Different Types of Sand Casting
Sand casting is one of the oldest and most versatile metal casting processes used in manufacturing. It involves creating a mold from sand, which is then used to form metal parts by pouring molten metal into the mold cavity. This process has been utilized for centuries due to its simplicity and the ability to create complex shapes. Within sand casting, there are various types, each with unique characteristics and applications. In this article, we will explore some of the most common types of sand casting and their respective advantages.
1. Green Sand Casting
Green sand casting is the most traditional type of sand casting. It uses a sand mixture that contains clay, water, and sand. The term green refers to the mold's state before it is dried or baked. The sand is moldable and can hold its shape when compressed. This method is highly favored for its cost-effectiveness and the ability to produce intricate designs. Green sand molds are easy to work with, making them suitable for both small and large production runs. However, one of the downsides is that green sand molds can have a limited lifespan; they may need to be reformed after a few casts.
Unlike green sand, dry sand casting utilizes sand that is baked or dried before the molten metal is poured in. The drying process hardens the mold, making it more durable than green sand molds. This type of casting is ideal for producing high-precision components due to its superior dimensional stability. Dry sand molds can also withstand higher temperatures, making them suitable for materials that require precise casting. Although dry sand casting tends to be more expensive than green sand casting, the improved quality and finish often justify the increased costs.
different types of sand casting
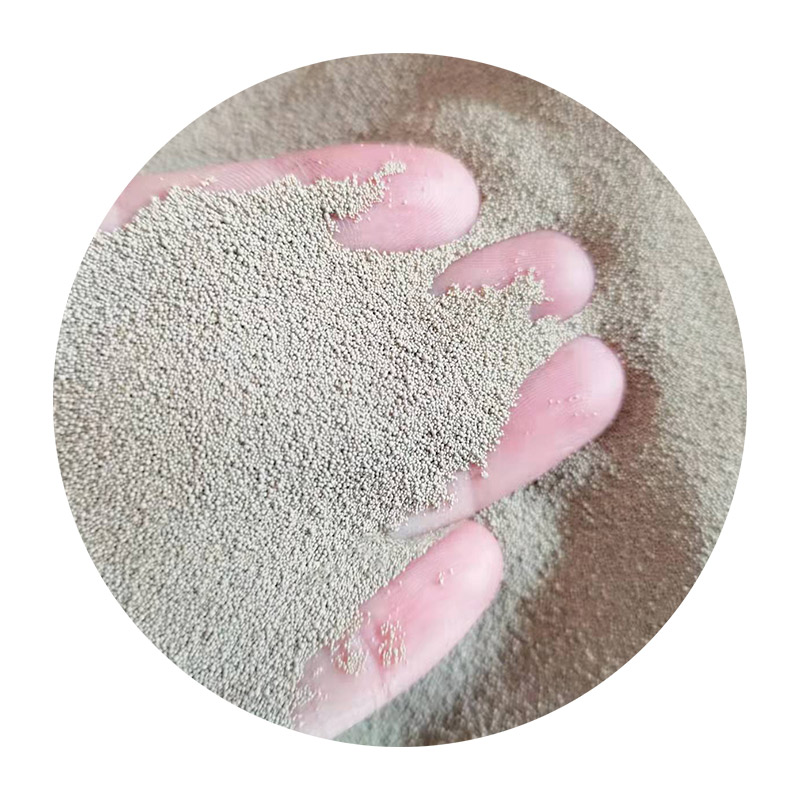
3. Sodium Silicate Sand Casting
Sodium silicate sand casting utilizes a chemical binder in its composition, making the sand molds rigid and strong. This type of sand casting is known for its ability to produce molds that have excellent surface finishes and high detail. The process often involves a gas hardening step where carbon dioxide is introduced, solidifying the sand and binder mixture. Sodium silicate molds can handle high pouring temperatures and are particularly advantageous for creating high-strength components. However, they may involve more complicated preparation and handling processes in comparison to traditional sand types.
4. Shell Mold Casting
Shell mold casting is a more advanced form of sand casting that employs a thin shell of sand and resin to create a mold. In this method, a heated metal pattern is coated with a mixture of sand and resin, which hardens when in contact with the hot surface. The resulting shell is thinner and provides a much better surface finish than traditional sand molds. Shell mold casting is best suited for small and medium-sized production runs and is highly regarded for producing intricate and detailed parts with excellent dimensional tolerance. Its main drawback lies in the higher material cost and complexity of the process.
Conclusion
Sand casting remains a fundamental technique in the manufacturing industry, with various types to suit different needs. From traditional green sand to advanced shell mold casting, each type offers unique benefits tailored to specific applications. Understanding the characteristics of each sand casting method is essential for manufacturers to choose the right process for their projects, ensuring optimal quality, efficiency, and cost-effectiveness in their production endeavors. As technology advances, the versatility and relevance of sand casting continue to play a crucial role in the production of metal components across various industries.
Post time:Aug . 16, 2024 17:27
Next:Exploring the Art and Techniques of Sand Casting for Metal Fabrication