Steel Sand Casting Process An Overview
Steel sand casting is a traditional and widely recognized manufacturing method used for producing metal parts and components. This process involves pouring molten metal into a mold made of sand, which takes the shape of the desired product. Steel casting is favored for its strength, durability, and versatility, making it applicable in various industries, including automotive, aerospace, construction, and machinery. In this article, we will explore the steel sand casting process, its advantages, and its applications.
At the heart of the steel sand casting process lies the creation of a mold. The molding process typically starts with the preparation of the sand mixture. The sand used in this process is usually a fine-grained silica that is combined with a binder to enhance its cohesion and strength. The mixture is then packed around a pattern that represents the size and shape of the final part. Patterns can be made from a variety of materials, including metal, wood, or plastic, and they are designed with allowances for shrinkage and finishing.
Once the mold is created, it is essential to carefully remove the pattern to leave a cavity that will form the casting. The two halves of the mold, often referred to as cope and drag, are then assembled. Filling the mold with molten steel involves pouring heated steel, typically heated to temperatures around 1400°C to 1500°C. This process can be executed manually or with automated pouring systems.
The molten steel flows into the mold cavity, taking its shape upon cooling. It is crucial to ensure that the pouring is done steadily to avoid defects such as porosity, shrinkage cavities, or uneven thickness. After the pouring process is complete, the molds are allowed to cool. The cooling period can vary, depending on the size and thickness of the casting, typically ranging from a few minutes to several hours.
steel sand casting process
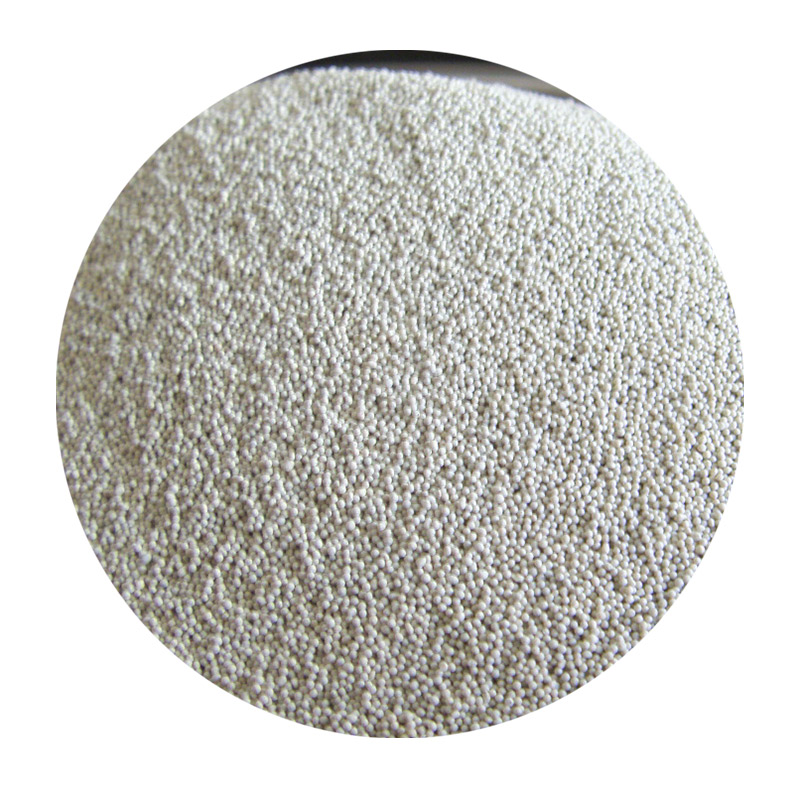
Once the metal has solidified, the molds are broken apart to reveal the cast steel part. This demolding process can be done using mechanical vibration or manual tools, depending on the mold design and complexity. The cast part may feature an array of finishing processes, such as grinding, machining, or surface treatments, to achieve the required tolerances, surface finish, and overall quality.
Steel sand casting offers several advantages. First, it allows for the production of complex shapes and designs that may be difficult or impossible to achieve with other manufacturing methods. Second, the process can be highly efficient, as multiple castings can be produced simultaneously from a single mold. Additionally, sand molds can be reused or recycled, making the process more environmentally friendly.
However, the steel sand casting process does have some drawbacks. For instance, achieving tight tolerances and smooth surface finishes can require significant post-processing, which may increase production time and costs. Furthermore, the method is generally slower compared to modern production techniques such as die casting or 3D printing.
In conclusion, the steel sand casting process plays a crucial role in the manufacturing of a wide range of industrial components. Its ability to produce durable and complex parts makes it a valuable technique in many sectors. While advancements in technology may create new methods, the traditional sand casting process remains relevant, serving as a testament to the enduring strength of this classic manufacturing approach. As industries continue to evolve, the steel sand casting process will likely adapt, integrating new techniques and technologies to meet future demands.
Post time:Jul . 28, 2024 16:19
Next:Exploring the Evolution and Impact of Sand Casting Techniques in Modern Manufacturing Industries