Lost Foam Casting Coating An Essential Component in Precision Manufacturing
Lost foam casting is a unique and innovative metal casting process that offers a high level of precision and detail. One of the integral components of this process is the coating applied to the foam pattern, which plays a critical role in ensuring the final quality of the cast components. This article explores the significance of lost foam casting coating, its composition, application methods, and its impact on the overall casting process.
Understanding Lost Foam Casting
Lost foam casting is a process that utilizes foam patterns to create intricate shapes and designs in metal. The pattern is coated with a refractory material, which is crucial for creating a mold cavity that can withstand the molten metal's heat. The term lost foam refers to the fact that the foam pattern is vaporized when the molten metal is poured into the mold, leaving behind a void that takes the shape of the original foam model.
The Role of Coating
The coating in lost foam casting serves several important functions. Firstly, it provides thermal insulation during the pouring process, protecting the foam from premature combustion. This insulation is vital as it allows the molten metal to fill the mold without prematurely igniting the pattern. Secondly, the coating helps to create a smooth surface finish on the final product, reducing the need for extensive machining or finishing processes. Lastly, the coating contributes to dimensional accuracy, ensuring that the resulting cast metal piece closely resembles the original foam pattern.
Composition of the Coating
lost foam casting coating
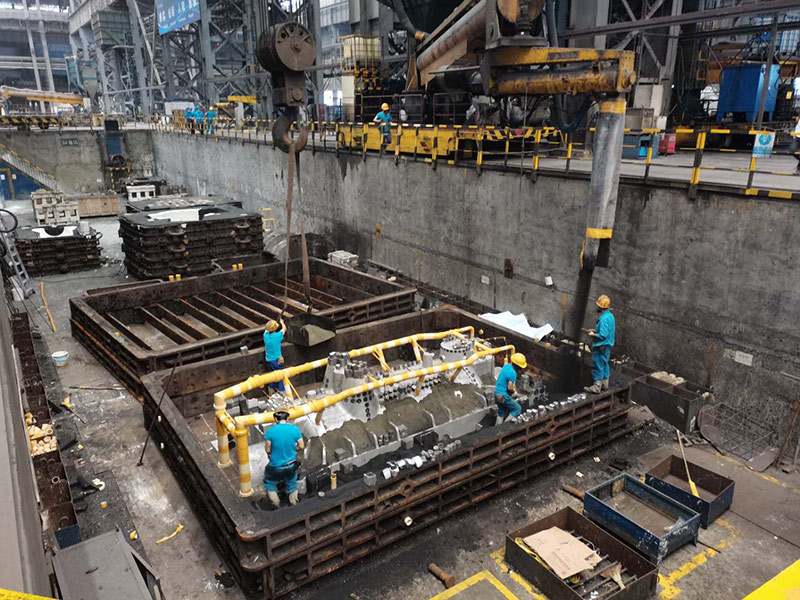
Typically, the coating materials used in lost foam casting are composed of a mixture of fine sand and a binding agent, often ceramic or other refractory materials. This combination allows the coating to withstand high temperatures while providing the necessary structural integrity to maintain mold shape during the metal pouring process. The choice of coating material can influence the final mechanical properties of the cast product, making it essential to select the appropriate formulation based on the specific requirements of the casting.
Application Methods
Applying the coating to the foam pattern can be achieved through various methods, including dipping, brushing, or spraying. Dipping is often favored for its ability to evenly coat complex geometries, while spraying allows for a more controlled application and can reduce the risk of coating oversaturation. After application, the coated patterns are typically subjected to a curing process that solidifies the coating, enhancing its durability and ensuring it adheres firmly to the foam.
Impact on Casting Quality
The quality of the coating directly affects the overall success of the lost foam casting process. A uniform and adequately cured coating can significantly mitigate defects such as sand inclusion, surface roughness, and dimensional inaccuracies. Furthermore, optimizing the coating parameters can lead to improved mechanical properties in the finished cast components, making them suitable for various applications in industries ranging from automotive to aerospace.
Conclusion
In conclusion, the coating used in lost foam casting is more than just a protective layer; it is a fundamental aspect of the casting process that influences the quality and performance of the final product. As industries continue to demand higher precision and efficiency, advancements in coating technologies and formulations will play a crucial role in the evolution of lost foam casting. Understanding the significance of this component enables manufacturers to optimize their processes and produce high-quality castings that meet the sophisticated needs of the market.
Post time:Aug . 12, 2024 22:26
Next:Exploring Methods for Testing Foundry Sand Quality and Performance in Metal Casting Applications