Sand Casting Mass Production An Overview
Sand casting is one of the most widely used metal casting processes in manufacturing. It involves creating a mold from a mixture of sand, clay, and water, which is then used to shape molten metal into a desired form. This method is particularly popular for mass production due to its cost-effectiveness, flexibility, and ability to produce complex shapes with a high level of detail. In this article, we will explore the key aspects of sand casting mass production, including the process, advantages, and applications.
The Sand Casting Process
The sand casting process begins with the creation of a pattern, which is a replica of the final product. The pattern is often made from materials such as wood, metal, or plastic. Once the pattern is ready, it is placed in a mold box, and a mixture of sand, clay, and water is packed around it to form the mold. The clay acts as a binder, helping to keep the sand grains together during the pouring of the metal.
After the mold is formed, the pattern is removed, leaving a cavity that will shape the molten metal. The next step involves melting the metal, which can be a variety of alloys such as aluminum, iron, or bronze, depending on the requirements of the final product. The molten metal is then poured into the mold cavity through a pouring cup and sprue system. Once the metal cools and solidifies, the sand mold is broken away, revealing the cast part.
Advantages of Sand Casting
One of the primary advantages of sand casting is its low cost, particularly for large-scale production. The materials used in sand casting—sand, clay, and water—are abundant and inexpensive. Additionally, the sand mold can be reused multiple times, significantly reducing production costs. The process is also highly adaptable, allowing manufacturers to create intricate designs and large components that other methods may struggle to achieve.
sand casting mass production
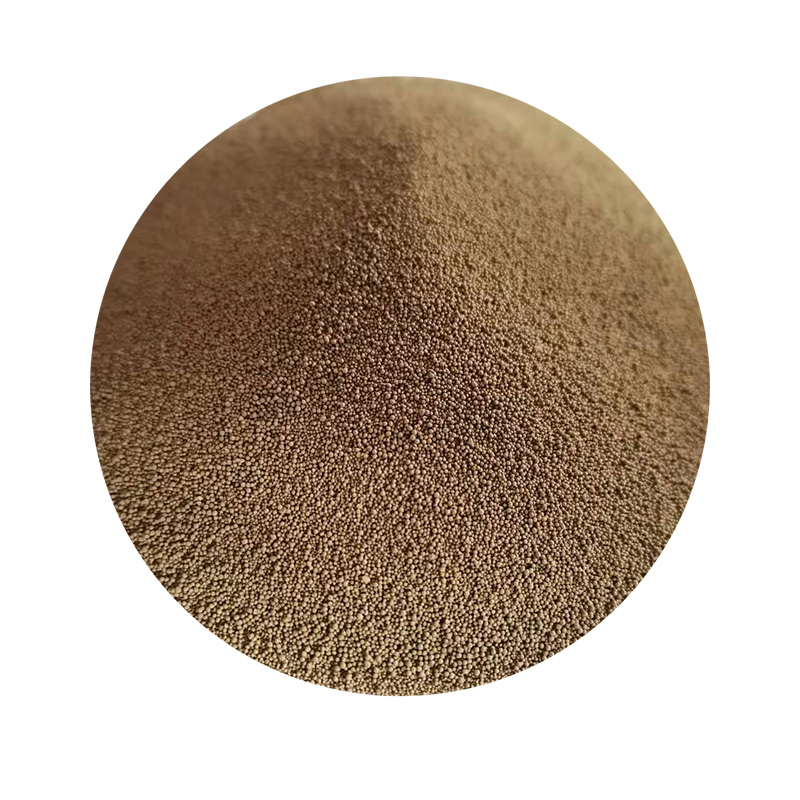
Another major benefit is the versatility of sand casting. It can accommodate a wide range of metal alloys and part sizes, making it suitable for various industries, including automotive, aerospace, and consumer goods. Furthermore, sand casting is capable of producing parts with excellent surface finishes and intricate details, which is crucial for many applications.
Applications of Sand Casting in Mass Production
Sand casting plays a pivotal role in the mass production of metal components across several industries. In the automotive sector, it is commonly used to produce engine blocks, transmission cases, and various structural components. The ability to create large, complex parts quickly and efficiently is essential for manufacturers looking to meet growing consumer demand.
In the aerospace industry, sand casting is utilized to produce intricate parts such as turbine housings and aircraft components. The lightweight nature of aluminum cast using this method allows for improved fuel efficiency in aircraft, providing both economic and environmental benefits.
Additionally, sand casting is often employed in the manufacturing of machinery components, decorative items, and consumer products. The flexibility of the process enables manufacturers to respond swiftly to changing market demands and custom orders, further enhancing its appeal for mass production.
Conclusion
In summary, sand casting is a vital process in the realm of mass production, combining cost-effectiveness with the ability to produce complex designs. Its adaptability to various metals and applications makes it a cornerstone in many industries. As technology continues to advance, sand casting is likely to evolve further, enhancing its efficiency and capabilities to meet the diverse needs of modern manufacturing.
Post time:Jul . 29, 2024 23:43
Next:Effective Techniques for Sanding Stainless Steel to Achieve a Smooth Finish and Enhance Appearance