Types of Sand Used in Foundry
Foundries are essential facilities in the metalworking industry, where metal casting is performed to produce a variety of components and structures. One of the most crucial materials used in foundry processes is sand. Various types of sand are employed in foundry applications, each with its unique properties and advantages. This article explores the main types of sand used in foundry practices, emphasizing their characteristics and the reasons for their selection.
1. Silica Sand
Silica sand is the most commonly used sand in many foundry operations. Composed primarily of silicon dioxide (SiO2), this type of sand is valued for its high melting point, excellent thermal stability, and good refractoriness. Silica sand is ideal for producing molds and cores due to its ability to withstand high temperatures. It can be found in various grades, providing options for foundries to choose the suitable size for their casting needs. Additionally, silica sand can be treated and coated to enhance its properties further, making it highly versatile for various metal types.
2. Green Sand
Green sand is a mixture of silica sand, clay, water, and various additives. It is one of the oldest and most widely used molding materials in the foundry industry. The term green refers to the moisture content in the sand, which provides the necessary binding properties. Green sand molds are easy to work with, allow for good detail replication, and are economical to produce. However, the properties of green sand can vary depending on the clay content and the fineness of the sand used. Clay provides additional binding strength, crucial in holding the mold together during the casting process.
3. Resin Sand
types of sand used in foundry
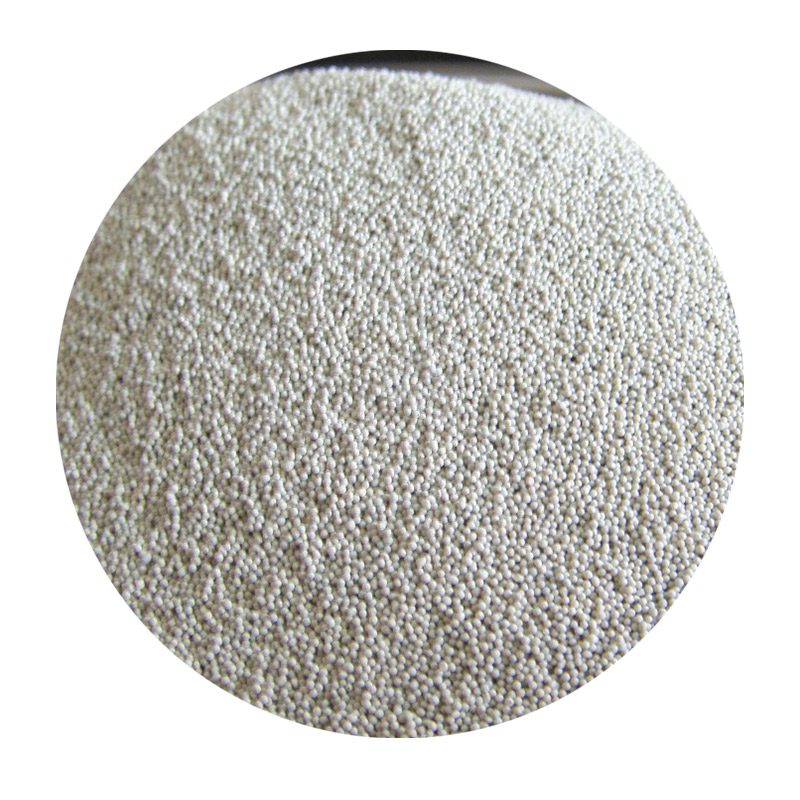
Resin sand, also known as chemically bonded sand, utilizes a resin binder alongside silica sand. The resin enhances the sand's properties, making it more durable, stronger, and capable of producing finer details in castings. Unlike green sand, resin sand molds are not dependent on moisture, making them suitable for high-temperature applications and complex geometries. One of the significant advantages of resin sand is its ability to be reused multiple times, supporting sustainability in foundry operations. However, the process requires careful handling of chemicals and adherence to environmental regulations.
4. Investment Sand
Investment sand is used in investment casting, a method that produces highly accurate and intricate parts. This type of sand is coated with a thin layer of a ceramic material, allowing for smooth surface finishes and precise detail in the final products. Investment casting often utilizes patterns made from wax or other materials, which are later removed, leaving a cavity for pouring molten metal. The need for high precision and surface quality makes investment sand particularly suitable for creating components in the aerospace and medical industries, where tolerances are critical.
5. Chromite Sand
Chromite sand, derived from chromite ore, is prized for its high thermal conductivity and resistance to erosion. It possesses excellent refractoriness, making it ideal for use in casting high-performance steels and nickel-based alloys. Chromite sand also has the added benefit of minimizing the formation of defects in castings, such as metal penetration or inclusions, which can compromise the integrity of the final product. Its unique properties make it a preferred choice in specialized foundries focusing on high-end applications.
In conclusion, the choice of sand in foundry operations significantly influences the quality and performance of the final cast products. Understanding the various types of sand available, including silica sand, green sand, resin sand, investment sand, and chromite sand, allows foundries to select the appropriate material that best meets their specific casting requirements. Each type of sand offers distinct advantages, catering to the diverse needs of the metalworking industry from traditional practices to advanced applications.
Post time:Aug . 17, 2024 19:04
Next:Understanding the Sand Casting Process and Its Key Steps for Successful Manufacturing