of flexibility, reliability, and cost-effectiveness. The method involves crafting a mold using sand as the primary material, allowing for the reproduction of complex shapes and designs. The technique has evolved over the years, and today, several types of sand casting are commonly employed in various industries. This article will explore the different types of sand casting, discussing their unique characteristics and applications.
1. Green Sand Casting
Green sand casting is perhaps the most commonly used form of sand casting. In this method, a mixture of sand, clay, and water is used to form the mold. The term “green” refers to the fact that the mold is not baked or cured before casting; instead, it is compacted to hold its shape. The main advantage of green sand casting is its cost-effectiveness, as well as its ability to successfully reproduce intricate details. This method is widely used for producing components in the automotive and machinery sectors.
Contrasting with green sand casting, dry sand casting involves using a sand mixture that has been baked or cured before the metal is poured. This process enhances the strength and durability of the mold, reducing the risk of deformation under heat. Dry sand molds are also less prone to moisture-related defects. Dry sand casting is often preferred for high-quality surface finishes and complex product requirements, thereby making it suitable for applications in aerospace and electrical industries.
3. Cold Box Sand Casting
different types of sand casting
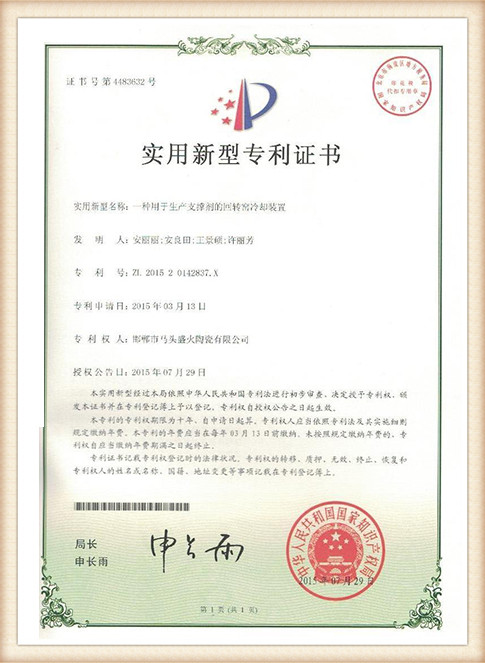
Cold box sand casting utilizes a binder system that hardens the sand when exposed to a gas, allowing for quick mold production without the use of heat. This method is advantageous as it reduces turnaround time and improves production efficiency. Additionally, cold box casting can achieve finer details and better tolerances compared to traditional sand casting methods. Its applications often extend to manufacturing automotive parts and precision components used in various industrial applications.
4. Shell Mold Casting
Shell mold casting is a more advanced variation of sand casting that uses a thin shell of sand and resin to form the mold. The process begins by heating a metal master pattern; then, a mixture of fine sand and thermosetting resin is applied to the pattern to form a shell. After curing, the shell is removed and assembled to create a mold. The primary benefits of shell mold casting include excellent surface finish and dimensional accuracy, making it ideal for producing complex parts where tighter tolerances are required. This method is often used in the production of intricate machine components and small batch production runs.
5. Investment Casting (Lost Foam)
Although primarily known for its compatibility with other materials, investment casting can also utilize a sand-based process known as lost foam casting. In this method, a foam pattern is coated with fine sand and then vaporized during the metal pouring process, leaving a cavity in the shape of the original pattern. This technique provides superior surface finish and intricate detail, making it particularly suitable for aerospace components and intricate designs where traditional sand casting may not suffice.
Conclusion
In conclusion, sand casting continues to be a robust and versatile method in metal manufacturing, adapting to various production needs and technological advancements. Each type of sand casting—be it green sand, dry sand, cold box, shell mold, or lost foam—offers distinct advantages, catering to the diverse requirements of different industries. As manufacturing technologies progress, the use of sand casting is likely to evolve further, ensuring its place as a fundamental process in metal fabrication.
Post time:Jul . 31, 2024 21:06
Next:Exploring the Various Materials Utilized in the Sand Casting Process for Manufacturing Components