The Importance of Foundry Sand in Metal Casting
Foundry sand is a crucial component in the metal casting industry, primarily used for producing metal parts by pouring molten metal into molds. This specialized type of sand serves as the mold material in various casting processes, including sand casting, which is one of the oldest and most widely used methods in metallurgy. Understanding its properties, applications, and significance can provide valuable insights into its role in modern manufacturing.
Properties of Foundry Sand
The most common type of foundry sand is silica sand, which consists predominantly of silicon dioxide. It possesses a unique set of properties that make it ideal for casting applications. For instance, foundry sand has a high refractoriness, ensuring it can withstand the extreme temperatures generated during the metal casting process without breaking down. Additionally, it has excellent permeability, allowing gases to escape during metal pouring and preventing defects in the final product.
Another critical character of foundry sand is its ability to retain moisture, which aids in the sand's bonding with water and bonding agents used in mold creation. This characteristic is essential for achieving the strong mold structures required for high-quality casts. Moreover, the granularity of foundry sand can be adjusted to suit specific applications, thus providing flexibility in the casting process.
Applications in Metal Casting
Foundry sand is integral in various casting techniques, with sand casting being the most prevalent. This process involves creating a mold from the sand, which is then filled with molten metal. The ability to produce intricate shapes and sizes makes sand casting an attractive option for manufacturers across diverse industries, including automotive, aerospace, and construction.
foundry sand
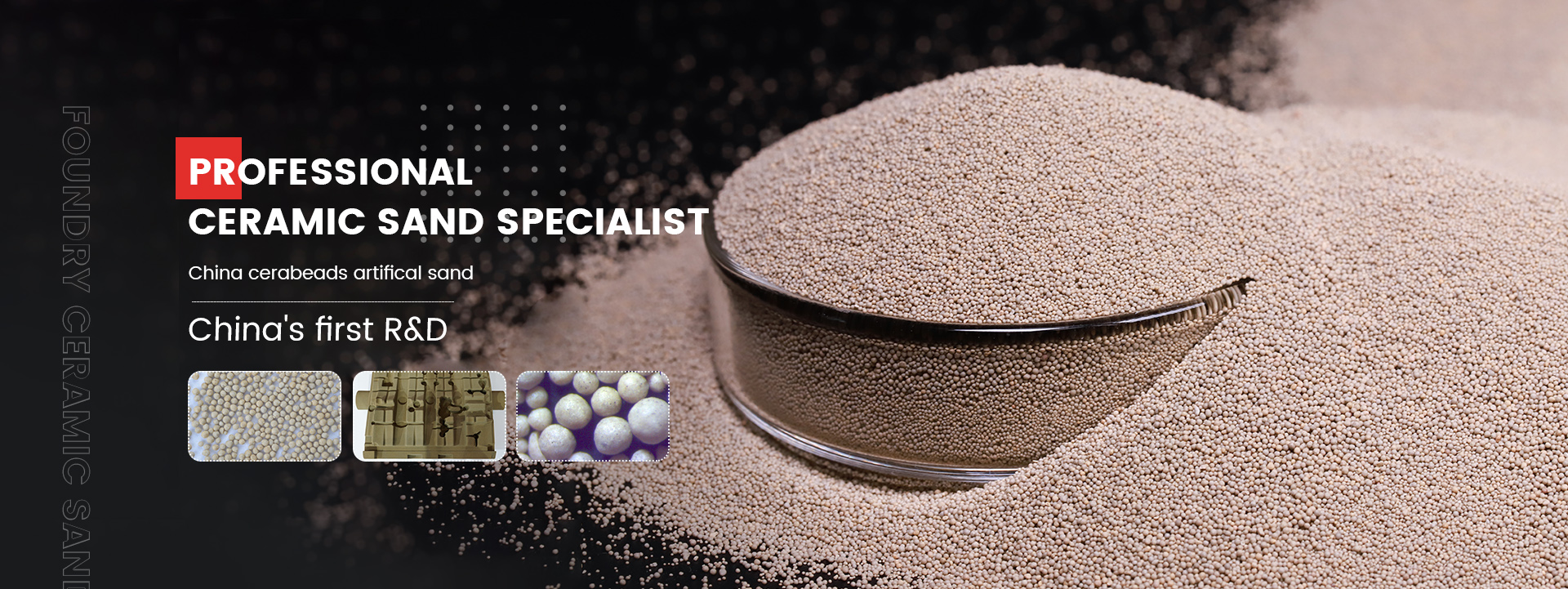
In addition to traditional sand casting, foundry sand is also used in more advanced casting techniques, such as investment casting and lost foam casting, where high precision is required
. Moreover, the demand for foundry sand has increased due to the growing need for lightweight and durable components in various applications, driving innovation in the casting industry.Environmental Considerations
Despite the advantages of using foundry sand, there are environmental concerns associated with its extraction and disposal. Sand mining can lead to habitat destruction and environmental degradation, prompting the need for sustainable practices. Fortunately, many foundries are adopting methods to recycle foundry sand. After a casting process, the sand can often be cleaned and reused, significantly reducing waste and conserving natural resources.
Recyclable foundry sand can be repurposed in various construction applications, such as road construction, concrete production, and land reclamation. This not only minimizes environmental impact but also provides cost savings for foundries by reducing the demand for new sand.
Conclusion
In summary, foundry sand is a vital material in the metal casting industry, contributing to the production of high-quality metal components. Its unique properties, versatility in various casting processes, and the ability to be recycled make it indispensable in modern manufacturing practices. However, it is essential to balance economic benefits with environmental considerations to ensure a sustainable approach to foundry sand usage. As the industry continues to evolve, innovations in both material science and recycling techniques will likely enhance the efficiency and environmental friendliness of metal casting processes.
Post time:Jul . 25, 2024 14:17
Next:Exploring Different Types of Foundry Sand and Their Applications in Metalcasting Processes