The Importance of Ceramic Foundry Sand in Metal Casting
In the metal casting industry, quality and efficiency are paramount. One of the key materials that significantly influence the outcome of metal casting processes is foundry sand. Among the various types of foundry sand available, ceramic foundry sand has gained immense popularity due to its distinct properties and advantages.
Ceramic foundry sand, composed predominantly of alumina and silica, offers superior thermal stability and resistance to deformation, which makes it an ideal choice for high-performance castings. Unlike traditional silica sands, ceramic foundry sands are engineered to withstand higher temperatures, reduce thermal expansion during the casting process, and provide consistent results, thus enhancing the overall quality of the final metal products.
Advantages of Ceramic Foundry Sand
1. High Thermal Conductivity The ability of ceramic foundry sand to conduct heat efficiently is a critical factor in achieving optimal mold performance. This property allows for uniform heat distribution during the melting and solidification processes, which is essential for minimizing defects such as shrinkage or warping.
2. Enhanced Mold Strength Ceramic sands provide excellent mold strength, which is vital for maintaining the integrity of the mold under high pressure and temperature. Strong molds can prevent sand erosion and ensure that intricate designs and fine details of the cast are accurately reproduced.
3. Reduced Environmental Impact The use of ceramic foundry sand is also associated with a lower environmental footprint compared to traditional sands. Ceramic sands can be recycled and reused multiple times without significant degradation in quality. This not only reduces waste but also lowers the cost associated with purchasing new sand for each casting job.
ceramic foundry sand
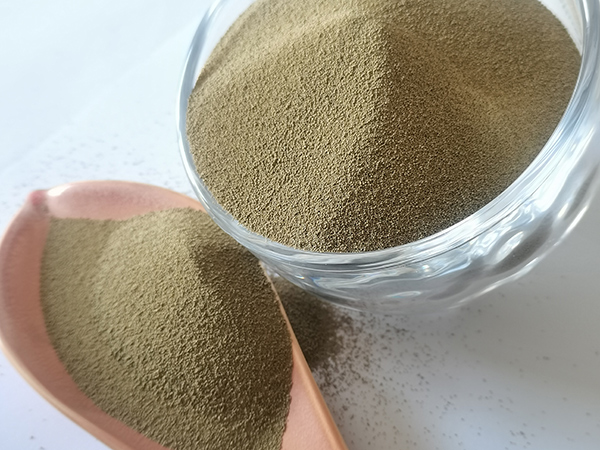
4. Minimized Metal Inclusion One of the most significant advantages of ceramic foundry sand is its ability to minimize or eliminate metal inclusions in cast parts. The smooth and spherical nature of ceramic particles allows for better flow and reduces the likelihood of sand being trapped within the molten metal, resulting in cleaner and more precise castings.
Applications in Various Industries
Ceramic foundry sand is utilized across various sectors, including automotive, aerospace, and machinery manufacturing. In the automotive industry, it is particularly favored for producing high-quality engine components and transmission housings, where precision and durability are crucial. Similarly, the aerospace sector takes advantage of its high performance for creating critical parts that must endure extreme conditions.
The versatility of ceramic foundry sand also extends to the production of industrial equipment and tooling. Components that require specific tolerances and surface finishes can greatly benefit from the enhanced properties of ceramic sand, thereby improving the overall performance and longevity of the products.
Conclusion
As industries continue to seek more efficient and sustainable solutions, ceramic foundry sand stands out as a valuable material in metal casting applications. Its exceptional thermal stability, enhanced mold strength, reduced environmental impact, and ability to produce high-quality castings make it a preferred choice among manufacturers. As technology advances and the demand for quality castings increases, ceramic foundry sand is expected to play an even more significant role in shaping the future of the casting industry. Embracing the potential of ceramic foundry sand not only enhances product quality but also contributes to a more sustainable manufacturing process, setting a benchmark for the industry.
Post time:Aug . 03, 2024 02:23
Next:Innovative Sand Casting Factory Techniques for High-Quality Metal Component Production and Design Solutions