The Difference Between Die Casting and Sand Casting
When it comes to metalworking and manufacturing, two of the most popular casting methods are die casting and sand casting. Both techniques serve the fundamental purpose of creating metal parts, but they differ significantly in their processes, materials, costs, and applications. Understanding these differences is crucial for manufacturers and designers when choosing the right casting method for their needs.
Process Overview
Die casting is a metal casting process in which molten metal is injected into a mold under high pressure. The molds, often made from steel or other strong alloys, are designed to produce precise and intricate shapes, making die casting particularly suitable for high-volume production. The process operates at high speeds, allowing for rapid cycles and quick turnarounds on production schedules.
In contrast, sand casting utilizes a mold made from sandy material, typically a mixture of sand, clay, and water. The sand is packed around a pattern that mirrors the shape of the desired component. After the sand has set, the pattern is removed, and molten metal is poured into the cavity left by the pattern. Once the metal has cooled and solidified, the sand mold is broken away to reveal the cast part. Sand casting is generally slower than die casting and is preferred for producing larger, more complex shapes or lower-volume runs.
Materials Used
The materials used in both processes also differ. Die casting commonly employs non-ferrous metals, such as aluminum, zinc, and magnesium, due to their flow characteristics and ability to produce a clean, finished surface in intricate designs. This selection of metals contributes to the lighter weight and excellent mechanical properties of die-cast parts, making them ideal for industries like automotive and electronics.
On the other hand, sand casting is versatile in terms of the metals that can be used. It can accommodate ferrous metals, such as cast iron and steel, as well as non-ferrous metals. This flexibility allows sand casting to be used for a wide range of applications, including heavy machinery and structural components, where weight and material properties are paramount.
difference between die casting and sand casting
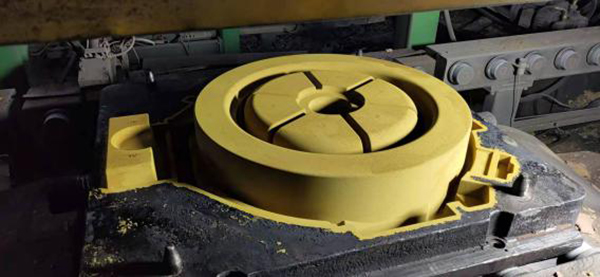
Cost Implications
When comparing cost, die casting typically has a higher initial investment due to the expense of creating durable metal molds
. However, this cost can be justified in high-volume production runs because the per-unit cost decreases significantly with increased output.In contrast, sand casting has a lower initial cost because the molds can be made quickly and relatively inexpensively. However, the per-unit cost can remain higher in comparison to die casting due to the slower production rate. As such, sand casting is often favored for low to medium volume production or for casting large, heavy parts where precision is not as critical.
Applications
Finally, the applications of each casting process highlight their unique advantages. Die casting is extensively used in industries requiring high precision and excellent surface finish, such as automotive engineering, consumer electronics, and aerospace applications. The ability to create highly detailed and consistent parts makes it an excellent choice for mass production.
On the other hand, sand casting is preferred in situations where parts are larger or where flexibility in design is necessary, such as in the creation of custom or low-volume components for heavy equipment, art, or architectural applications.
Conclusion
In summary, the choice between die casting and sand casting hinges on factors such as production volume, the complexity of the part, material properties, and cost considerations. Understanding the key differences between these two casting methods allows manufacturers to make informed decisions that align with their production goals and project requirements.
Post time:Jul . 28, 2024 16:57
Next:Exploring the Techniques and Benefits of Steel Sand Casting in Modern Manufacturing Processes