Steps in Sand Casting
Sand casting is one of the oldest and most widely used methods for metal casting. It is a versatile technique suitable for creating complex shapes and large parts, making it an essential process in various industries, including automotive, aerospace, and manufacturing. This article outlines the critical steps involved in sand casting, providing a comprehensive overview of this fascinating process.
1. Pattern Making
The first step in sand casting involves creating a pattern, which is a replica of the final product to be cast. Patterns can be made from various materials, including wood, metal, or plastic, depending on the size and complexity of the component. The pattern is usually made slightly larger than the final part to account for material shrinkage during cooling. This pattern serves as a template for creating the mold.
2. Mold Preparation
Once the pattern is ready, the next step is to prepare the mold. This is done by placing the pattern in a mold box, typically made of two parts the cope (top half) and the drag (bottom half). Sand mixed with a binding agent (such as clay) is packed tightly around the pattern to form the mold. The sand must be compacted sufficiently to hold its shape when the pattern is removed. After packing the sand, the pattern is carefully removed, leaving a cavity that mirrors the shape of the desired part.
3
. Core MakingIf the casting requires internal features or cavities, cores are added to the mold. Cores are separate pieces made from materials similar to the molding sand, which create voids in the final casting. They are placed in the mold cavity before pouring the molten metal. The core must be designed and positioned correctly to ensure that it holds its shape during the casting process.
4. Melting the Metal
steps in sand casting
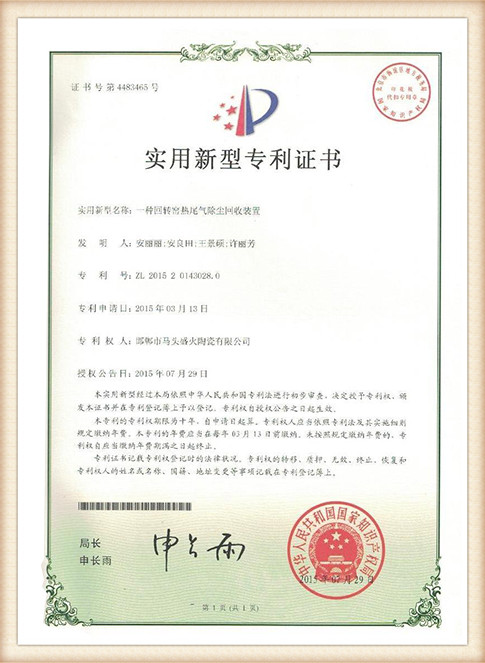
With the mold and cores prepared, the next step is to melt the metal to be cast. This process usually takes place in a furnace, where the raw metal (such as aluminum, iron, or bronze) is heated until it reaches a molten state. The temperature and duration of melting depend on the type of metal used. Safety precautions are crucial during this stage, as molten metal poses significant risks.
5. Pouring the Metal
Once the metal is melted, it is poured into the mold through a system of gates and runners, which ensure proper flow and distribution. The pourer must work quickly and accurately to minimize the risk of defects related to cooling or premature solidification. The pouring temperature and speed are critical factors that impact the overall quality of the casting.
6. Cooling
After the molten metal is poured into the mold, it begins to cool and solidify. The cooling time varies depending on the size and complexity of the casting as well as the type of metal used. During this phase, it is essential to monitor the temperature to avoid stress and cracking in the casting. Once completely cooled, the mold is broken open to reveal the casting.
7. Finishing
The final step in the sand casting process is finishing. The casting is often coated with sand, which may need to be removed through sandblasting or grinding. It may also require additional machining to achieve precise dimensions and a smooth surface finish. This step can include processes such as drilling, sanding, or milling, depending on the requirements of the final product.
Conclusion
Sand casting is a time-tested method for producing complex metal parts with various applications. From pattern making to finishing, each step plays a crucial role in ensuring the quality and integrity of the final casting. Understanding these steps not only highlights the intricacies of the sand casting process but also showcases its importance in modern manufacturing. Whether in large-scale production or custom one-off projects, sand casting remains a cornerstone of metalworking techniques worldwide.
Post time:Aug . 16, 2024 18:05
Next:Various Categories of Sand Casting Techniques and Their Applications