Sand Casting Procedure An Overview
Sand casting, also known as sand mold casting, is a versatile and widely used manufacturing process that involves creating metal castings. It is an ancient technique that has been refined over the years and remains popular in various industries due to its simplicity, cost-effectiveness, and ability to produce complex shapes. This article will provide a step-by-step overview of the sand casting procedure.
1. Pattern Making
The first step in the sand casting process is the creation of a pattern, which is a replica of the desired final product. Patterns can be made from various materials, including wood, metal, or plastic. The choice of material largely depends on the durability required and the number of casts needed. The pattern is typically designed to be slightly larger than the final product to account for shrinkage that occurs during the cooling process.
2. Mold Preparation
Once the pattern is ready, the next step is to prepare the sand mold. Sand casting uses a mixture of sand, clay, and water to create a mold. The sand is compacted around the pattern to form the mold cavity. This is usually done in two halves the cope (the top half) and the drag (the bottom half). Each half of the mold is made in a separate box called a flask.
To enhance the mold's strength and improve its ability to retain shape, a binder like clay is added to the sand mixture. The preparation of the mold requires skill to ensure that the sand is evenly packed and that the pattern is accurately captured.
3. Cores (if necessary)
In some cases, cores are used to create internal features or hollow sections in the casting. Cores are made from similar sand mixtures and are placed within the mold before the metal is poured. This allows for more complex shapes that cannot be achieved with a single mold.
sand casting procedure
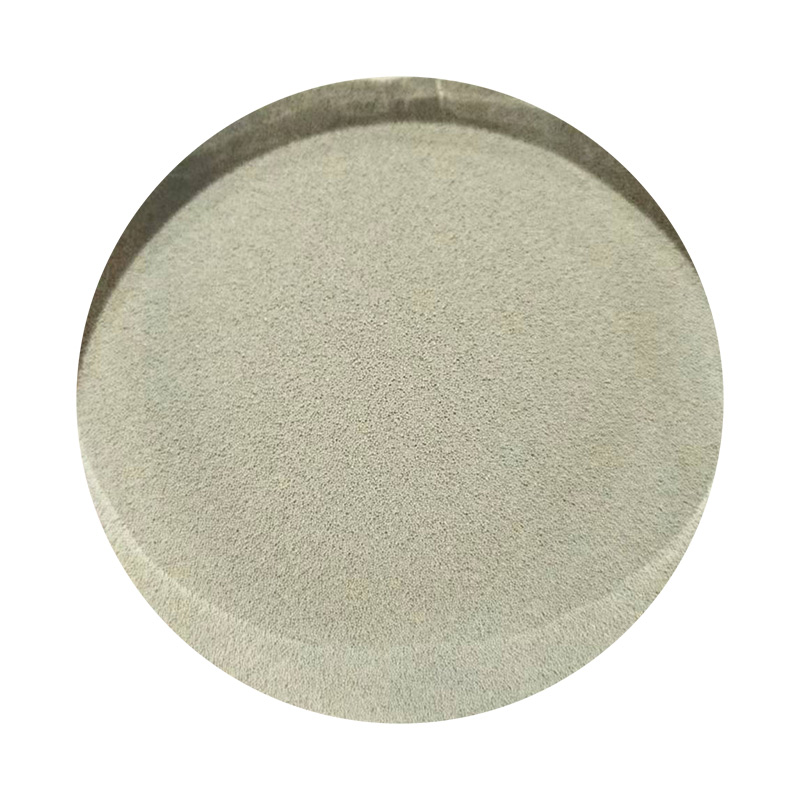
The next step involves melting the metal that will be poured into the mold. Common metals used in sand casting include aluminum, bronze, and iron. The metal is heated in a furnace until it reaches a molten state. The temperature and composition of the molten metal are crucial for ensuring the quality of the final casting.
5. Pouring the Metal
Once the metal is molten, it is poured into the mold cavity. Care must be taken during the pouring process to prevent defects such as air entrapment or turbulence, which can affect the integrity of the casting. The poured metal fills the mold and begins to cool and solidify.
6. Cooling and Shakeout
After the metal has been poured, it is allowed to cool. The cooling time varies based on the thickness of the casting and the type of metal used. Once cooled, the mold is broken apart, and the casting is removed. This process is called shakeout, and it can be done manually or with the use of mechanical equipment.
7. Finishing Operations
After the casting is removed from the mold, it often requires finishing operations to achieve the desired surface finish and accuracy. This can include processes such as trimming excess metal (flash), grinding, sanding, and machining to meet specific tolerances. Inspection is also carried out to ensure that the casting meets quality standards.
Conclusion
The sand casting procedure is a fundamental manufacturing process that has stood the test of time. Its ability to produce complex shapes and accommodate a variety of metals makes it a preferred choice across different industries, from automotive to aerospace. Understanding the steps involved in sand casting is crucial for engineers and manufacturers looking to optimize this process for better efficiency and quality in metal casting. Whether for prototype development or high-volume production, mastering sand casting techniques can lead to significant advantages in the manufacturing landscape.
Post time:Aug . 17, 2024 18:31
Next:Resin Coated Sand Production Facility for Enhanced Performance Applications