Understanding Foundry Sand Testing Ensuring Quality in Casting
Foundry sand plays a crucial role in the metal casting industry, serving as the medium in which molten metal is poured to create various components. To ensure the quality of the final products, it is essential to conduct thorough testing of the foundry sand. This article delves into the significance of foundry sand testing, the different parameters involved, and the common methods utilized.
The Importance of Foundry Sand Testing
The primary function of foundry sand is to provide a reliable mold that can withstand the high temperatures of molten metal without breaking down. The properties of the sand, such as grain size, permeability, and cohesiveness, directly influence the quality of the casting. Poor sand quality can lead to defects such as surface imperfections, poor dimensional accuracy, and even structural weaknesses in the final product. Therefore, rigorous testing is necessary to maintain industry standards and ensure that the castings produced are reliable and meet the required specifications.
Key Properties of Foundry Sand
1. Grain Size Distribution The distribution of grain sizes in foundry sand affects its flowability and packing characteristics. A well-graded sand promotes better mold strength and reduces the likelihood of defects. Testing the grain size is typically done using sieving techniques or laser diffraction methods.
2. Permeability This property refers to the ability of the sand mold to allow gases to escape during the casting process. Insufficient permeability can trap gases, leading to casting defects. It is measured using a permeability tester, which evaluates the flow of air through a sand sample.
3. Cohesiveness and Bonding The cohesiveness of the sand mixture, often influenced by the type and amount of binder used, is critical for mold strength. Cohesion testing can be conducted using standardized techniques like the green compression strength test, which evaluates the sand’s ability to hold its shape under pressure.
4. Moisture Content The moisture content of foundry sand must be carefully controlled, as it affects both the physical properties of the sand and the quality of the mold. Excessive moisture can lead to defects like gas formation during casting. A simple oven-drying method can be employed to measure moisture content.
foundry sand testing
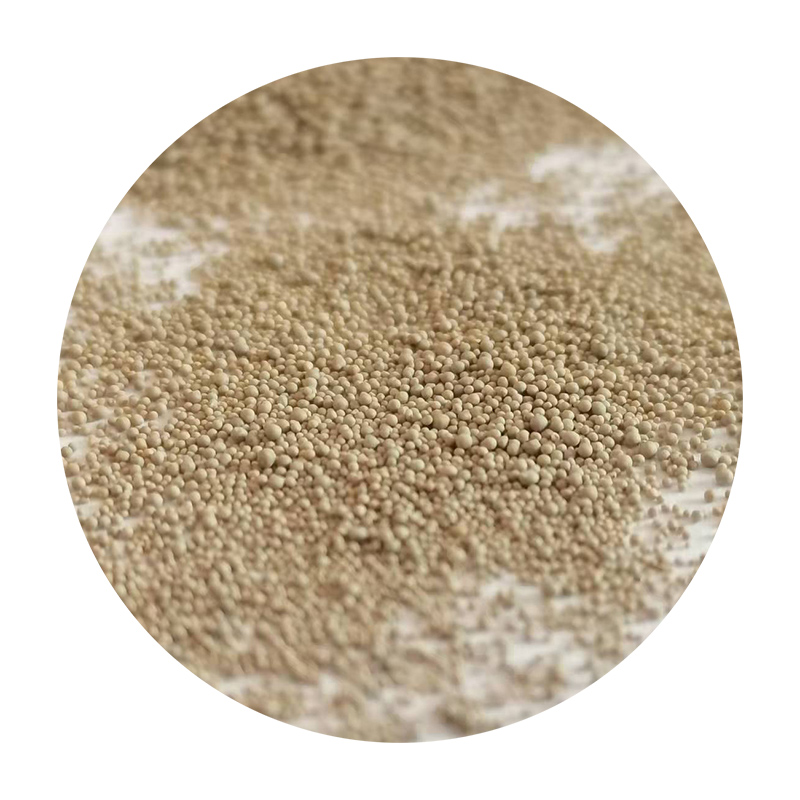
5. Clay Content Clay acts as a binder in sand mixtures, providing cohesion and plasticity. However, too much clay can create issues like increased stickiness and reduced permeability. Clay content can be analyzed using sedimentation techniques or chemical analysis.
Common Testing Methods
Foundry sand testing involves a combination of standard laboratory methods and on-site evaluations to ensure consistency. Some commonly used testing methods include
- AFS (American Foundry Society) Sand Testing Methods AFS has established a series of standardized tests for various sand properties, including grain fineness, clay content, and more. - Ring Test This method assesses the ability of sand to hold together under pressure, reflecting its strength as a mold material.
- Compression Testing This is used to evaluate the strength of the molded sand under various conditions, providing insights into its suitability for the casting process.
- Thermal Analysis This testing involves assessing how sand behaves under different temperature conditions, important for determining its suitability for high-temperature applications.
Conclusion
Regular testing of foundry sand is an indispensable part of the metal casting process, ensuring that molds perform reliably and produce high-quality castings. By meticulously evaluating the various properties of sand, foundries can minimize defects and enhance the overall efficiency of their operations. As the demand for precision in the manufacturing sector continues to rise, investing in rigorous foundry sand testing will remain a key factor in achieving superior casting outcomes.
Post time:Aug . 12, 2024 22:26
Next:Innovative Techniques in Three-Dimensional Sand Printing for Enhanced Manufacturing Applications