Exploring the Art of 3D Printing with Sand
In the realm of additive manufacturing, 3D printing continues to revolutionize industries by enabling the creation of complex geometries that were once unimaginable with traditional methods. One innovative technique gaining traction is 3D printing with sand, a process that combines the traditional craft of sandcasting with modern technology to produce intricate and functional objects. This article delves into the intricacies of 3D printing with sand, its applications, benefits, and future prospects.
The Process of 3D Printing with Sand
3D printing with sand, often referred to as sand 3D printing or sand casting, employs a binder jetting technique. In this process, a 3D model is created using CAD (Computer-Aided Design) software, which is then sliced into cross-sectional layers. The printer deposits a layer of sand, typically a mix of silica sand, and selective binder material. A print-head moves across the sand bed, depositing the binder in the pattern dictated by the 3D model.
Once the layer is complete, the process is repeated, building up layers until the entire object is formed. After the printing is finished, the non-bonded sand is removed, leaving behind a solid, intricately designed piece. This method allows for a high degree of customization and is especially beneficial for producing complex geometries that would be difficult or impossible to achieve using traditional sandcasting techniques.
Applications of Sand 3D Printing
The application of 3D printing with sand extends across various industries. One of the most significant areas of impact is in the manufacturing sector, particularly for creating molds for metal casting. By using sand 3D printing, manufacturers can produce molds with complex internal features that are tailored to specific designs. This capability reduces material waste and shortens lead times, ultimately resulting in cost savings.
In addition to industrial applications, 3D printing with sand has found its way into architectural and artistic realms. Artists are experimenting with this technology to create large-scale sculptures and installations, while architects are utilizing sand 3D printing to prototype intricate structures. The possibilities are virtually limitless when it comes to the creative potential of sand-based 3D printing.
fill 3d print with sand
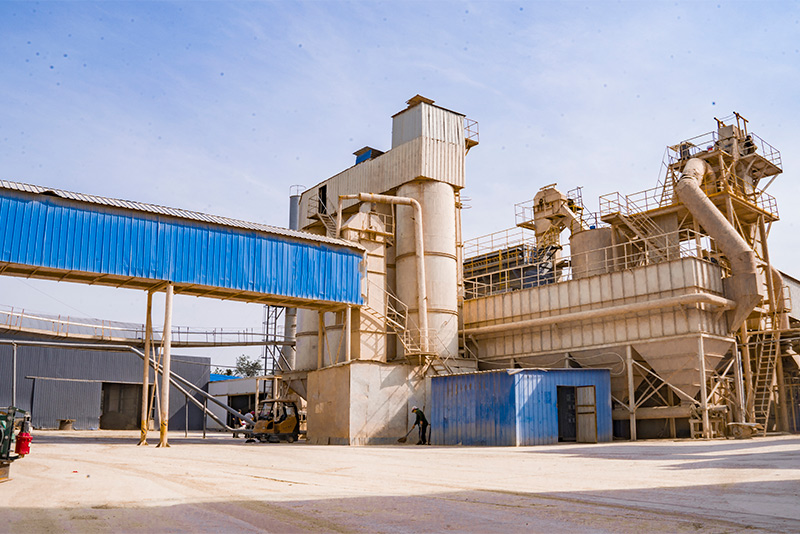
Benefits of 3D Printing with Sand
One of the standout benefits of 3D printing with sand is its sustainable nature. Sand is an abundant resource, and the process generates less waste compared to traditional manufacturing methods. Furthermore, the ability to recycle sand from previous prints means that the environmental impact is minimized, making it an attractive option for eco-conscious companies.
Another advantage is the speed of production. With traditional sandcasting methods, creating molds can be a time-consuming process. In contrast, sand 3D printing significantly reduces the time required to go from design to finished product. This rapid prototyping ability allows for quicker iterations and improvements, fostering innovation.
The Future of Sand 3D Printing
As technology continues to advance, the future of 3D printing with sand looks promising. Ongoing research aims to enhance the materials used in the process, including developing different types of binders that could expand the range of applications. Additionally, the integration of AI and machine learning may optimize designs and improve overall efficiency in sand 3D printing.
Moreover, as industries increasingly seek sustainable practices, sand 3D printing's eco-friendly advantages position it well within the green manufacturing movement. Its potential to reduce waste and utilize natural resources optimally could make it a staple in future manufacturing processes.
Conclusion
In conclusion, 3D printing with sand is an exciting and innovative technology that blends traditional practices with modern advancements. Its applications across various industries, combined with its sustainability and efficiency benefits, point toward a bright future. As we continue to explore and develop this technology, the possibilities for creating intricate, customized products will only expand, thus redefining manufacturing and artistry in the years to come.
Post time:Aug . 19, 2024 04:45
Next:Innovative Techniques in 3D Printing for Enhanced Sand Casting Processes