The Importance of Sand Casting in Modern Manufacturing
Sand casting, one of the oldest and most widely used casting processes, continues to hold a prominent position in the manufacturing sector today. This versatile technique allows for the production of complex metal components with high precision, making it indispensable in various industries, from automotive to aerospace.
A sand casting factory typically begins its operations by creating a mold from sand. This involves mixing sand with a binding agent, usually clay, to allow the sand to hold its shape when compressed. The mixture is then packed into a mold pattern, which is usually made of metal or wood, shaped according to the specifications of the final product. Once the pattern is removed, the sand mold is ready for molten metal to be poured into it.
One of the key advantages of sand casting is its ability to produce large parts. The flexibility of sand molds allows manufacturers to create components of significant size and weight, something that is difficult to achieve with other casting methods. This capability is particularly beneficial in industries where large machinery and structural components are required, such as in the production of engines, frames, and heavy equipment.
In addition to its size versatility, sand casting is also remarkably cost-effective, especially for low to medium production runs. The materials used—primarily sand—are relatively inexpensive, and the molds can be reused for multiple casting cycles, leading to lower overall costs. This makes sand casting an attractive option for small and medium enterprises that may not have the budget for more complex manufacturing techniques.
sand casting factory
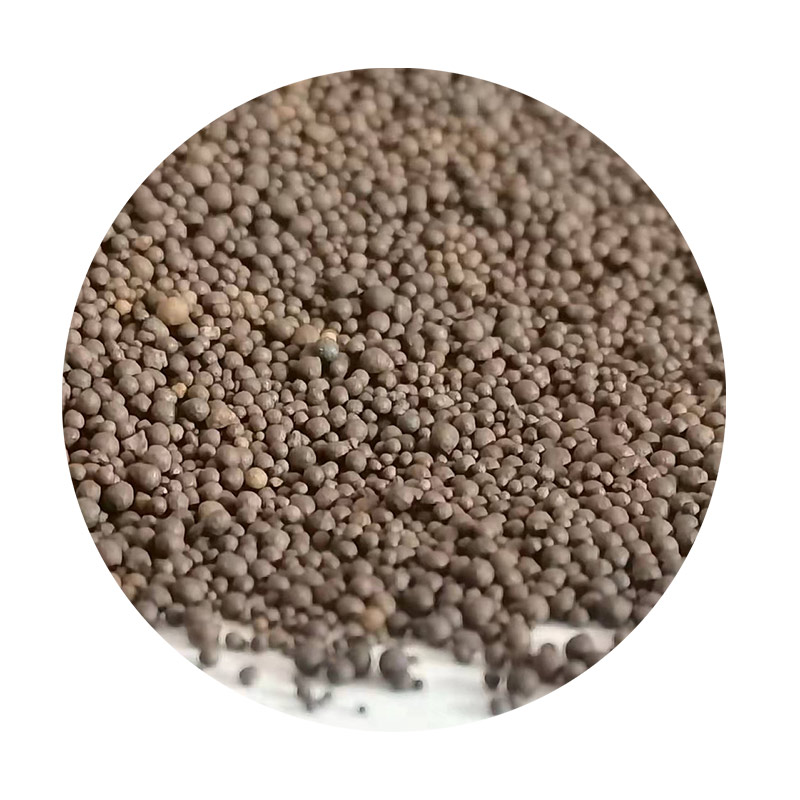
Moreover, the sand casting process is adaptable to various metals. While traditionally associated with iron and aluminum, advancements in materials science have broadened the types of alloys and metals that can be used, including copper and magnesium. This versatility allows manufacturers to meet specific mechanical and thermal properties required by different applications.
Quality control is a crucial aspect of operations in a sand casting factory. Adhering to stringent quality standards is essential to ensure that the final products meet the necessary specifications and performance criteria. This involves monitoring the entire casting process, from mold preparation to pouring and cooling, as well as inspecting the finished components for defects. Modern factories increasingly utilize advanced technologies, such as computer-aided design (CAD) and simulation software, to optimize mold designs and predict potential issues before physical production begins.
Sustainability also plays a vital role in the modern sand casting factory environment. Efforts to reduce waste and recycle materials are at the forefront of many operations. Sand can often be reused in multiple casting cycles, and advances in environmentally friendly binders are assisting factories in minimizing their ecological footprint. This commitment to sustainability not only fulfills regulatory requirements but also addresses growing consumer demand for environmentally friendly production practices.
In conclusion, sand casting remains a cornerstone of the manufacturing industry due to its versatility, cost-effectiveness, and ability to produce complex components. As the industry continues to evolve, sand casting factories are embracing new technologies and sustainable practices, ensuring their relevance in an increasingly competitive marketplace. With its ability to meet diverse engineering requirements and its adaptability to various metals, sand casting is poised to continue shaping the future of manufacturing for years to come.
Post time:Aug . 12, 2024 18:36
Next:Sustainable Practices for Reusing Foundry Sand in Environmental and Economic Applications