The Revolution of 3D Sand Printing Transforming Industries
In recent years, 3D printing has emerged as a groundbreaking technology that has transformed various industries, from healthcare to manufacturing. Among its many applications, 3D sand printing stands out as a game changer, particularly in the realm of foundry and construction. Utilizing sand as its primary material, this innovative technique offers numerous advantages, including reduced waste, faster production times, and the ability to create complex geometries that were previously unachievable with traditional methods.
3D sand printing is a form of additive manufacturing that employs a layer-by-layer approach to create sand molds and cores. This process begins with a digital 3D model designed using computer-aided design (CAD) software. The printer then selectively binds sand particles together using a liquid binder, thereby building up the desired shape. Once the printing is complete, the unbound sand is simply brushed away, leaving behind the intricately designed mold. This method significantly reduces the need for tooling, which is often time-consuming and costly in traditional manufacturing processes.
The Revolution of 3D Sand Printing Transforming Industries
Moreover, 3D sand printing drastically minimizes material waste. Conventional casting processes often involve excess material that must be machined away after production. This can lead to increased costs and significant environmental impact. However, with 3D sand printing, the precise amount of material is used to create the mold, significantly reducing the waste generated in the production process.
3d sand printing
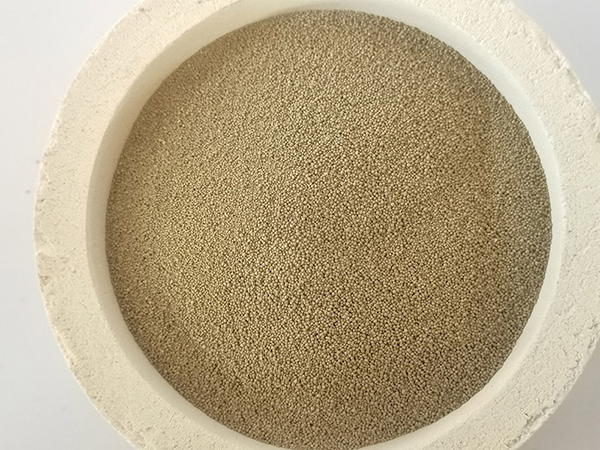
In addition, the capability to produce complex geometries opens up new possibilities for design and innovation. Engineers and designers can experiment with intricate shapes and structures that were once impossible to achieve. This flexibility not only allows for creativity in design but also enables the production of lightweight components that do not compromise on strength or durability. For instance, the aerospace industry is particularly interested in using 3D sand printing for creating lightweight yet robust components, resulting in improved fuel efficiency and performance.
Furthermore, the rise of 3D sand printing technology has implications for sustainability. As industries look to reduce their carbon footprint, the reduction in waste and energy consumption associated with 3D sand printing presents an attractive option. Companies can produce parts more sustainably, aligning their operations with global goals for environmental responsibility.
Despite the numerous benefits, 3D sand printing does face some challenges. Initial setup costs can be high, and the technology is still relatively new, leading some companies to hesitate before adopting it. Moreover, ongoing research and development are essential to maximize the potential of 3D sand printing and improve the reliability of output.
Ultimately, as the technology matures and becomes more accessible, 3D sand printing is poised to revolutionize the manufacturing landscape. Its advantages in efficiency, waste reduction, and design flexibility present compelling reasons for industries to embrace this innovative method. From producing intricate molds for complex machinery to crafting unique components in the automotive and aerospace sectors, 3D sand printing is transforming not only how products are made but also the very nature of manufacturing itself. As we move forward, it will be exciting to witness the ongoing evolution of this technology and the incredible possibilities it holds for the future.
Post time:Aug . 12, 2024 20:26
Next:Exploring the Benefits and Techniques of Sand Casting for Iron Manufacturing Processes