Understanding Large Sand Casting Techniques and Applications
Large sand casting is an essential manufacturing process widely used in various industries to produce complex metal components of significant size and weight. The method encompasses a set of techniques that involve pouring molten metal into molds made from sand, which acts as a temporary receptacle for the metal until it solidifies and can be removed. This article delves into the advantages, techniques, and applications of large sand casting, highlighting its importance in modern manufacturing.
The Advantages of Large Sand Casting
One of the primary advantages of large sand casting is its cost-effectiveness. Compared to other casting methods, such as die casting or investment casting, sand casting is relatively inexpensive, especially for larger components. The materials required—primarily sand, binder, and metal—are readily available and affordable. Furthermore, the setup for sand casting is less complex, allowing for shorter lead times and the ability to produce intricate shapes that would be challenging with other techniques.
Another notable advantage is the flexibility of the process. Sand molds can be easily adapted to create custom designs, making large sand casting a preferred choice for producing one-off components or small runs. The ability to modify molds quickly without significant additional costs enhances its appeal among manufacturers. Moreover, the casting process can accommodate a wide variety of metals, including aluminum, iron, and steel, providing options based on the specific requirements of the part being produced.
Techniques of Large Sand Casting
The large sand casting process typically involves several key steps mold creation, pouring, cooling, and finishing.
1. Mold Creation Initially, a pattern—usually made from metal, wood, or plastic—is created to form the mold. The pattern is placed in a flask (a box-like structure), and sand mixed with a binding agent is packed around it. This forms a mold cavity when the pattern is removed. For large castings, making a cope and drag separation is crucial to facilitate easier mold removal and ensure structural integrity.
large sand casting
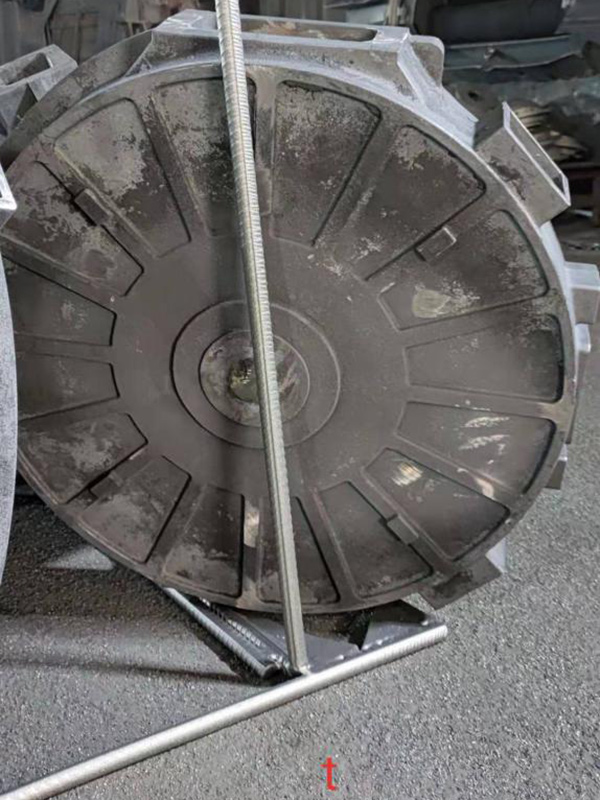
2. Pouring Once the molds are prepared and compacted, molten metal is poured into the cavity. This step must be executed carefully to avoid defects like cold shuts or inclusions, which can affect the final product’s quality.
3. Cooling After pouring, the metal is allowed to cool and solidify. The cooling rate can significantly influence the casting's properties; therefore, careful control is essential.
4. Finishing Once solidified, the sand mold is broken away to reveal the casting. The final step involves machining, sanding, or other processes to achieve the required surface finish and tolerances.
Applications of Large Sand Casting
Large sand casting finds applications in a plethora of industries, including automotive, aerospace, energy, and construction. For instance, components such as engine blocks, turbine housings, and pump casings are commonly produced using this method. In the automotive industry, large sand castings are vital for manufacturing parts that require durability and strength, ensuring that they can withstand rigorous operating conditions.
In the aerospace sector, precision is paramount, and many large sand-casted components must meet strict regulatory standards. Additionally, with the increasing shift toward renewable energies, large sand casting is employed in producing parts for wind turbines and generators. The versatility of this casting method allows it to cater to a wide range of applications, making it an indispensable technique in modern manufacturing.
Conclusion
Large sand casting remains a cornerstone of the manufacturing industry due to its cost-effectiveness, flexibility, and ability to produce complex shapes and large components. As technology advances, the methods and materials used in sand casting continue to evolve, further enhancing its capabilities and applications. Whether in the automotive sector or renewable energy, large sand casting is poised to remain a vital process for producing quality metal parts for years to come.
Post time:Aug . 06, 2024 03:36
Next:Exploring the Benefits and Applications of Resin Coated Sand in Modern Industry