3D Printed Sand Casting Revolutionizing Metal Manufacturing
In recent years, the manufacturing industry has witnessed a technological revolution with the rise of additive manufacturing, commonly known as 3D printing. Among the various applications of this technology, 3D printed sand casting is gaining significant traction, particularly in the realm of metal casting. This innovative approach combines the traditional techniques of sand casting with the precision and efficiency of 3D printing, enabling manufacturers to produce complex metal parts with remarkable accuracy and reduced lead times.
3D Printed Sand Casting Revolutionizing Metal Manufacturing
3D printed sand molds allow for the rapid fabrication of complex geometries that would be challenging or impossible to achieve with traditional methods. Using a binder jetting process, fine sand particles are glued together in a printer to create a mold layer by layer. This method enables the production of intricate designs, such as internal cooling channels or lightweight structures, which enhance the performance of the final casted metal part. Moreover, the ability to iterate designs quickly means that engineers can test and refine their concepts more effectively, thus driving innovation in product development.
3d printed sand casting
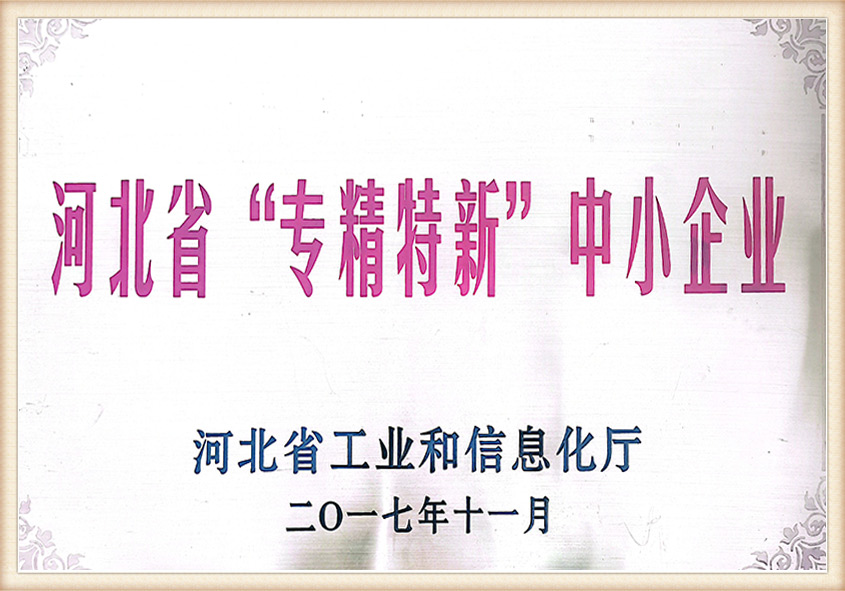
One of the standout advantages of 3D printed sand casting is its potential for reducing lead times. Conventional mold-making can take days or even weeks, depending on the complexity of the part. In contrast, 3D printing a sand mold can often be accomplished in a matter of hours. This rapid production capability not only accelerates time-to-market for new products but also allows for smaller batch sizes and customization without incurring significant additional costs. As industries increasingly lean toward just-in-time manufacturing and short production runs, the flexibility offered by 3D printed sand casting becomes a vital asset.
Furthermore, the environmental impact of manufacturing processes is becoming a critical concern across various sectors. Traditional sand casting methods can generate substantial waste, from raw materials to energy consumption. With 3D printed sand molds, material waste is minimized, as only the necessary amount of sand is used to create the mold. Additionally, the energy savings associated with faster production times and the potential for using recyclable materials further enhance the sustainability of this method.
Industries such as automotive, aerospace, and even art and design are already benefiting from the advancements in 3D printed sand casting. For example, automotive manufacturers are using this technology to fabricate lightweight components that contribute to improved fuel efficiency. Similarly, aerospace companies leverage this technique to produce parts that meet rigorous safety standards while also reducing overall weight.
In conclusion, 3D printed sand casting represents a significant leap forward in the metal manufacturing landscape. With its ability to create complex designs, reduce lead times, minimize waste, and enhance customization options, it is transforming how manufacturers approach product development and production. As technology continues to evolve and more industries recognize the benefits of this method, the future of 3D printed sand casting looks incredibly promising, paving the way for even greater innovations in manufacturing processes.
Post time:Jul . 29, 2024 23:45
Next:Efficient Techniques for Large-Scale Production of Sand Casting Components in the Manufacturing Industry