3D Printed Sand Casting Revolutionizing the Foundry Industry
In recent years, the advent of 3D printing technology has significantly transformed various industries, and the foundry sector is no exception. Specifically, 3D printed sand casting is emerging as a game-changer, offering innovative solutions to traditional manufacturing challenges. This process not only enhances manufacturing efficiency but also promotes sustainability, flexibility, and design freedom.
At its core, 3D printed sand casting involves using 3D printing technology to create molds for sand casting. Traditional sand casting methods require significant labor and time investment for mold creation, as patterns need to be crafted from materials such as wood or metal. These patterns can be costly and time-consuming to produce, especially when small adjustments are needed. However, with 3D printing, manufacturers can create intricate and complex molds directly from digital designs without the need for physical patterns.
3D Printed Sand Casting Revolutionizing the Foundry Industry
Moreover, 3D printing allows for greater design complexity that would be difficult or impossible to achieve with traditional methods. Engineers can create molds with intricate geometries, internal channels, and cooling features that enhance the performance of the final casted product. This level of design freedom encourages innovation and experimentation, paving the way for the development of new products and solutions.
3d print sand casting
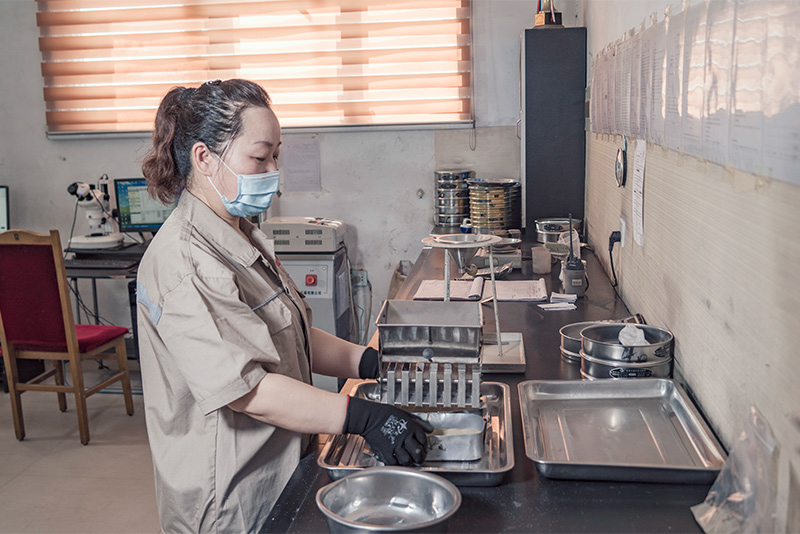
In addition to improving design capabilities, 3D printed sand casting contributes to sustainability in manufacturing practices. Traditional sand casting generates significant waste, as excess material must be removed and discarded. In contrast, 3D printing produces molds with minimal waste, as the material is only used where necessary. Furthermore, many 3D printing technologies for sand casting utilize eco-friendly materials, such as recyclable sand and biodegradable binders, reducing the environmental impact of the casting process.
Cost efficiency is another critical aspect of 3D printed sand casting. While the initial investment in 3D printing technology may be substantial, the long-term savings can be significant. Reducing material waste, minimizing labor costs associated with traditional mold-making, and decreasing lead times all contribute to a more cost-effective production process. Additionally, the ability to produce low-volume runs without the need for new tooling makes it easier for smaller businesses and startups to enter the market.
Despite the numerous advantages, the widespread adoption of 3D printed sand casting still faces challenges. The technology is continually evolving, and manufacturers must invest in training and skill development to keep up with new advancements. Moreover, ensuring the quality of castings produced from 3D printed molds is crucial, as variations in mold design can directly affect the final product's properties.
In conclusion, 3D printed sand casting represents a significant leap forward in the foundry industry, offering unparalleled advantages in speed, design flexibility, sustainability, and cost efficiency. As industries continue to embrace digital manufacturing, the integration of 3D printing into sand casting processes will likely become more prevalent. This evolution not only addresses the challenges faced by traditional methods but also paves the way for innovative designs and products that can push the boundaries of what is possible in manufacturing. The future of sand casting is undoubtedly bright, and 3D printing is at the forefront of this transformation.
Post time:Aug . 19, 2024 04:16
Next:Applications of Sand Casting in Manufacturing and Production Processes