The Sand Casting Foundry Process An Overview
Sand casting is a widely used manufacturing process that involves creating metal components by pouring molten metal into a mold made from sand. It is one of the oldest and most versatile casting methods, capable of producing complex shapes with relative ease. This article will delve into the sand casting foundry process, outlining its steps, advantages, and applications.
The Steps of the Sand Casting Process
The sand casting process can be broken down into several key stages
1. Mold Creation The first step in sand casting is the creation of a mold. This involves compacting a mixture of sand, clay, and water around a pattern that replicates the desired shape of the final product. The pattern is typically made from metal, plastic, or wood and is designed to be slightly larger than the final component to allow for shrinkage during cooling. Once the mold is formed, it is carefully removed from the pattern.
2. Core Making If the part being cast has internal features or hollow sections, cores may be used. Cores are made from a similar sand mixture and are placed in the mold before the molten metal is poured. This allows for the creation of intricate internal shapes that would otherwise be impossible to produce.
3. Melting the Metal The next step is to melt the metal that will be poured into the mold. This is typically done in a furnace, where the metal is heated to its molten state. Common metals used in sand casting include aluminum, iron, and steel.
4. Pouring Once the metal has reached the appropriate temperature, it is poured into the prepared mold. Care must be taken during this stage to ensure that the molten metal fills the mold evenly and does not create defects.
5. Cooling and Solidification After pouring, the metal is allowed to cool and solidify. The cooling time will vary depending on the size and thickness of the cast part. Once the metal has cooled sufficiently, the mold is broken away to reveal the casting.
6. Finishing The final step in the sand casting process is finishing. This involves removing any unwanted material, smoothing surfaces, and making final adjustments to achieve the desired specifications. This can include machining, grinding, or sandblasting.
sand casting foundry process
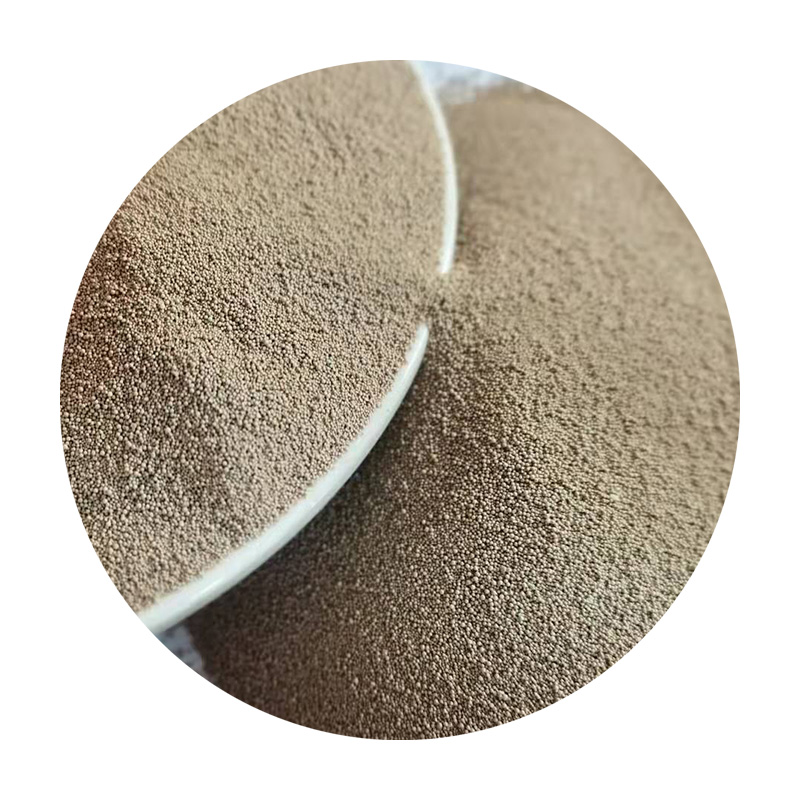
Advantages of Sand Casting
Sand casting offers several benefits that make it a preferred choice in many manufacturing scenarios
- Versatility Sand casting can be used to create components of various sizes, shapes, and materials, making it suitable for numerous applications, from small parts to large engine blocks.
- Cost-Effective The materials used in sand casting are relatively inexpensive, and the process itself is economical for small to medium production runs.
- Complex Geometries Sand casting allows for the production of complex geometries and details that might be difficult or impossible to achieve with other manufacturing methods.
- Low Setup Time Compared to other casting processes, the setup time for sand casting is often shorter, allowing for quicker turnarounds in production.
Applications of Sand Casting
Sand casting is used in a variety of industries, including automotive, aerospace, and manufacturing. It is commonly employed to produce engine blocks, transmission cases, and other intricate components. Additionally, it is an essential method for producing custom parts in small quantities, where traditional manufacturing techniques may be less feasible.
In conclusion, the sand casting foundry process remains a vital method of producing metal components due to its versatility, cost-effectiveness, and ability to create complex shapes. As technology continues to advance, the process is likely to evolve further, incorporating new techniques and materials to improve efficiency and product quality.
Post time:Aug . 10, 2024 00:15
Next:Innovative Solutions for High-Quality Sand Casting Services Tailored to Your Manufacturing Needs