The Difference Between Die Casting and Sand Casting
Casting is a fundamental manufacturing process used in various industries to create metal parts and components. Among the various casting methods, die casting and sand casting are two of the most prominent techniques, each offering unique advantages and disadvantages. Understanding the differences between these two methods is crucial for selecting the appropriate process for specific applications.
Die Casting
Die casting is a high-pressure casting process where molten metal is injected into a mold cavity under high pressure. The molds, typically made from steel, are designed to create precise and complex shapes. Due to the nature of die casting, it allows for rapid production rates, making it ideal for large-scale manufacturing.
One of the key advantages of die casting is the excellent surface finish and dimensional accuracy it achieves. The high pressure forces the molten metal into the mold, which fills the cavity completely and ensures minimal defects. This precision reduces the need for post-processing, saving both time and costs. Additionally, die casting is suitable for non-ferrous metals, such as aluminum, zinc, and magnesium, which possess good fluidity and can be cast into intricate designs.
However, die casting comes with its limitations. The initial setup costs for the molds can be quite high, making it less economical for small production runs. Furthermore, the complexity of the design can affect the mold’s lifespan, as intricate shapes may cause wear and tear over time.
Sand Casting
difference between die casting and sand casting
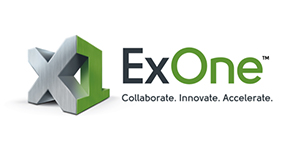
In contrast, sand casting is a more traditional and versatile casting process. It involves creating a mold from sand, typically mixed with a binding agent. The molten metal is poured into the sand mold, where it cools and solidifies to form the desired part. Sand casting is widely used for both ferrous and non-ferrous metals, making it a more flexible option compared to die casting.
The primary advantage of sand casting is its low production costs. Since the molds are made from sand, which is readily available and inexpensive, the initial investment is significantly lower than that of die casting. Additionally, complex shapes can be easily achieved without the need for intricate mold designs, and the sand molds can be reused for subsequent castings.
However, sand casting does have its drawbacks. The surface finish is generally not as smooth as that produced by die casting, which may require additional machining to achieve the desired specifications. Moreover, the dimensional accuracy of sand casting may be inferior to that of die casting, leading to potential variances in the final product.
Conclusion
In summary, die casting and sand casting are two widely used metal casting techniques, each with its own set of advantages and disadvantages. Die casting excels in terms of precision, surface finish, and production speed, making it suitable for high-volume manufacturing of complex components. However, its high initial costs can be prohibitive for smaller runs.
On the other hand, sand casting offers flexibility and lower costs, making it an ideal choice for prototyping or low-volume production. Despite its limitations in surface finish and dimensional accuracy, sand casting remains a valuable technique in various industries.
When deciding between die casting and sand casting, manufacturers must consider factors such as production volume, material type, part complexity, and budgeting constraints. By understanding the differences between these two methods, companies can make informed decisions that align with their manufacturing needs.
Post time:Aug . 14, 2024 12:09
Next:Step-by-step Guide to Effectively Sanding Your 3D Printed Models for a Smooth Finish