The World of Sand Foundries An Overview
Sand foundries have been pivotal in the manufacturing landscape, playing a crucial role in producing metal castings that are essential across various industries. The traditional method, which has evolved over centuries, employs sand as the primary mold material. This article delves into the workings, advantages, and future of sand foundries.
Understanding Sand Foundries
At its core, a sand foundry operates by creating molds from sand, which is then filled with molten metal to create desired shapes. The process begins with preparing a mixture of sand, clay, and water, forming a mold that can withstand the heat of molten metal. There are two primary types of sand used in foundries green sand, which is a mixture of sand, clay, and moisture, and resin-bonded sand, which uses resin as a binding agent.
Once the mold is prepared, liquid metal is poured into it, cooled, and solidified. After cooling, the mold is broken apart, revealing the cast metal object. This method is favored for its versatility, allowing for the production of intricate designs and complex geometries.
Advantages of Sand Casting
The advantages of sand casting make it a popular choice for many manufacturers. Firstly, the process is highly adaptable, capable of producing small one-off items as well as large quantities of castings. It is also cost-effective, especially for small production runs, since it requires less initial investment in tooling compared to other casting methods.
Additionally, sand casting can accommodate a wide range of metals, including iron, steel, aluminum, and copper, making it suitable for various industries. The ability to easily modify molds allows for rapid prototyping and innovation, essential in today’s fast-paced market.
sand foundry
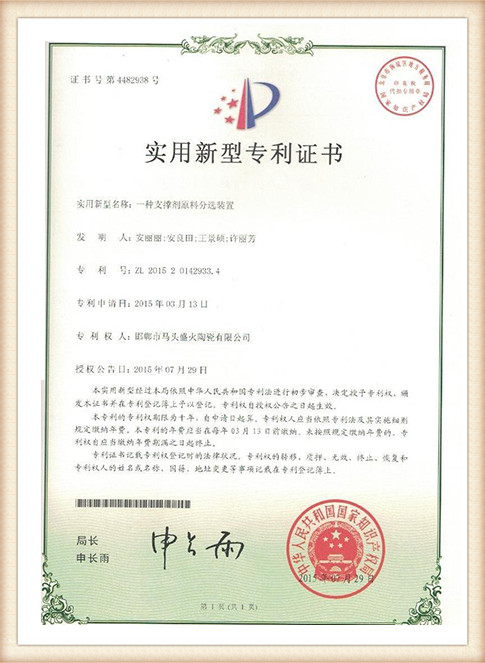
Applications of Sand Casting
The applications of sand casting are vast. It is employed in automotive manufacturing for engine blocks, transmission cases, and other critical components. In the aerospace sector, it’s used for producing complex parts that require precise specifications. Beyond transportation, sand foundries serve industries like construction, agriculture, and energy, creating everything from large machinery parts to decorative elements in architecture.
Environmental Considerations
While sand foundries provide numerous benefits, they also present environmental challenges. The process generates waste materials, and the dust from sand can create air quality issues. Consequently, many foundries are adopting sustainable practices, such as recycling spent sand, reducing energy consumption, and implementing dust control measures. Innovations like 3D printing technology are also being explored to minimize waste and enhance production efficiency.
The Future of Sand Foundries
Looking ahead, the future of sand foundries appears promising, driven by technological advancements and an increasing focus on sustainability. The integration of automation and digital technologies is enabling foundries to enhance production efficiency, improve precision, and reduce human error. Moreover, the rise of additive manufacturing techniques is transforming traditional processes, allowing for faster prototyping and reduced lead times.
In conclusion, sand foundries remain a cornerstone of the manufacturing industry, offering unmatched flexibility and a wide range of applications. As the industry adapts to new technologies and environmental challenges, sand foundries are likely to continue evolving, ensuring that they remain relevant in a dynamic and competitive marketplace. Their role in producing high-quality metal castings will be indispensable in meeting the growing demands of various sectors, from automotive to aerospace and beyond.
Post time:Aug . 12, 2024 20:46
Next:Advancements in Three-Dimensional Sand Printing Technology for Innovative Manufacturing Solutions