Understanding Sand Casting for Steel A Comprehensive Overview
Sand casting, also known as sand mold casting, is one of the oldest and most versatile methods for producing metal parts, especially steel components. This process involves creating a mold from a mixture of sand and a bonding agent, and it is particularly well-suited for large-scale manufacturing due to its cost-effectiveness and adaptability.
The Sand Casting Process
The sand casting process starts with creating a pattern of the desired component, typically made of metal, plastic, or wood. This pattern is used to form a mold. The mold consists of two halves, known as the cope and drag, which are assembled together. The sand, often mixed with clay and water, is packed tightly around the pattern. The clay acts as a binder that holds the sand grains together.
Once the sand is compacted, the pattern is removed to leave a cavity in the shape of the final product. This cavity is then prepared for pouring molten steel. In many cases, additional features such as risers and gates are incorporated into the mold to allow the molten metal to flow freely and to provide extra material as it solidifies.
When the mold is ready, molten steel is poured into the cavity. The temperature of the molten steel is crucial; it must be high enough to ensure complete filling of the mold but not so high that it adversely affects the quality of the casting. Once the metal cools and solidifies, the mold is broken away to reveal the final casting.
Advantages of Sand Casting
One of the primary advantages of sand casting is its cost-effectiveness. The materials required for sand molds are relatively inexpensive, making it an ideal choice for both small and large production runs. The process is also quite flexible; it can accommodate various part sizes and complexities, from small components to large industrial parts.
Another benefit is the ability to use different types of sand and bonding agents, which allows for the production of high-quality castings with varying mechanical properties. Additionally, sand casting can be used to produce intricate designs and features, enabling manufacturers to meet specific requirements with high precision.
sand casting steel
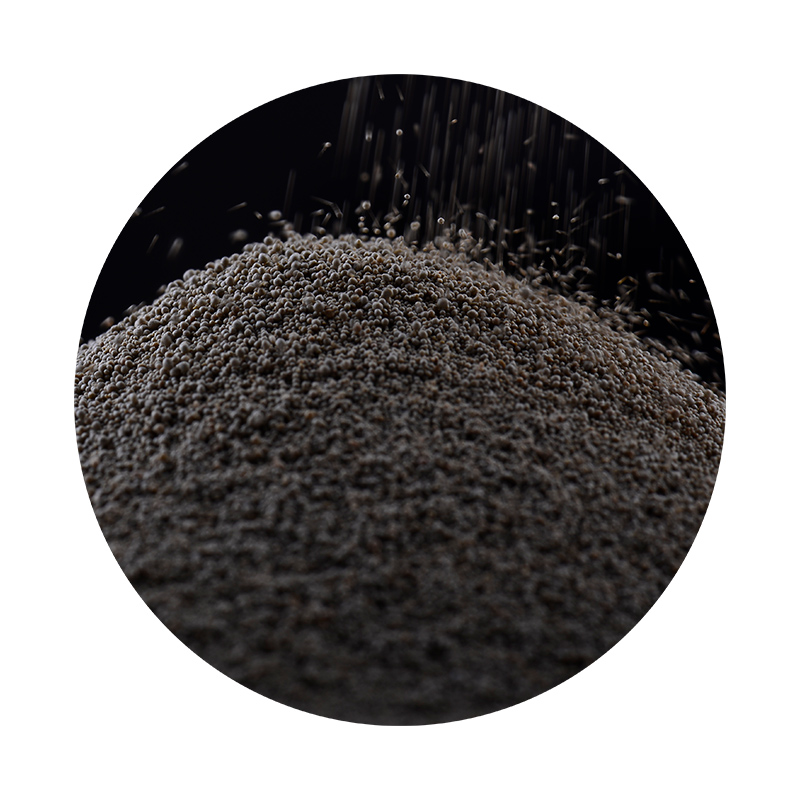
Applications of Sand Casting in Steel
Sand casting is widely used in various industries that rely on steel components. The automotive sector, for instance, utilizes sand casting for engine blocks, cylinder heads, and various other components due to the durability and strength of steel. The aerospace industry also applies sand casting techniques for producing lightweight but strong structural components.
Moreover, the construction industry benefits from sand casting by utilizing it for manufacturing parts such as frames and brackets that require high strength and resilience. Even artistic applications, like sculptures and decorative items, often employ sand casting techniques due to their flexibility in design.
Challenges and Solutions
Despite its many advantages, sand casting has some challenges. One common issue is the surface finish of the cast parts, which may require additional machining to meet specifications. Additionally, the process can lead to defects like shrinkage, gas traps, and sand inclusion if not properly managed.
To mitigate these issues, advancements in technology, such as the use of computer-aided design (CAD) and computer-aided manufacturing (CAM), have significantly improved mold designs and the pouring process. Innovations like 3D printing for creating molds have also emerged, reducing lead times and allowing for more complex geometries.
Conclusion
In summary, sand casting for steel is a practical and efficient manufacturing process that supports a wide range of industries. Its adaptability, cost-effectiveness, and ability to handle complex designs make it a go-to method for producing high-quality steel components. Addressing the challenges associated with the process through modern technology can enhance its effectiveness and further solidify its place in the manufacturing landscape. As industries continue to evolve, sand casting remains a vital technique, embodying both tradition and innovation in metalworking.
Post time:Jul . 29, 2024 17:16
Next:Comprehensive Sand Casting Solutions for Your Custom Metal Fabrication Needs and Projects