Custom Sand Casting An Overview
Custom sand casting is a widely used manufacturing process that involves creating metal parts and components by pouring molten metal into a sand mold. This technique is valued for its versatility, cost-effectiveness, and ability to produce complex shapes. In this article, we will explore the process of custom sand casting, its advantages, applications, and the factors influencing its success.
The Sand Casting Process
The custom sand casting process begins with the creation of a pattern, which is a replica of the final product. Typically made from materials like wood, metal, or plastic, the pattern is essential for forming the mold. The pattern is placed in a specially prepared sand mixture, usually composed of silica sand, clay, and water, which allows it to retain its shape. Once the pattern is set, the sand is compacted around it to form a mold cavity.
After the sand mold is prepared, the next step is to remove the pattern, leaving a hollow cavity that mirrors the shape of the desired casting. The two halves of the mold are then joined together, and molten metal is poured into the cavity through strategically placed gates. Once the metal cools and solidifies, the mold is broken apart to retrieve the finished casting.
Advantages of Custom Sand Casting
One of the primary advantages of custom sand casting is its flexibility in producing different shapes and sizes
. Unlike other casting methods that may require expensive molds, sand molds can be relatively inexpensive and are easily amended for different designs. This makes custom sand casting an excellent choice for small to medium production runs or unique one-off items.Moreover, sand casting can accommodate various alloys and metals, including iron, aluminum, and bronze. This versatility ensures that manufacturers can choose the most suitable materials for their specific applications. The method also allows for the incorporation of complex geometries, which is often challenging with other forms of casting.
custom sand casting
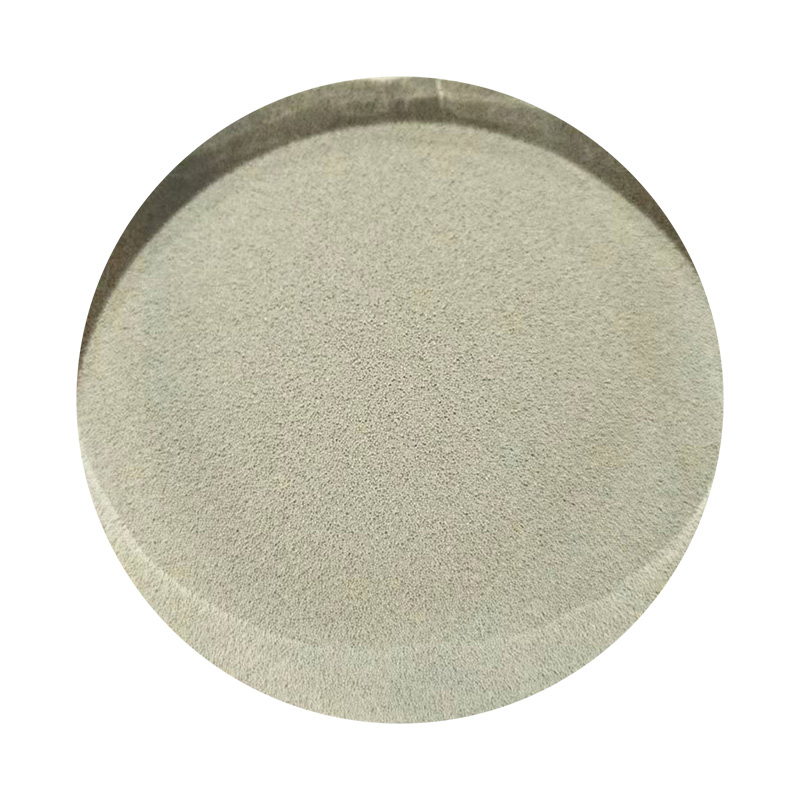
Another significant benefit is the ability to produce large parts. Custom sand casting is particularly effective for creating heavy and oversized components that would be difficult to fabricate using traditional machining techniques. This characteristic is valuable in industries such as automotive, aerospace, and heavy machinery.
Applications of Custom Sand Casting
Custom sand casting finds its application across a wide range of industries. In the automotive sector, it is used for making engine blocks, transmission cases, and other components that require strength and precision. The aerospace industry also benefits from custom sand casting for producing parts that need to withstand extreme conditions.
In addition, the construction and infrastructural sectors utilize sand casting for creating components like valves, pumps, and large decorative fixtures. The method’s adaptability makes it suitable for both functional and aesthetic applications.
Key Considerations for Successful Sand Casting
While custom sand casting offers numerous benefits, there are essential factors to consider to ensure a successful outcome. Material selection is critical; the chosen metal or alloy must be compatible with the sand mold material. Additionally, the design of the pattern and mold should account for factors such as thermal expansion and the proper flow of molten metal to avoid defects.
The sand mixture's quality and composition also play a crucial role in determining the final product's surface finish and structural integrity. Proper compaction and sand conditioning techniques must be employed to enhance the mold’s performance.
In conclusion, custom sand casting is a significant manufacturing technique that provides flexibility and efficiency for producing a wide range of metal components. Its ability to produce complex shapes, use various materials, and create large parts makes it invaluable in multiple industries. By focusing on key considerations and utilizing advanced techniques, manufacturers can optimize the sand casting process to meet their specific needs effectively.
Post time:Jul . 29, 2024 18:11
Next:Exploring the Techniques and Benefits of Sand Casting for Steel Manufacturing Processes