Understanding Sand Casting A Key Foundry Process
Sand casting, also known as sand molded casting, is one of the oldest and most widely used casting processes in metalworking. With a history that spans thousands of years, it continues to play a crucial role in various industries, including automotive, aerospace, and construction. In this article, we will delve into the sand casting process, its advantages, applications, and some best practices for achieving high-quality results.
What is Sand Casting?
At its core, sand casting involves creating a mold from sand in which molten metal is poured to create a desired shape. The primary materials used in sand casting are silica sand, a bonding agent (usually clay), and water. These materials come together to create a mold that can withstand the heat of molten metal.
The process begins with the creation of a pattern, which is a replica of the final product. Patterns are typically made from materials such as wood, metal, or plastic. Once the pattern is prepared, it is placed in a mold box, and sand is packed around it to form the mold. The sand is compressed and held together using the bonding agent.
After the mold is created, it is carefully opened to remove the pattern, leaving behind a cavity in the shape of the desired part. The two halves of the mold are then reassembled, and molten metal is poured into the cavity. Once the metal cools and solidifies, the mold is broken apart, and the cast part is removed.
Advantages of Sand Casting
One of the significant advantages of sand casting is its versatility. This process can accommodate a wide range of metals, including aluminum, iron, brass, and bronze, making it suitable for producing parts that vary in size and complexity. Additionally, sand casting is ideal for both small-scale production and large batch runs, making it a cost-effective choice for manufacturers.
Another benefit is the relative simplicity of the process. Sand is readily available, and the equipment needed for sand casting is not overly complex or expensive compared to other casting methods. This makes it accessible for foundries and manufacturers of various sizes.
Additionally, sand casting allows for intricate designs and geometries. The ability to create complex shapes with internal features is particularly advantageous for many industries. Moreover, the surface finish of sand-cast parts can be improved through secondary operations, such as machining or grinding, if necessary.
Applications of Sand Casting
what is a sand casting
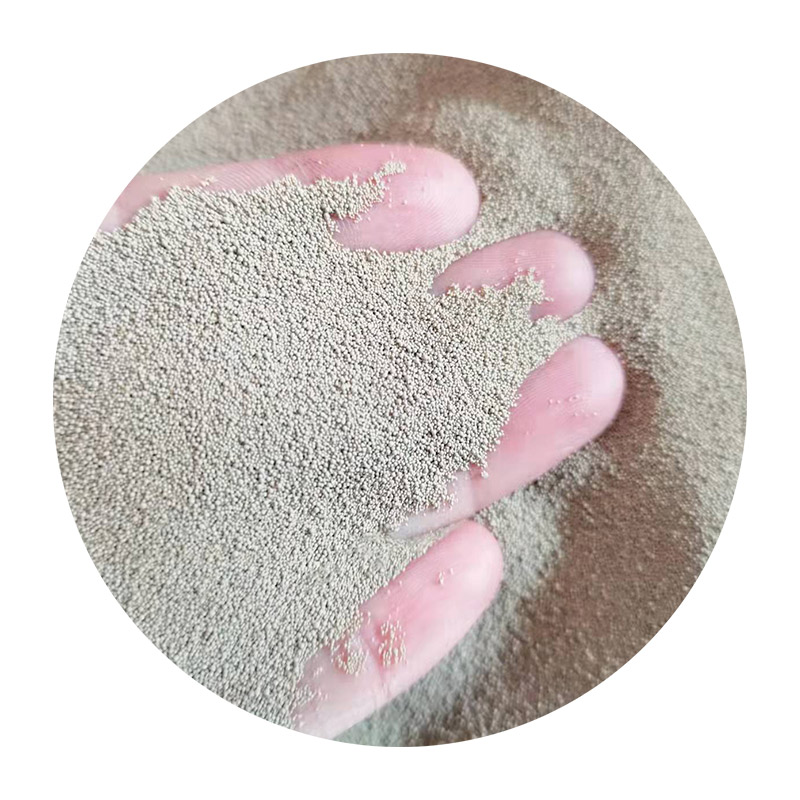
Sand casting is employed in various sectors due to its adaptability. In the automotive industry, it is used to produce engine blocks, cylinder heads, and various other components. The aerospace sector also relies on sand casting for critical parts, such as turbine housings and brackets.
Furthermore, sand casting is prevalent in manufacturing large components like pipes, valves, and pump casings used in construction and infrastructure. Its suitability for producing heavy machinery parts contributes to its ongoing relevance and demand.
Best Practices for High-Quality Sand Casting
To achieve high-quality sand castings, several best practices should be followed
1. Pattern Design Ensure that the pattern is designed with proper allowances for shrinkage and draft angles to facilitate easy removal from the mold.
2. Material Selection Use high-quality sand and bonding agents to enhance mold strength and durability. Properly graded sand will help achieve better surface finish and dimensional accuracy.
3. Mold Preparation Properly compact the sand in the mold to prevent defects such as sand blowholes or misalignment.
4. Control of Pouring Temperature Maintain an appropriate pouring temperature for the metal to prevent defects such as oxidation or entrapment of gases.
5. Quality Inspection Implement regular inspections throughout the process to monitor for defects and ensure that specifications are met.
In conclusion, sand casting remains a vital process in the manufacturing landscape, offering a blend of versatility, accessibility, and cost-efficiency. As industries continue to evolve, this traditional method adapts, proving that even the oldest techniques can still hold their ground in a modern context.
Post time:Jul . 29, 2024 21:46
Next:Innovative Techniques for 3D Printed Sand Casting Patterns in Modern Manufacturing Applications