An Overview of Foundry Sand Types
Foundry sand plays a critical role in the metal casting industry. It serves as a mold material for producing metal parts, providing not only the desired shape but also the surface finish. There are various types of foundry sand, each with unique properties that make them suitable for specific applications. Understanding these different types can help manufacturers choose the right material for their casting needs.
1. Silica Sand
Silica sand, often referred to simply as foundry sand, is the most commonly used material in the foundry industry. Composed mainly of silicon dioxide (SiO2), it is abundant, relatively inexpensive, and highly heat-resistant. Silica sand provides excellent mold strength and permeability, which allows gases to escape during the casting process. This is crucial to avoid defects such as blowholes. However, it is important to control the dust generated during cutting or grinding, as it can pose health risks.
2. Green Sand
Green sand is a mixture of silica sand, clay, water, and additives. It is termed green because it is used in its natural, moist state, which keeps the sand particles bound together. The clay acts as a binder, providing the strength and ability to hold the shape of the mold. Green sand molds are commonly used for ferrous and non-ferrous castings due to their excellent cooling and solidification characteristics. This type of sand is favored for its reusability and cost-effectiveness.
foundry sand types
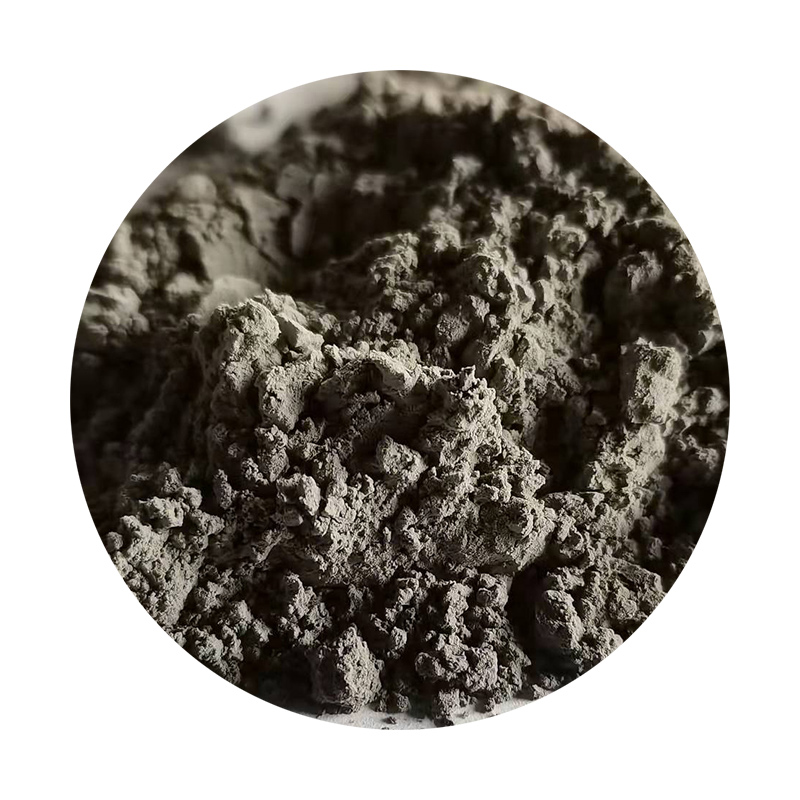
Resin-bonded sand is made by coating sand grains with a resin binder, which hardens when heated. This type of foundry sand offers superior strength and dimensional accuracy compared to traditional green sand. The molds created with resin-bonded sand can sustain higher temperatures, making them ideal for casting materials like aluminum and bronze. However, they can be more expensive and require careful handling and disposal due to the chemical components involved.
4. Lost Foam Sand
Lost foam sand is used in a unique casting process where a foam pattern is coated with sand and resin, then subjected to heat. The foam pattern vaporizes when the molten metal is poured, creating a cavity for the casting. This method allows for complex shapes and reduces the need for additional machining. The sand used in lost foam casting is typically lightweight and fine, optimizing the detail and surface finish of the final product.
5. Shell Molding Sand
Shell molding sand involves creating a thin shell around a pattern made of metal, which is then filled with sand and binder. This process enhances the mold's strength and allows for finer details in the castings. Shell molds are suited for high-volume production of intricate parts due to their excellent dimensional accuracy and surface finish. However, the cost of shell molding is generally higher than that of traditional sand molding processes.
Conclusion
Each type of foundry sand has its advantages and specific applications in different metal casting processes. Silica sand remains the industry standard, but alternative materials like green sand, resin-bonded sand, lost foam sand, and shell molding sand provide tailored solutions for various casting requirements. Ultimately, selecting the right foundry sand is crucial for achieving high-quality castings while balancing costs and manufacturing efficiency. As the metal casting industry evolves, ongoing research and development into sand materials continue to expand the possibilities for superior casting performance.
Post time:Jul . 25, 2024 14:17
Next:Techniques and Tips for Effective Sanding of Ceramic Surfaces for a Flawless Finish