Understanding Sand Casting and Its Different Types of Sand
Sand casting is one of the oldest and most versatile metal casting processes used to create complex shapes and structures. This technique involves pouring molten metal into a mold formed from sand, which is then allowed to cool and solidify. The properties of the sand used in this casting process are crucial to the quality and precision of the final product. Various types of sand are available, each with its unique characteristics and applications. In this article, we explore the various types of sand used in sand casting.
1. Silica Sand
Silica sand is the most common type of sand used in sand casting. It consists primarily of silicon dioxide (SiO2) and is known for its high melting point and excellent thermal stability. Silica sand is effective due to its ability to retain heat, making it suitable for molds that require quick solidification. In sand casting, silica sand is often mixed with binders to enhance its strength and cohesion, enabling it to withstand the forces during metal pouring.
2. Green Sand
Green sand is another well-known material in sand casting, consisting of silica sand mixed with clay, water, and other additives. The term green refers to the fact that the sand is damp and not yet cured. Green sand molds are favored for their excellent flowability and the ability to hold fine details, making them perfect for intricate patterns. This type of sand can be easily reworked and reused, which makes it a cost-effective option for many foundries.
3. Resin Sand
sand casting sand types
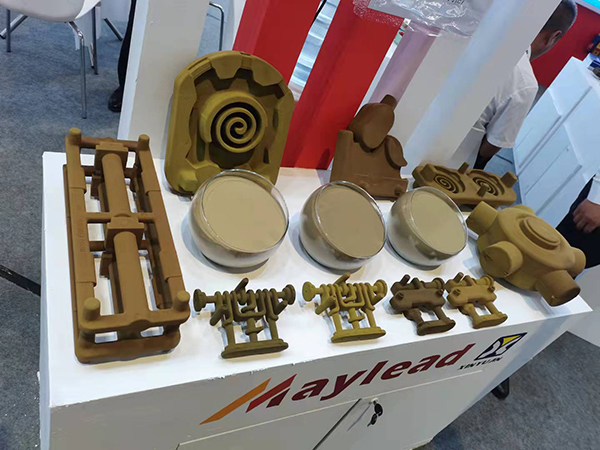
Resin sand is a modern alternative to traditional sand casting materials. It is made by mixing silica sand with a resin binder, which is then cured with heat or chemical catalysts. This type of sand provides superior strength and can produce highly accurate molds with smoother surfaces than green sand. Resin sand is ideal for producing complex shapes and is often used in high-production settings or situations where fine tolerances are required.
4. No-bake Sand
No-bake sand, also known as cold-box sand, is another type used in sand casting. This sand is combined with a resin that cures at room temperature, eliminating the need for heat during the curing process. No-bake sand allows for the creation of molds with excellent dimensional accuracy and surface finish, making it a popular choice for producing intricate components. Furthermore, no-bake sand molds can handle higher pouring temperatures, which is particularly beneficial for certain metal alloys.
5. Shell Molding Sand
Shell molding sand consists of fine silica sand coated with a thermosetting phenolic resin. This sand is used to create thin-walled molds, which are highly durable and provide excellent surface finishes. The shell molding process involves heating the mixed sand, which causes the resin to bond with the sand grain, forming a rigid shell around a pattern. This technique is especially useful in producing high-precision castings for automotive and aerospace applications.
Conclusion
In conclusion, the choice of sand type in the sand casting process significantly affects the quality, detail, and efficiency of the final product. Each type of sand offers unique benefits suited for various applications, from the traditional green sand to modern resin and no-bake sands. Understanding the characteristics of these sands allows engineers and foundry professionals to select the best materials for their specific casting needs, ultimately leading to the production of high-quality cast metal parts. As technology and materials science continue to evolve, the future of sand casting holds promising opportunities for innovation and enhanced performance.
Post time:Jul . 29, 2024 21:54
Next:Understanding the Process and Benefits of Sand Casting in Metal Manufacturing Techniques