The Difference Between Die Casting and Sand Casting
Casting is a fundamental manufacturing process used to create metal parts and components with intricate shapes. Two popular casting techniques are die casting and sand casting. While both methods serve the same primary function of shaping metals, they differ significantly in their processes, materials, costs, and applications. Understanding these differences is crucial for manufacturers and engineers when choosing the suitable casting method for their projects.
Process Overview
Die Casting involves forcing molten metal into a mold cavity under high pressure. The molds, typically made of steel or other durable materials, are designed to produce precise and detailed shapes. This method is particularly suited for mass production since it allows for high-speed production cycles and excellent dimensional accuracy. Die casting is often used for non-ferrous metals, such as aluminum, magnesium, and zinc.
On the other hand, Sand Casting is a more traditional technique that uses sand as the primary mold material. In this process, a pattern of the desired part is created, usually from metal or plastic, and then surrounded by sand mixed with a binder. Once the sand has set, the pattern is removed, leaving a hollow cavity into which molten metal is poured. Sand casting can accommodate a variety of metals, including ferrous and non-ferrous materials.
Material and Mold Reusability
One of the critical differences between the two methods is the material used for molds and the potential for reusability. Die casting molds are generally more expensive but are designed for long-term use and can produce thousands of parts before needing replacement. This makes die casting an efficient option for large-scale manufacturing, despite the higher initial investment.
In contrast, sand casting molds are typically used only once, as the sand mixture is not durable enough for multiple uses. While the initial costs are lower compared to die casting, this means that sand casting may become more expensive for larger production runs due to the need to produce new molds for each batch.
Surface Finish and Tolerances
difference between die casting and sand casting
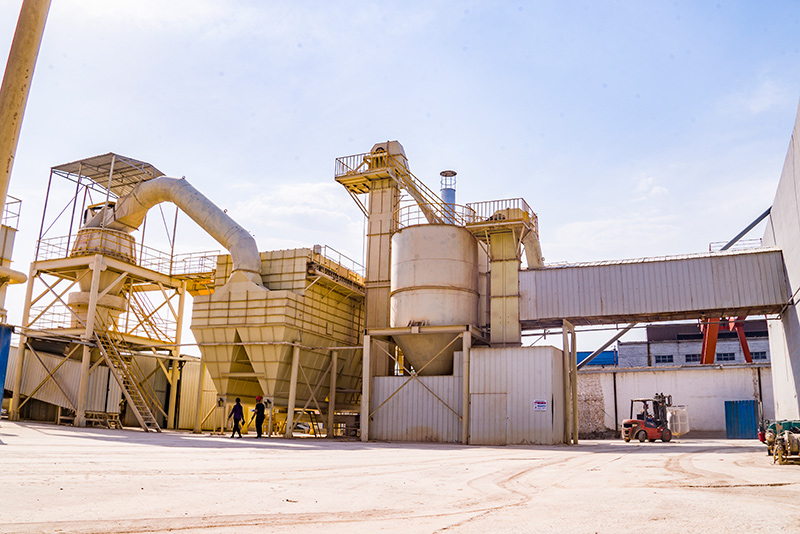
When it comes to surface finish and tolerances, die casting has a significant advantage. The high-pressure injection of molten metal into precisely engineered molds allows for excellent surface finishes and tight tolerances, making this method ideal for intricate parts that require minimal post-processing.
Sand casting, while versatile, generally results in a rougher surface finish and greater tolerance variations. The porous nature of the sand molds can also lead to surface imperfections in the final product. Consequently, components created via sand casting might require additional machining or finishing to meet specific quality standards.
Cost Considerations
The cost implications of each method also differ considerably. Die casting usually has a higher upfront cost due to the investment in molds and machinery. However, the per-unit cost decreases significantly with high-volume production. For smaller production runs or prototype parts, the initial costs may not justify die casting.
In contrast, sand casting has lower initial costs, making it a more economical choice for low-volume production or custom parts. However, the overall production time can be longer, and the variability in quality may lead to higher costs in terms of scrap and rework.
Applications
Both casting methods find their applications in various industries. Die casting is widely used in the automotive, aerospace, and consumer goods sectors for creating complex, high-strength components. In contrast, sand casting is common in the manufacture of large parts, such as engine blocks, pipes, and heavy machinery components.
Conclusion
In summary, the choice between die casting and sand casting depends on several factors, including production volume, cost, material type, and desired surface finish. Die casting excels in high-volume production with tight tolerances and excellent surface quality, while sand casting is ideal for low-volume and custom applications with more intricate shapes. By understanding the key differences between these two casting methods, manufacturers can make informed decisions that best suit their production needs.
Post time:Aug . 11, 2024 01:56
Next:Innovative Approaches to Recycling Foundry Sand for Sustainable Industrial Practices and Environmental Benefits