Understanding Resin Coated Sand Advantages and Applications
Resin coated sand is a specialized material widely employed in the foundry industry, primarily for metal casting processes. As an enhanced alternative to traditional sand, resin coated sand offers several advantages that have made it a popular choice among manufacturers seeking precision and quality in their casting operations.
At its core, resin coated sand consists of sand grains that are coated with a thermosetting resin, which, when heated, bonds the sand particles together. This process creates a strong and durable mold that significantly improves the quality of the final casting product. The primary types of resins used include phenolic, furan, and epoxy resins, each providing unique benefits depending on the specific requirements of the casting process.
One of the significant advantages of resin coated sand is its excellent dimensional accuracy. The molds produced from this material offer exceptional precision, allowing for intricate designs and tight tolerances that are often difficult to achieve with traditional sand molds. As industries increasingly demand high-quality castings with reduced defects, the use of resin coated sand becomes an attractive option.
Another benefit is the enhanced mechanical properties of the molds. The resin coating increases the strength of the sand mold, reducing the likelihood of deformation during the casting process. This increased strength allows for the production of complex shapes, including those with thin walls and intricate features, which are essential in industries such as automotive, aerospace, and machinery manufacturing.
resin coated sand
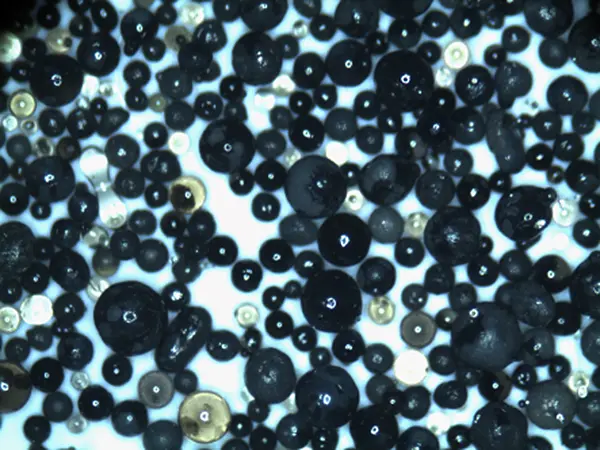
In addition to its mechanical advantages, resin coated sand also provides improved surface finish for castings
. The smooth surface of the molds leads to better-defined details on the final products, resulting in reduced post-processing requirements. This not only saves time and resources but also enhances the aesthetic quality of the cast components, making them suitable for a broader range of applications.Moreover, resin coated sand is known for its excellent thermal properties. The resin coating allows the sand to withstand higher temperatures, making it suitable for casting metals with high melting points, such as aluminum and iron. This characteristic broadens the scope of materials that can be effectively cast using this technology, opening up new possibilities for product development.
Another noteworthy aspect of resin coated sand is its recyclability. After the casting process, the sand can be reclaimed and reused multiple times, provided that it is adequately processed. This feature not only reduces waste and lowers production costs but also aligns with modern sustainability practices, making it an environmentally friendly option in metal casting.
Despite its numerous advantages, there are challenges associated with the use of resin coated sand. The production process requires careful handling and precise control of parameters to ensure optimal properties of the coated sand. Additionally, the initial cost of resin coated sand can be higher than traditional sand, although this is often offset by the improvements in product quality and yield.
In conclusion, resin coated sand plays a crucial role in modern metal casting operations, offering outstanding benefits in terms of accuracy, strength, thermal resistance, and surface quality. Its ability to facilitate the production of complex geometries while being recyclable makes it a valuable resource in various industrial applications. As technology continues to advance, the demand for precise and high-quality castings will likely drive further innovations and applications of resin coated sand in the foundry industry. This enhanced material is indeed paving the way for a new era in casting processes, where efficiency and quality go hand in hand.
Post time:Aug . 06, 2024 02:30
Next:Innovative Ceramics for Advanced Applications in Industry and Technology Enhancement