Types of Sand Used in Foundry Applications
The foundry industry plays a critical role in manufacturing, enabling the production of metal components through various casting processes. One of the fundamental materials used in foundry operations is sand, which serves as a mold material. The type of sand selected can significantly impact the quality of the final product, the efficiency of the casting process, and the overall costs involved. This article explores the various types of sand used in foundry applications and their unique characteristics.
1. Silica Sand
Silica sand, primarily composed of quartz, is the most commonly used sand in foundry applications. Due to its high melting point and excellent thermal conductivity, silica sand can withstand the high temperatures associated with metal casting. It is also well-suited for creating intricate mold designs, providing fine details and smooth surfaces. The grains of silica sand are angular in shape, which enhances the bonding capability when mixed with other materials. Additionally, silica sand is widely available and relatively inexpensive, making it a popular choice among foundries.
2. Green Sand
Green sand is not a specific type of sand but rather a mixture of silica sand, clay, water, and other additives. The term green refers to the fact that this sand mixture is used in its moist state. Green sand molds provide good collapsibility, which aids in the easy removal of the casting after solidification. It also boasts excellent moldability and retention of shape, making it ideal for creating complex shapes. The clay content in green sand gives it a degree of plasticity that allows manufacturers to produce reliable and durable molds. Foundries have utilized green sand for decades and continue to do so due to its cost-effectiveness and reliability.
3. Resin-Bonded Sand
types of sand used in foundry
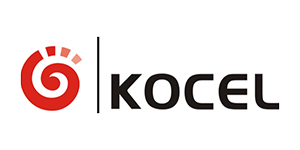
Resin-bonded sand has gained popularity in modern foundry applications due to its superior performance characteristics. This type of sand consists of silica grains bound together using synthetic resin. The resulting molds have exceptional strength, allowing them to withstand higher temperatures and more intricate designs than traditional green sand molds. Resin-bonded sand also has improved dimensional accuracy and surface finish, making it ideal for applications requiring high precision. However, the production cost is higher compared to green sand, which may be a consideration for some foundries.
4. V-Process Sand
The Vacuum Process (V-Process) employs a unique approach to mold making using specially designed sand that is compacted under vacuum. This high-tech process results in high-quality molds that exhibit excellent dimensional accuracy and surface finish. The sand used in V-Process molding is typically dry and non-bonded, creating molds that are easy to demold. Although this method is more expensive than traditional sand casting processes, the benefits in terms of casting quality and reduced need for machining can justify the higher costs.
5. Other Specialty Sands
In addition to the common types of sand mentioned above, there are several specialty sands used for specific applications in foundries. For instance, zircon sand and chromite sand are utilized in the casting of non-ferrous metals due to their superior thermal stability and resistance to metal penetration. These specialty sands can improve the casting's performance and longevity, although they often come at a higher price point.
Conclusion
The type of sand used in foundry applications is a crucial factor influencing the quality and efficiency of the casting process. While silica sand and green sand remain the most commonly employed materials, innovations such as resin-bonded sand and V-Process sand are paving the way for enhanced casting capabilities. Foundries must carefully consider the properties and costs associated with each type of sand to optimize their operations and meet the demands of their clients. By understanding the various types of sand available, foundries can make informed decisions that lead to better casting outcomes and increased competitiveness in the market.
Post time:Aug . 14, 2024 12:36
Next:Comparing Die Casting and Sand Casting Techniques for Optimal Metal Fabrication Solutions