Resin Bonded Sand Casting An Overview
Resin bonded sand casting is a modern casting process that has revolutionized the way metal components are produced. This method combines the advantages of traditional sand casting with the strength and versatility provided by resin binders, resulting in high-quality castings with improved surface finishes and dimensional accuracy.
The fundamental principle behind sand casting involves pouring molten metal into a mold made from sand. Traditionally, sand molds are created by mixing sand with clay as a binder, but the introduction of synthetic resin as a bonding agent has significantly enhanced the properties of sand molds. Resin bonded sand casting utilizes a mixture of fine sand and a thermosetting resin, typically phenolic or furan, which is activated by heat or catalyst. When heated, the resin hardens, forming a strong and rigid mold that can withstand the rigors of the casting process.
One of the key advantages of resin bonded sand casting is the superior surface finish it produces. The high strength of resin-bonded molds allows for finer grain sand to be used, resulting in smoother surfaces on the final product. This is particularly advantageous for applications where aesthetic appearance and tight tolerances are critical, such as in the automotive and aerospace industries. Manufacturers can achieve intricate shapes and complex geometries that would be challenging with traditional sand casting methods.
Additionally, this casting technique offers excellent dimensional accuracy. The stability of resin-bonded molds minimizes distortion during the casting process, ensuring that the final product closely matches the desired specifications. This accuracy can reduce machining time and costs, as less post-casting processing is required.
resin bonded sand casting
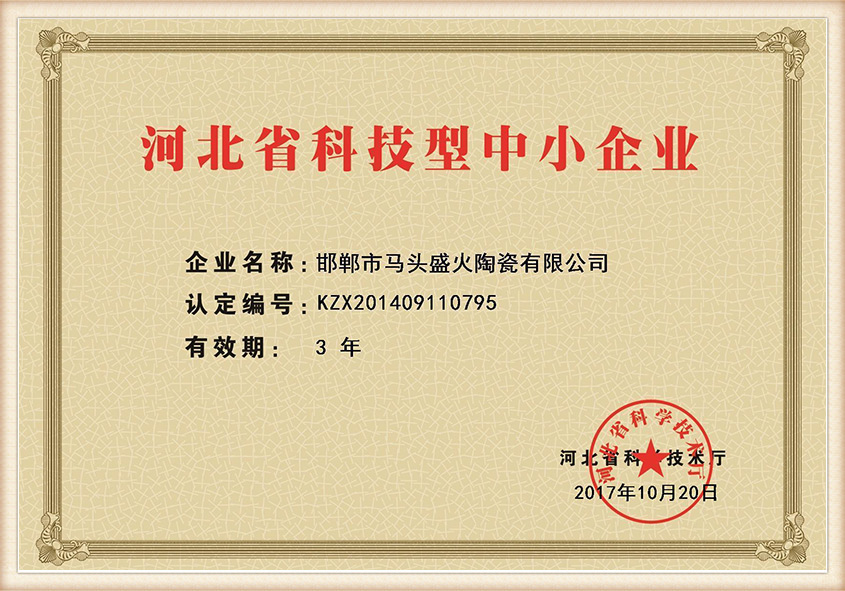
Another notable benefit of resin bonded sand casting is its ability to produce molds quickly
. The process is relatively rapid, allowing for shorter production cycles compared to other molding techniques. This makes it an ideal choice for low to medium volume production runs, enabling manufacturers to respond swiftly to changing market demands.Moreover, the use of resin as a binder enhances the thermal stability of the molds. This characteristic allows for the casting of a broader range of metals, including high-temperature alloys that may otherwise be unsuitable for traditional sand casting processes. Consequently, industries that require high-performance materials have increasingly turned to resin bonded sand casting for their production needs.
However, it is important to note that while resin bonded sand casting has numerous advantages, it does come with certain challenges. The resin used can emit volatile organic compounds (VOCs) during the curing process, raising environmental health concerns. Manufacturers must adopt adequate ventilation and proper waste management practices to mitigate these risks. Additionally, the cost of resin materials might be higher compared to traditional clay binders, which could affect the overall production cost, especially in high-volume settings.
In conclusion, resin bonded sand casting represents a significant advancement in casting technology. Its ability to produce high-quality, dimensionally accurate, and complex metal components has made it a preferred choice in various industries. While challenges exist, the benefits of improved surface finishes, rapid production, and expanded material compatibility continue to drive the adoption of this innovative casting method. As technologies advance and environmental concerns are addressed, the future of resin bonded sand casting looks promising, paving the way for even more applications in modern manufacturing.
Post time:Aug . 12, 2024 19:02
Next:Innovative Sand Casting Manufacturing Solutions for High-Quality Industrial Applications and Prototypes